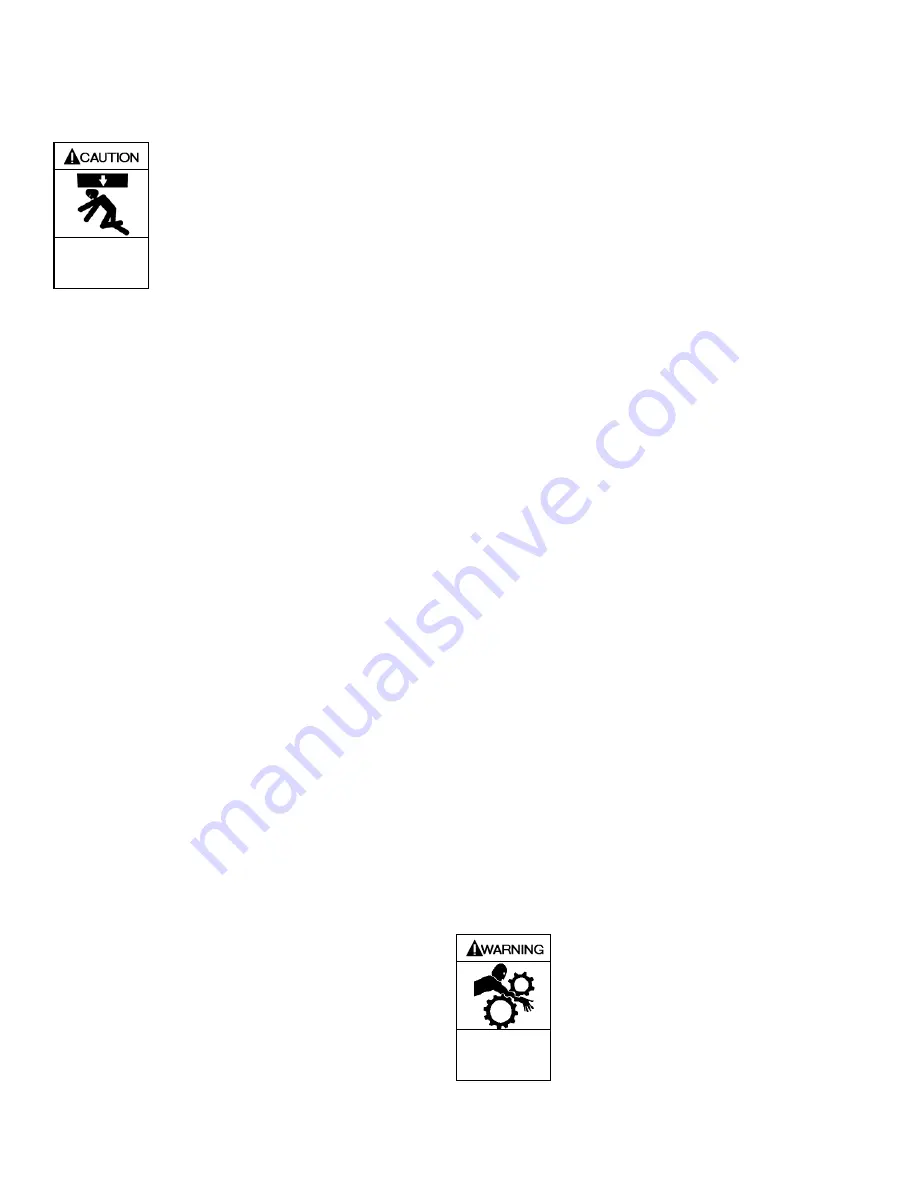
1301-C00 page 18/56
6.0 MOUNTING THE MOTOR
With the pump mounted without a soft foot and the discharge
flange level, mount the motor in one of two different methods
as follows:
6.1 Foot Mounted Motor
Pump and components are heavy.
Failure to properly lift and support
equipment could result in physical
injury or damage to the pump. Steel
toed shoes should be worn at all times.
Heavy assemblies
can cause personal
injury or porperty
damage.
In most cases, it will be necessary to install spacer blocks
under the motor feet to obtain proper motor support and
elevation. Allow for additional space under the motor feet of at
least 0.12 in. (3 mm) for shim stock to allow for proper motor
alignment.
A check for soft foot should be performed on the motor feet.
This “Soft Foot Check Procedure” can be used during the
initial shimming process or upon completion of the preliminary
alignment:
1. Tighten all hold-down bolts or nuts to approximately fifty
percent of torque value on the unit (pump and motor) to
be shimmed.
2. Secure a dial indicator base to the pump baseplate, or
suitable surface. The dial indicator stem is placed
vertically on the top edge of the foot to be checked. Zero
the dial indicator. Completely loosen the hold-down bolts
or nuts on that foot only. Watch dial indicator for foot
movement during the loosening process.
