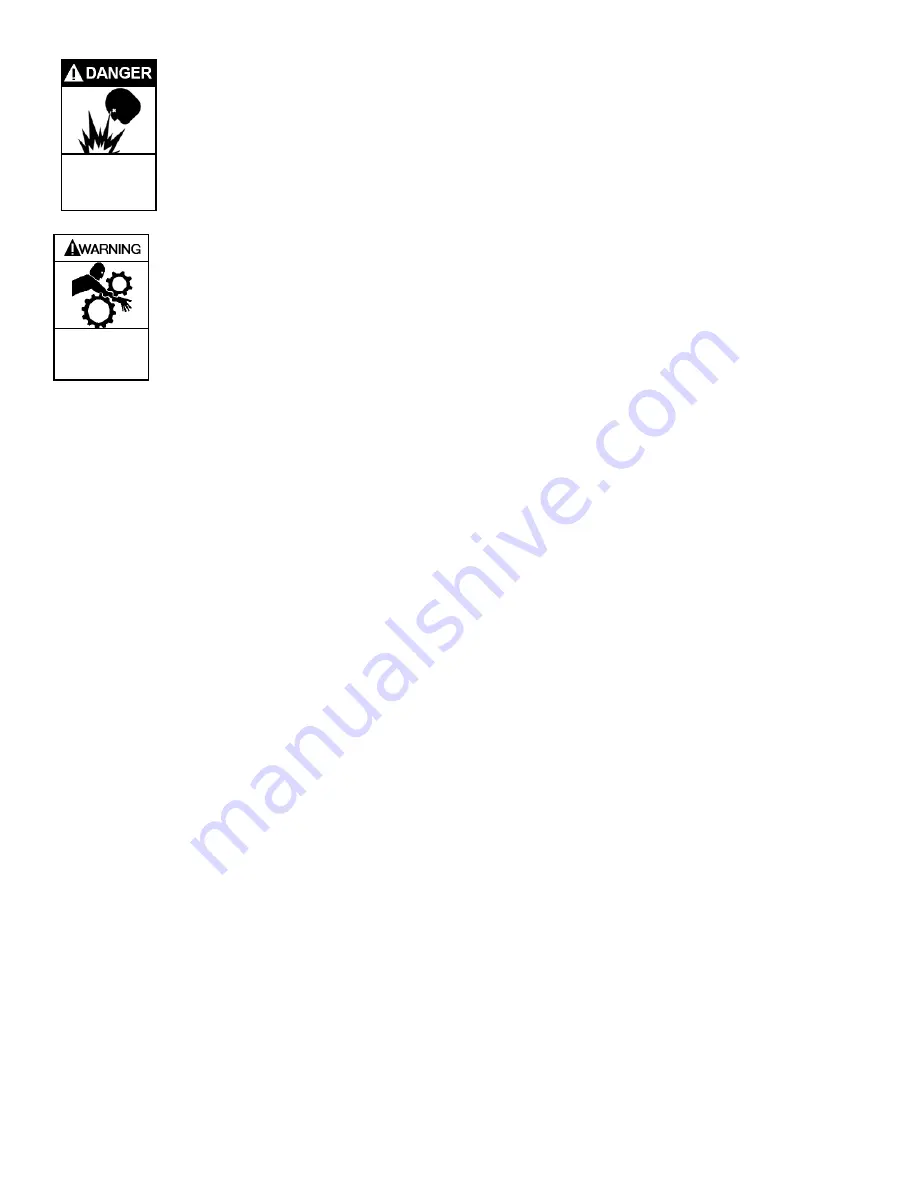
1301-C00 page 14/56
Never use heat to remove parts. Use of
heat may cause an explosion due to
trapped fluid resulting in physical injury
and property damage.
Explosive fluids will
cause severe
personal injury
death or major
property damage.
Wear heavy work gloves when handling
impellers as sharp edges may cause
physical injury.
Hazardous
machinery can
cause serious
personal injury.
2. Install the mechanical seal centering clips if available.
Remove the seal gland stud nuts. Remove
backcover/frame adapter nuts quantity 2 except for 13 in.
Frame A pumps which have quantity 8, then remove the
back cover (11) assembly from the frame adapter (71).
Loosen the set screws on the mechanical seal to free it
from the shaft (6), then remove the seal.
3. Drain the oil from the bearing frame (19) by removing the
plug (414) below the oil level sight glass (143). If the
optional System One temperature monitor is installed, it is
removed to drain oil.
4. If the power end is to be completely disassembled,
remove the motor adapter at this time.
5. Remove the frame adapter/bearing frame screws (quantity
4 for Frame A, quantity 8 for Frame M) and remove the
frame adapter (71) from the bearing frame (19)(not
applicable to Frame SD and S).
6. Clean and lubricate the shaft surface to facilitate removal
of the labyrinth seal. In doing so, the rotor portion of the
radial labyrinth seal (89E) with two flourocarbon (FKM) O-
rings (89F) will slide off the shaft (6).
