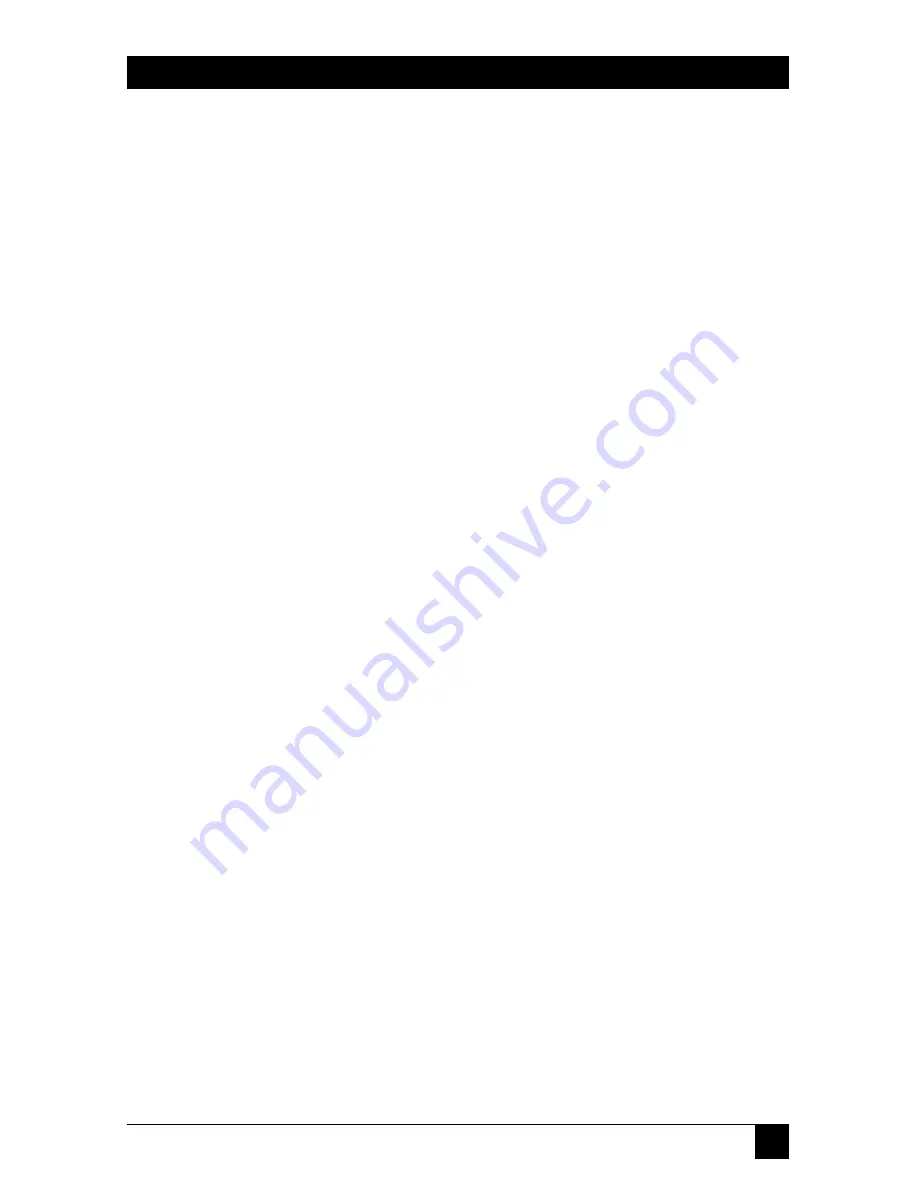
27
CHAPTER 4: Card Installation
4.2 The RackNest 2/14’s Power Supply
The 115-VAC RackNest 2/14 (our product code RM110A) uses the PS1000A power
supply, which accepts 115-VAC input power. The 230-VAC RackNest 2/14 (our
product code RM110AE) uses power supply PS1000AE, which accepts 230-VAC
input power. Each of these power supplies consists of a power-line transformer,
a fuse, and an operating switch. The 115-VAC Nest can also be ordered with dual
power supplies (our product code RM110A-2PS); either of these power supplies
can be hot-swapped if it fails.
All power-regulating circuitry for the RackNest 2/14 is located on the card
modems/drivers themselves. Each card has two fuses which protect the entire
system against power failure due to a short circuit in one card. Primary power
needed is 115 or 230 VAC ±10%, 47 to 63 Hz, at 24 VA maximum.
AC power should be supplied to the RackNest 2/14 through a standard power
cable run between the AC mains socket on the rear of the Nest’s power-supply
module—an IEC 320 male power inlet which contains an integral fuse—and a
standard, grounded, easily accessible AC outlet. (If your Nest is an RM110A, you
can use the power cord supplied with it; if your Nest is an RM110AE, use a power
cord appropriate for your site’s mains outlets.)
The Nest begins operating and supplying power to the installed Cards as soon as
it is plugged into a mains outlet, and will continue operating until it is unplugged.
WARNING!
The RackNest 2/14 unit should always be grounded through the
protective earth lead of the power cable. To connect AC power to this
unit, the mains plug should only be inserted into a socket outlet
provided with protective earth contact. The protective action must not
be negated by use of an extension cord without a grounding conductor.
Whenever it is likely that the unit’s fuse (located in a bayonet-type
fuse holder on the unit’s rear panel) has been blown or damaged, make
the unit inoperative and secure it against unintended operation until the
fuse can be replaced. Make sure that only fuses of the required rating,
as marked on the rear panel, are used for replacement. Do not use
repaired fuses or short-circuit the fuse holder. Always disconnect the
mains cable before removing or replacing the fuse.
Interrupting the grounding conductor, inside or outside the unit, or
disconnecting the protective earth contact, can make this unit
dangerous!
Summary of Contents for ME760A-R2
Page 26: ...25 CHAPTER 3 Standalone Installation Figure 3 2 The standalone LDM MR19 2 s board layout...
Page 35: ...34 LDM MR19 2 Figure 4 3 The LDM MR19 2 card s board layout...
Page 38: ...37 CHAPTER 5 Operation Figure 5 2 The LDM MR19 2 card s front panel 1 2 3 4 5 7 A 6 B C D...
Page 46: ...NOTES...
Page 47: ...NOTES...