3. If the foot rises from the base when the hold-down bolts or
nuts are loosened, place shim stock equal to the amount
of deflection shown on the dial indicator under the foot.
Soft foot readings less than or equal to 0.005 in. (0.13
mm) require no corrections.
4. Tighten the hold-down bolt or nut and repeat the entire
process until no movement is present.
5. Move the dial indicator to the next foot and repeat the
above process.
6. Repeat until all feet have been checked and corrected as
necessary.
Remember: All other feet must remain securely
tightened when a foot is being checked for soft foot.
6.2 Coupling
Install a spacer type coupling between the pump and motor.
The pump and motor are now ready for alignment.
Shaft gaps are as follows for pumps not using motor adapters:
Frame SD: 3.94 in. (100 mm)
Frame S and Frame A: 3.63 in. (92 mm)
Frame M: 5.25 in. or 7.25 in. (133 mm) or (184 mm)
6.3 Motor Mounted on C-Frame or D-Flange Motor
Adapter
Wiring the motor with flexible conduit will allow simple removal
of the power end when servicing the pump.
NOTICE:
The coupling end of the pump bearing frame has a male
fit for mounting the motor adapter which must be cleaned
to bare metal. Remove all the paint and debris from the
radial fit and the face fit surfaces. Failure to do so will
result in poor coupling alignment.
1. Attach the motor adapter to the pump bearing frame (19).
Be sure to alternately tighten the bolts to maintain correct
alignment.
2. Install the coupling hubs on the pump and motor shafts.
3. Fasten the pump feet to the baseplate.
4. Bolt motor to motor adapter. Use a lifting device to
support the motor while attaching to the motor adapter. If
there is a small gap between the motor feet and the
support blocks, it must be completely filled with shims
while the motor is supported by the lifting device. This will
prevent motor adapter distortion that could result in shaft
misalignment.
5. After shimming, remove the motor support and fasten the
motor feet to the mounting blocks.
6. Motor frames 140 to 210TC weighing less than 183 lb (83
kg) can be suspended from the C-frame adapter without
additional support.
7. Motor frames 250TC weighing up to 309 lb. (140 kg) can
be supported by support feet (available from the factory)
under the two rear motor feet (except Frame SD and S
which requires 1 in. (25 mm) pads under the pump).
8. Motor frames 280TC and up, weighing more than 309 lb.
(140 kg) must be supported by and bolted to solid pads
under all four feet.
NOTICE:
Large motors may result in a slight deflection of the
motor adapter. Failure to follow this procedure below
may result in damage to pump and/or motor during
operation.
To insure proper alignment of motor and pump shafts, the
following procedures should be followed:
Externally mount a dial indicator to read movement of
the motor adapter motor end flange. Zero indicator
once it is in place.
Mount motor to C-frame adapter, noting any changes
to indicator reading.
a. If no change occurs, insert shims between motor
feet and motor pads such that all motor weight is
taken off the motor adapter. Secure the motor to
the base and check “soft foot” per section 6.1.
b. If the indicator reading shows movement, the
motor must be lifted and shimmed until the
indicator reading returns to zero and all the motor
weight is taken off the adapter. After inserting
shims between motor feet and motor pads, check
“soft foot” per section 6.1.
Fully torque all motor hold-down bolts before
operating motor.
9. Assemble and lubricate the coupling as required by the
coupling manufacturer.
10. Install coupling guard.
Never operate pump without coupling
guard properly installed. Personal
injury can occur if pump is operated
without coupling guard.
Do not operate
without guard in
place.
Summary of Contents for SYSTEM ONE
Page 27: ...1301 C00 page 26 56 8 2 Pump Assembly Parts List Frame S Horizontal 6 1 ...
Page 28: ...1301 C00 page 27 56 8 3 Pump Assembly Parts List Frame S Horizontal 8 ...
Page 29: ...1301 C00 page 28 56 8 4 Pump Assembly Parts List Frame A and IPP Frame A ...
Page 30: ...1301 C00 page 29 56 8 5 Pump Assembly Parts List LD17 and IPP LD17 ...
Page 31: ...1301 C00 page 30 56 8 6 Pump Assembly Parts List Vortex Frame A and IPP Vortex Frame A ...
Page 32: ...1301 C00 page 31 56 8 7 Pump Assembly Parts List Vortex LD17 and IPP Vortex LD17 ...
Page 33: ...1301 C00 page 32 56 8 8 Pump Assembly Parts List Frame M ...
Page 55: ...1301 C00 Page 54 56 notes ...
Page 56: ...1301 C00 Page 55 56 notes ...