7. Press out the stator (89D) portion of the radial labyrinth
seal if replacement is required (not applicable to Frame
SD and S as the stator is integral to the bearing frame).
For Frame M pumps, the radial labyrinth rotary seal (89E)
will not be removed with the frame adapter (71) as it is
part of the radial labyrinth seal acting as a radial bearing
cover.
Remove and Disassemble the Rotating Element
1. The rotating element assembly can now be removed from
the bearing frame (19) (after removal of C-frame or D-
flange motor adapter if supplied). Remove the cartridge
lock nuts (404), quantity 3 for Frame SD, S and A,
quantity 4 for Frame M. Slide the rotating element out
from the back end of the bearing frame (19).
2. The micrometer nuts (66) can be used to help disengage
the cartridge O-ring (405) from the bearing frame (19)
3. The rotating element assembly can now be disassembled.
Remove the pump half of the coupling from the shaft (6) if
this has not already been done.
4. Remove the bearing retainer screws and the bearing
retainer cover (35) from the cartridge (33).
5. Clean and lubricate the shaft surface at the motor end to
facilitate removal of the labyrinth seal. Remove the
cartridge (33) with O-ring (405) from the rotating element.
In doing so, the rotor portion of the thrust labyrinth seal
(89B) with two O-rings (89C), will slide off the shaft.
6. Press out the stator portion of the labyrinth seal (89A)
from the cartridge if replacement is necessary. Applies
only to pre-2000 Frame A and LD17 models. All others
have stators as part of the thrust cartridge.
7. Bend out the locking tab from the locking slot in the lock
nut (22). Remove the thrust bearing lock nut (22) and lock
washer (69). The threads on the shaft are right hand.
For detailed instructions on handling and removing
bearings, see section 12.0
8. Press the thrust bearings (18) from the shaft (6) using an
arbor press. A fixture is necessary (split steel plate with a
bored hole of the same diameter as the maximum shaft
diameter) to hold the shaft in the arbor press by the inner
race of the bearing and to allow the press arbor to contact
the end of the shaft. Care is necessary so that the shaft is
not scratched or bent. Shaft must be perfectly aligned
under the arbor. Do not use a hammer or other tools that
may damage the shaft.
NOTICE:
Always press on the inner race of the bearings when
removing from a shaft.
9. Press the radial bearing (16) from the shaft (6) in the
same manner.
10. Loosen the flinger set screw and remove the flinger (62)
along with the bearing retainer cover (35) from the shaft
(6). Frame S pumps do not have a flinger.
4.2 Assembly Procedure
See appropriate pump assembly drawing in section 8.0.
See Fastener Torque Chart section 11.0.
Assemble Rotating Element
1. Clean all parts thoroughly, especially gasket surfaces, fits,
and the inside of the oil sump.
2. Replace all O-rings, gaskets, thrust bearings, the radial
bearing, and mechanical seal wear parts.
3. Inspect all remaining parts and determine if they should
be reused, repaired or replaced. Use good judgement for
a successfully reconditioned pump.
See Pump Component Inspection section 13.0 and Pump
Tolerances 10.0.
4. Slide the flinger (62) on the shaft (6). The Frame SD and
S have no flinger.
5. Mount the bearing retainer cover (35) loosely on the shaft
(6) with the smaller diameter ring facing toward the
coupling end.
For detailed instructions on Bearing Installation see
section 12.0
6. Heat the thrust bearing(s) (18) in hot oil, or with an
induction heater, to a temperature of 240°F (116°C).
Using clean, insulated gloves, mount the hot thrust
bearings back-to-back (letters to letters) on the coupling
end of the shaft (6). For Frame SD, A and M, be sure the
bearings are tight against each other. The standard
Frame S thrust bearing is one piece only and can be
mounted in either direction (except for optional angular
contact bearings). Make sure bearings are seated against
shaft shoulder.
Summary of Contents for SYSTEM ONE
Page 27: ...1301 C00 page 26 56 8 2 Pump Assembly Parts List Frame S Horizontal 6 1 ...
Page 28: ...1301 C00 page 27 56 8 3 Pump Assembly Parts List Frame S Horizontal 8 ...
Page 29: ...1301 C00 page 28 56 8 4 Pump Assembly Parts List Frame A and IPP Frame A ...
Page 30: ...1301 C00 page 29 56 8 5 Pump Assembly Parts List LD17 and IPP LD17 ...
Page 31: ...1301 C00 page 30 56 8 6 Pump Assembly Parts List Vortex Frame A and IPP Vortex Frame A ...
Page 32: ...1301 C00 page 31 56 8 7 Pump Assembly Parts List Vortex LD17 and IPP Vortex LD17 ...
Page 33: ...1301 C00 page 32 56 8 8 Pump Assembly Parts List Frame M ...
Page 55: ...1301 C00 Page 54 56 notes ...
Page 56: ...1301 C00 Page 55 56 notes ...