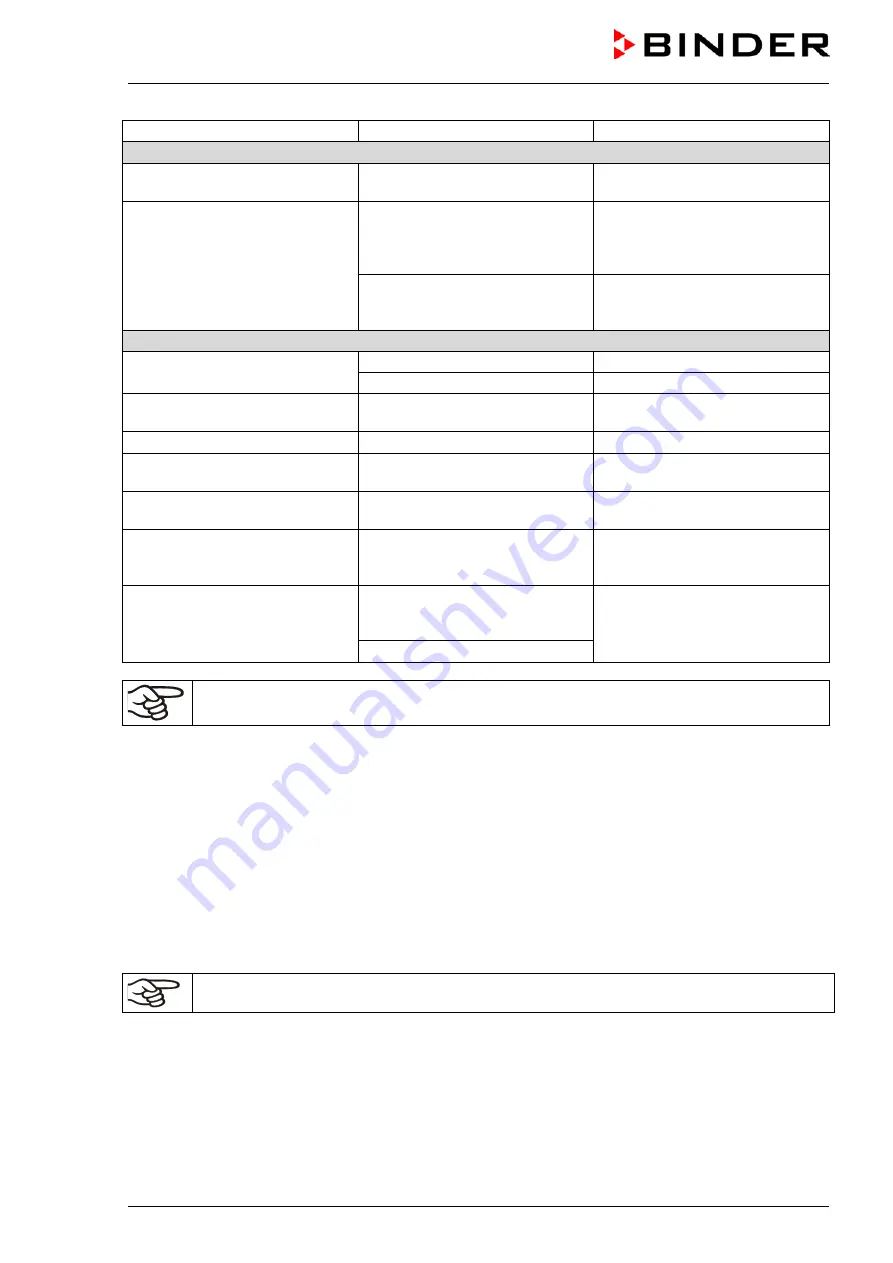
KBF-S (E6) 08/2018
page 70/88
Fault description
Possible cause
Required measures
Humidity
(continued)
Icing at the evaporator plates.
Set-point was too long below
ambient temperature.
Defrost the chamber (chap. 19).
Condensation at the walls of the
inner chamber.
Combination of tempera-
ture/humidity values not in the
optimum range (see temperature
humidity diagram, chap. 18)
Select combination of tempera-
ture/humidity values in the opti-
mum range (chap. 18).
Set-point was too long below
ambient temperature, icing in the
preheating chamber.
Defrost the chamber (chap. 19)
Controller
No chamber function
(dark display).
Display mode “Standby” active.
Press on touchscreen.
Main power switch turned off.
Turn on the main power switch.
Menu functions not available.
Menu functions not available with
current authorization level.
Log in with the required higher
authorization.
No access to controller
Password incorrect.
Contact BINDER service.
Controller does not equilibrate to
entered setpoints
Humidity control turned off.
Turn on humidity control (chap.
8).
Humidity alarm when operating
without water supply.
Humidity control turned on.
Turn off humidity control (chap.
8).
Acknowledging the alarm does
not cancel the alarm state.
Cause of alarm persists.
Remove cause of alarm. If the
alarm state continues, contact
BINDER service.
Alarm message:
- - - -
or <-<-<
or
>->->
Sensor rupture between sensor
and controller or Pt 100 sensor
defective.
Contact BINDER service.
Short-circuit.
Only qualified service personnel authorized by BINDER must perform repair.
Repaired chambers must comply with the BINDER quality standards.
24. Technical description
24.1 Factory calibration and adjustment
The chambers were calibrated and adjusted in the factory. Calibration and adjustment were performed
using standardized test instructions, according to the QM DIN EN ISO 9001 system applied by BINDER
(certified since December 1996 by TÜV CERT). All test equipment used is subject to the administration of
measurement and test equipment that is also a constituent part of the BINDER QM DIN EN ISO 9001
systems. They are controlled and calibrated to a DKD-Standard at regular intervals.
Repeated calibrations are recommended in periods of 12 months.
24.2 Over current protection
The chambers are equipped with an internal fuse not accessible from outside. If this fuse is blown, please
contact an electronic engineer or BINDER service.
Summary of Contents for KBF-S 240
Page 75: ...KBF S E6 08 2018 page 75 88 24 7 Dimensions Dimensions size 240...
Page 76: ...KBF S E6 08 2018 page 76 88 Dimensions size 720...
Page 78: ...KBF S E6 08 2018 page 78 88...
Page 79: ...KBF S E6 08 2018 page 79 88...
Page 81: ...KBF S E6 08 2018 page 81 88...
Page 82: ...KBF S E6 08 2018 page 82 88 26 Product registration...
Page 89: ......