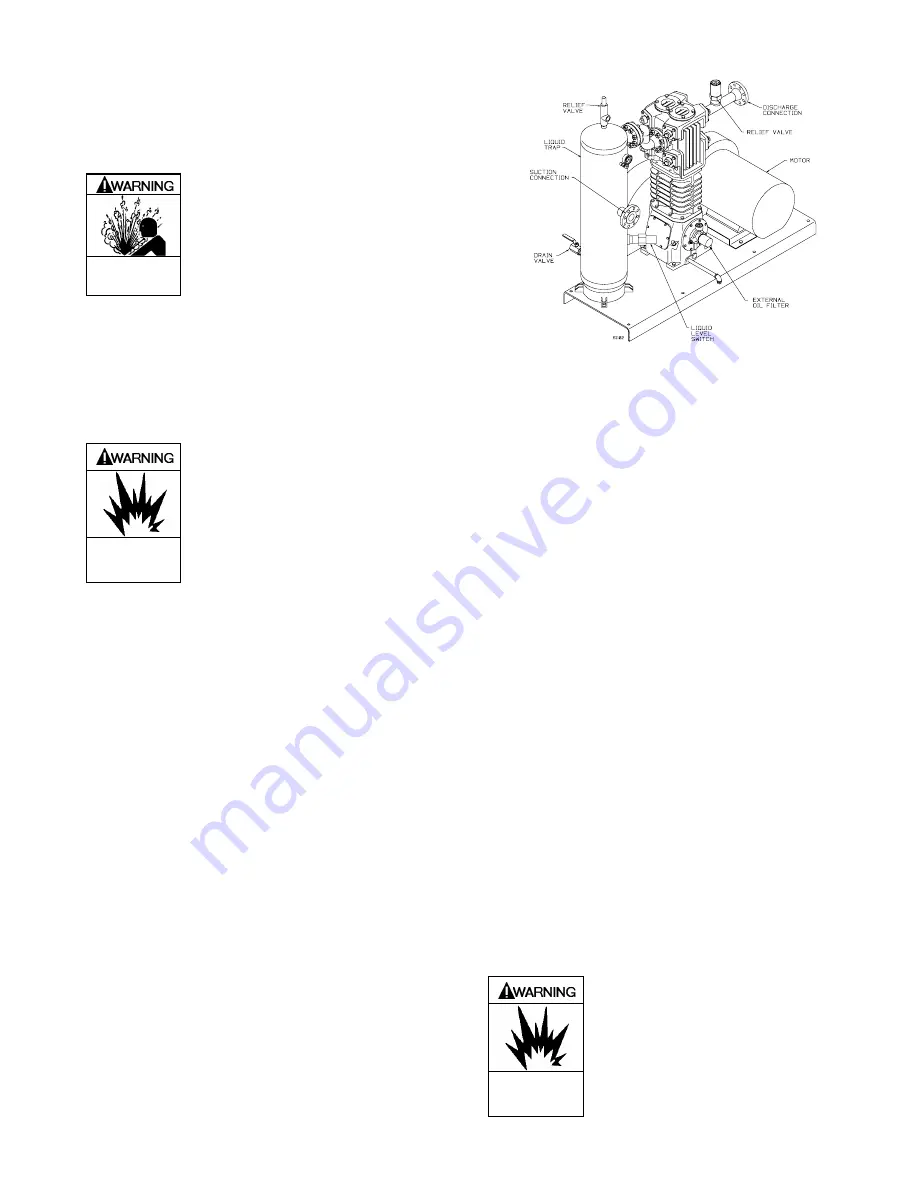
INSTALLATION
CB9A-030 page 9/28
RELIEF VALVES
A relief valve of a type, material and pressure rating
suitable to the installation, MUST be installed. The
relief valve shall be installed in the discharge line
between the compressor head and the first block valve.
Hazardous pressure
can cause serious
personal injury or
property damage
Compressor operating against closed
valve can cause system component
failure, personal injury or property
damage.
Since all systems differ in design, care must be taken to
ensure the relief valve is installed to safely vent away
from sources of ignition and personnel. This can be
accomplished by either orientation or a pipe away,
consult the Relief Valve manufacture for assistance.
Should the Relief Valve actuate, the cause MUST be
determined and corrected before continuing operations.
See the 'Troubleshooting' section.
Hazardous gases
can cause property
damage, personal
injury or death
Operation of the relief valve can release
explosive gas to the atmosphere
creating an explosion hazard, possibly
causing personal injury or death
Blackmer offers various relief valves for gas and
application compatibility.
PRESSURE GAUGES
Install pressure gauges in the discharge and inlet lines
to verify actual suction and discharge pressures.
LIQUID TRAPS
Compressors handling gasses that contain
condensates or other liquids MUST be protected from
entry of the liquid. Liquid can also enter the compressor
from the discharge piping, particularly if the piping
slopes down toward the compressor. To prevent liquid
from entering the compressor and causing major
damage, it is necessary to carefully consider the system
design and have strict procedures for operation.
NOTICE: Liquid in the compressor cylinder can
cause destruction of the compressor.
Suction liquid traps collect liquid entrained in the suction
gas stream, preventing it from entering the compressor.
The most common liquid trap is an ASME code vessel
(approx. 12" diameter X 50" tall) fitted with an internal
stainless steel mist pad, a relief valve, a manual drain
valve, and one or two electric float switches. Level
gauges and automatic drain systems are also available.
If the liquid level rises too high in the trap, a float switch
is tripped, sending a signal to stop the compressor or
sound an alarm. The trap must then be drained before
the compressor can be restarted. The cause of the high
liquid level must be found and the problem corrected.
Figure 5 – Typical HD942 Compressor Package
4-WAY VALVES
Many liquefied gas compressors are used for both liquid
transfer and vapor recovery operations. An optional 4-
way valve is used to reverse the direction of flow
through the system when changing from liquid transfer
to vapor recovery. Both lubricated and nonlubricated
models are available. Lubricated models should be
lubricated every 6 months.
TEMPERATURE SWITCHES
Excessive discharge temperature is a leading cause of
premature component failure and is often an early
warning sign of impending problems.
Optional temperature switches should be installed with
a thermowell as close to the compressor discharge as
possible. The switch should be set to actuate at a
temperature just above the maximum operating
temperature of the compressor.
ATEX compliant compressors
must
have a temperature
switch installed.
LOW OIL PRESSURE SWITCHES
Loss of crankcase oil pressure is a rare occurrence, but
can result in costly damage. An optional low oil
pressure switch set at about 15 psig (1 bar-g) may be
installed to shut down the compressor in the event of a
lubrication failure. A 10 second delay timer should be
used to lock the low oil pressure switch out during
compressor startup.
PRESSURE SWITCHES
Pressure switches may be installed in the suction or
discharge gas stream as protective devices, for
compressor control, or for other uses varying with each
application and system design.
Hazardous gases
can cause property
damage, personal
injury or death
Optional liquid trap level switches,
temperature switches, pressure
switches or other electrical devices
must be properly specified for
applications using explosive gases.
Summary of Contents for HD942A
Page 26: ...NOTES CB9A 030 page 26 28...
Page 28: ...1528 3 e 5...