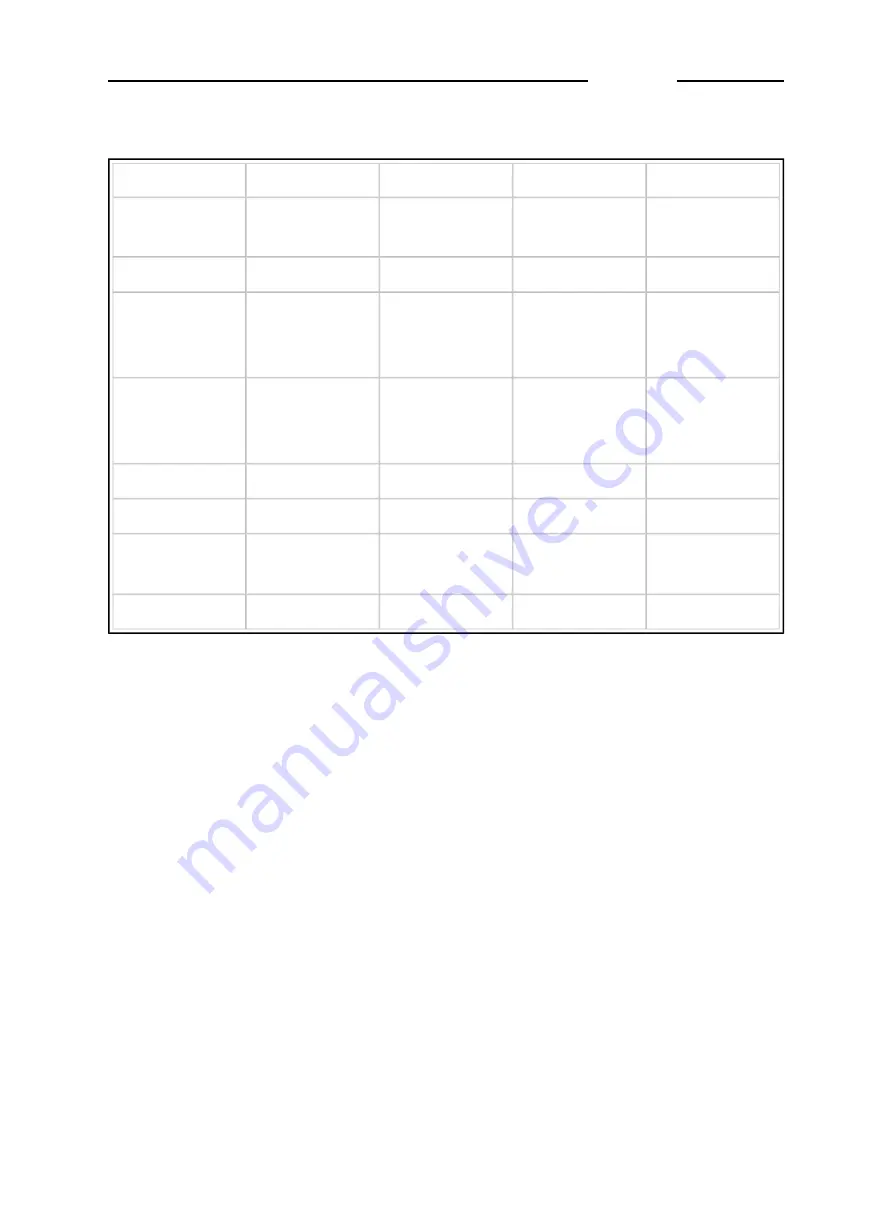
17.2 Management of errors by peripheral devices
Error -04-
Error -01-
Error -02-
Error -05-
??
??
NO
NO
Remote
commands
NO
Input
NO
NO
NO
NO
YES
YES
NO
Extended
string
transmission
NO
NO
NO
NO
Other
transmission
strings
BCD calc.
FFFFF
FFFFF
NO
NO
BCD aux.
FFFFF
FFFFF
NO
NO
NOT
ACTIVE
NO
NO
Output
active
NOT
ACTIVE
Analog.
MAX
0
NO
NO
where:
"NO" denotes "not managed";
"YES" denotes "managed";
"??" is the reply on the serial line;
"FFFFF" is the status of the outputs in hexadecimal code.
D400
3-57
Summary of Contents for D400
Page 2: ......
Page 4: ...D400 3 4 ...
Page 6: ...D400 3 6 ...
Page 18: ...Key 1 Jumper P1 2 Connectors for the MPP board Figure 13 11 CPU board log0152 gif D400 3 18 ...
Page 22: ...D400 3 22 ...
Page 47: ...Key 1 Jumper P1 2 Connectors for upgrade board Figure 15 2 CPU board log0152 gif D400 3 47 ...
Page 58: ......