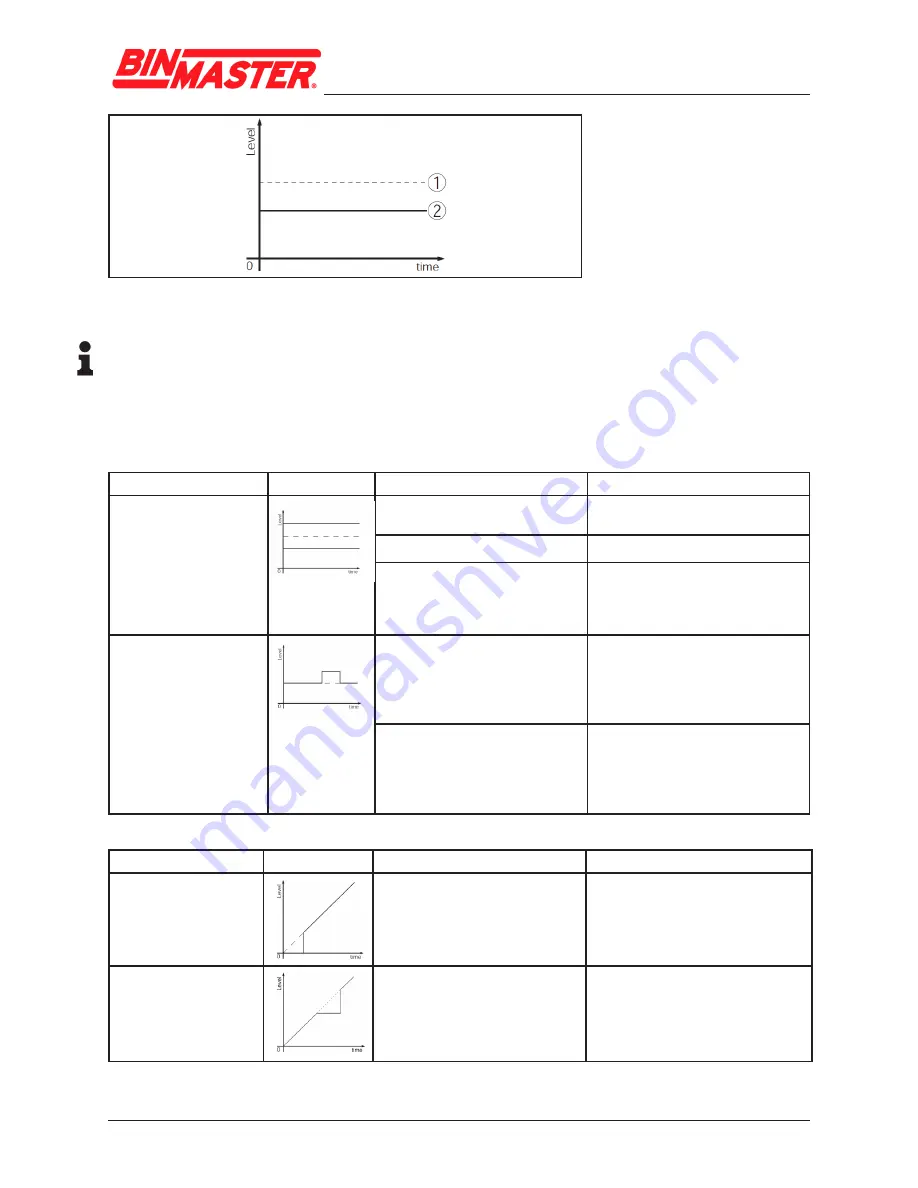
GWR-2000 Four-wire 4-20 mA/HART
925-0335 Rev B
9 Diagnosis, asset management and service
52
1 Real level
2 Level displayed by the sensor
Note:
●
Whenever the sensor displays a constant value, the reason could also be that the fault set-
ting of the current output is set to "Hold value"
●
If the level indication is too low, the reason could be a line resistance that is too high
Measurement error with constant level
Fault description
Error pattern Cause
Rectification
1. Measured value
shows a too low or
too high level
- Min./max. adjustment not
correct
- Adapt min./max. adjustment
- Incorrect linearization curve
- Adapt linearization curve
- Running time error (small
measurement error close to
100 %/serious error close
to 0 %)
- Repeat setup
2. Measured value
jumps towards 100 %
- Due to the process, the am-
plitude of the product echo
decreases
- A false signal suppression
was not carried out
- Carry out a false signal sup-
pression
- Amplitude or position of a
false signal has changed
(e.g. buildup); false sig-
nal suppression no longer
matches
- Determine the reason for the
changed false signals, carry
out false signal suppression,
e.g. with buildup
Measurement error during filling
Fault description
Error pattern Cause
Rectification
3. Measured value
remains in the area
of the bottom during
filling
- Echo from the probe end
larger than the product
echo, for example, with
products with εr < 2.5 oil-
based, solvents, etc.
- Check parameter "Medium"
and "Vessel height", adapt if
necessary
4. Measured value
remains momentarily
unchanged during
filling and then jumps
to the correct level
- Turbulence on the product
surface, quick filling
- Check parameters, change if
necessary, e.g. in dosing ves-
sel, reactor