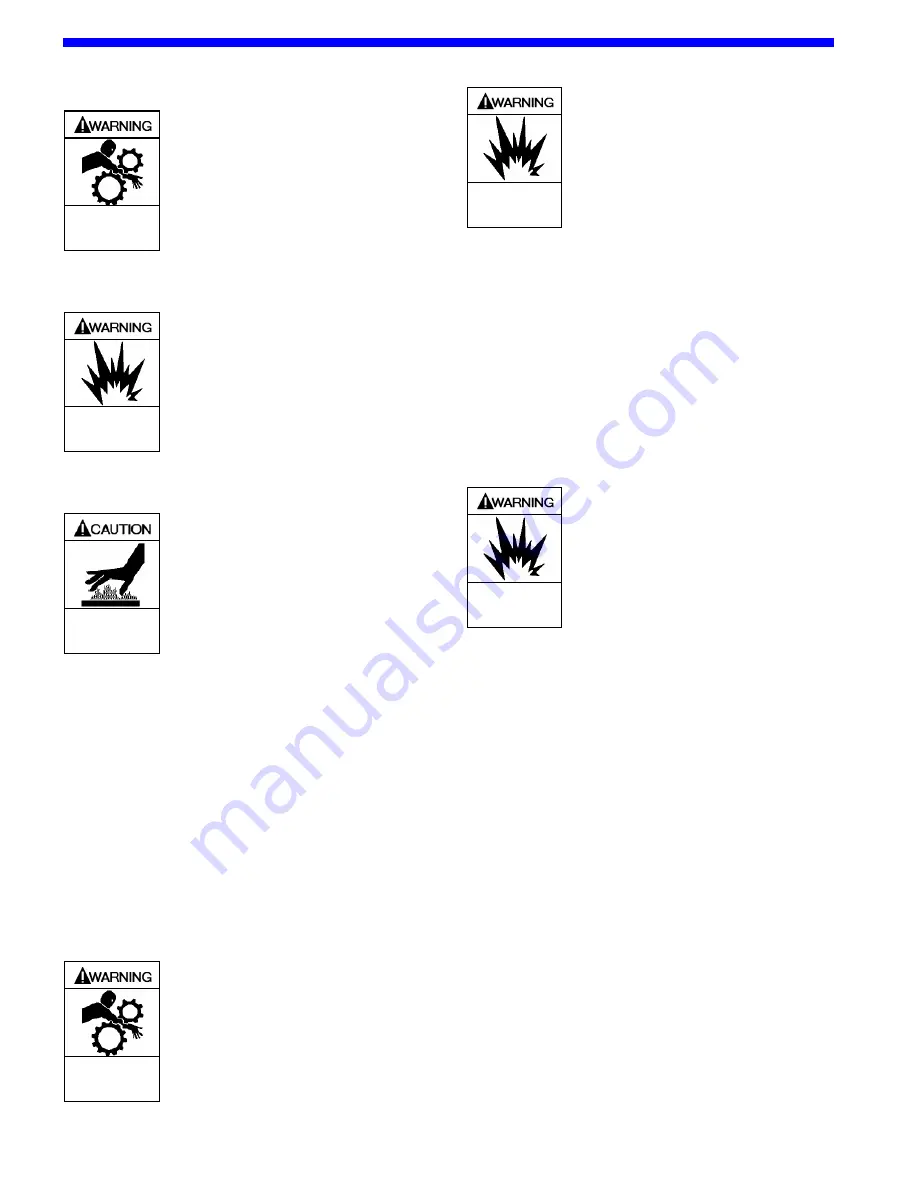
OPERATION
CB9A-030 page 10/28
PRE-STARTUP CHECK LIST
Hazardous
machinery can
cause serious
personal injury.
Failure to disconnect and lockout
electrical power or engine drive before
attempting maintenance can cause
severe personal injury or death
1. After the compressor is installed in the system, a
complete leak test MUST be performed on both the
compressor and the piping.
Hazardous gases
can cause property
damage, personal
injury or death
Failure to properly leak test the
compressor installation may result in
leakage of explosive gas to the
atmosphere creating an explosion
hazard, possibly causing severe
personal injury or death.
2. Re-check the system piping and the piping supports
to ensure that no piping loads are being placed on
the compressor.
Extreme Heat can
cause personal injury
or property damage
Discharge piping surface temperatures
may be hot during operation (over
158°F, 70°C). Temperatures should be
monitored and adequate warnings
posted.
3. If V-belt driven, check the alignment of the motor
and the compressor sheaves. The faces of the
sheaves must be parallel.
4. Ensure that pressure gauges are installed on both
inlet and discharge of the compressor.
5. Blackmer compressors are shipped from the factory
without oil in the crankcase. Fill with a high quality
non-detergent oil of the proper viscosity. See
"Crankcase Lubrication" in this manual.
6. Check the electrical connections for proper wiring,
grounding, etc.
7. With the power disconnected, remove the
compressor nameplate. Squirt oil onto each
crosshead while rotating the compressor by hand to
verify smooth operation.
8. Ensure that all guarding is properly installed.
Hazardous
machinery can
cause serious
personal injury.
Operation without guards in place can
cause serious personal injury, major
property damage or death.
Hazardous gases
can cause property
damage, personal
injury or death
Flywheel guard contact with moving
parts may be a source of ignition in
explosive atmospheres causing severe
personal injury or death
STARTUP PROCEDURE
NOTICE:
Consult the 'troubleshooting' section of this manual if
difficulties during startup are experienced.
1. Start the compressor. Oil pressure should register
25 psig (1.7 bar-g) within 10 seconds.
If proper oil pressure is not present, stop the
compressor and correct the problem.
Operating the compressor with low oil pressure will
cause severe damage to the unit. Adjust if
necessary. See "Setting the Oil Pressure" in this
manual.
Hazardous gases
can cause property
damage, personal
injury or death
Operation of the compressor with low or
no oil may result in extreme
temperature in the crankcase. This
could be an ignition source in the
presence of explosive gas and could
lead to severe personal injury or death.
The oil pump on these models will operate in either
direction of crankshaft rotation.
2. Verify that the suction and discharge pressures are
within the expected ranges.
Operating limits listed in the "Compressor Data"
section must not be exceeded.
3. Check for leakage from the piping and equipment,
and repair as necessary.
4. If the seals (packing) have just been replaced, or if
the compressor has been out of service for over 6
months, the lower seal MUST be manually
lubricated during the first 60 minutes of operation.
See "Seal (Packing) Replacement" section. New
compressors have had the packing broken in at the
factory.
5. On newly rebuilt units, the valve hold down screws,
valve cover plate bolts and cylinder head bolts
MUST have their torque checked after 60 minutes
running time. Also re-tighten all hold down bolts,
flywheel bolts, etc. after 60 minutes running time.
See the "Bolt Torque." table.
Summary of Contents for HD942A
Page 26: ...NOTES CB9A 030 page 26 28...
Page 28: ...1528 3 e 5...