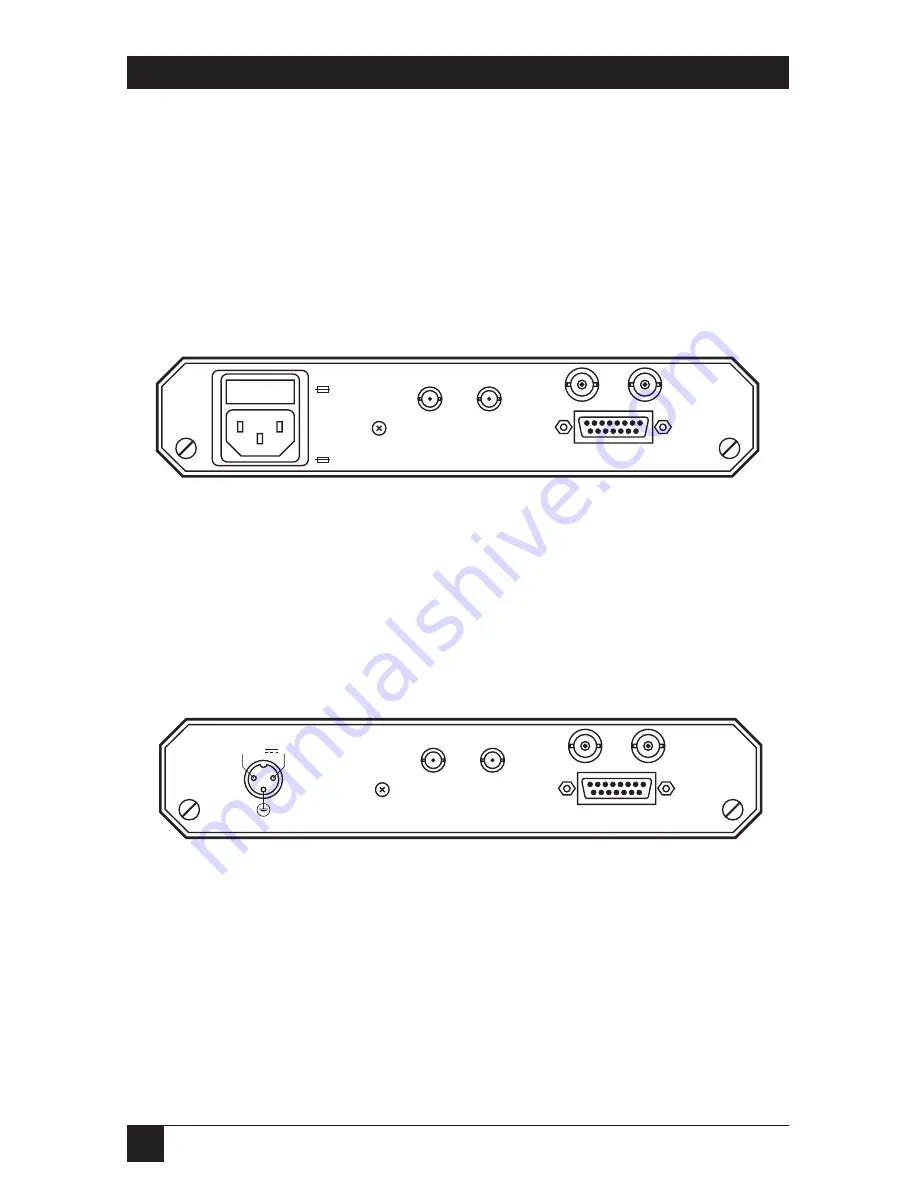
20
T1/E1 FIBEROPTIC LINE DRIVER
WARNING
The unit has no power switch. Its operation starts when power is applied
to the POWER connector. When applying power, first connect the plug
of the power cable to the Line Driver POWER connector and then to the
mains.
Figure 3-5. Line Driver Rear Panel.
Figure 3-6. Pinout of -48 VDC Power Jack.
OUT
IN
CHASS
GND
48V
+
-
RX
TX
~230V
0.1A T 250V
OUT
IN
RX
TX
100-115VAC
0.2A T 250V
Line Fuse