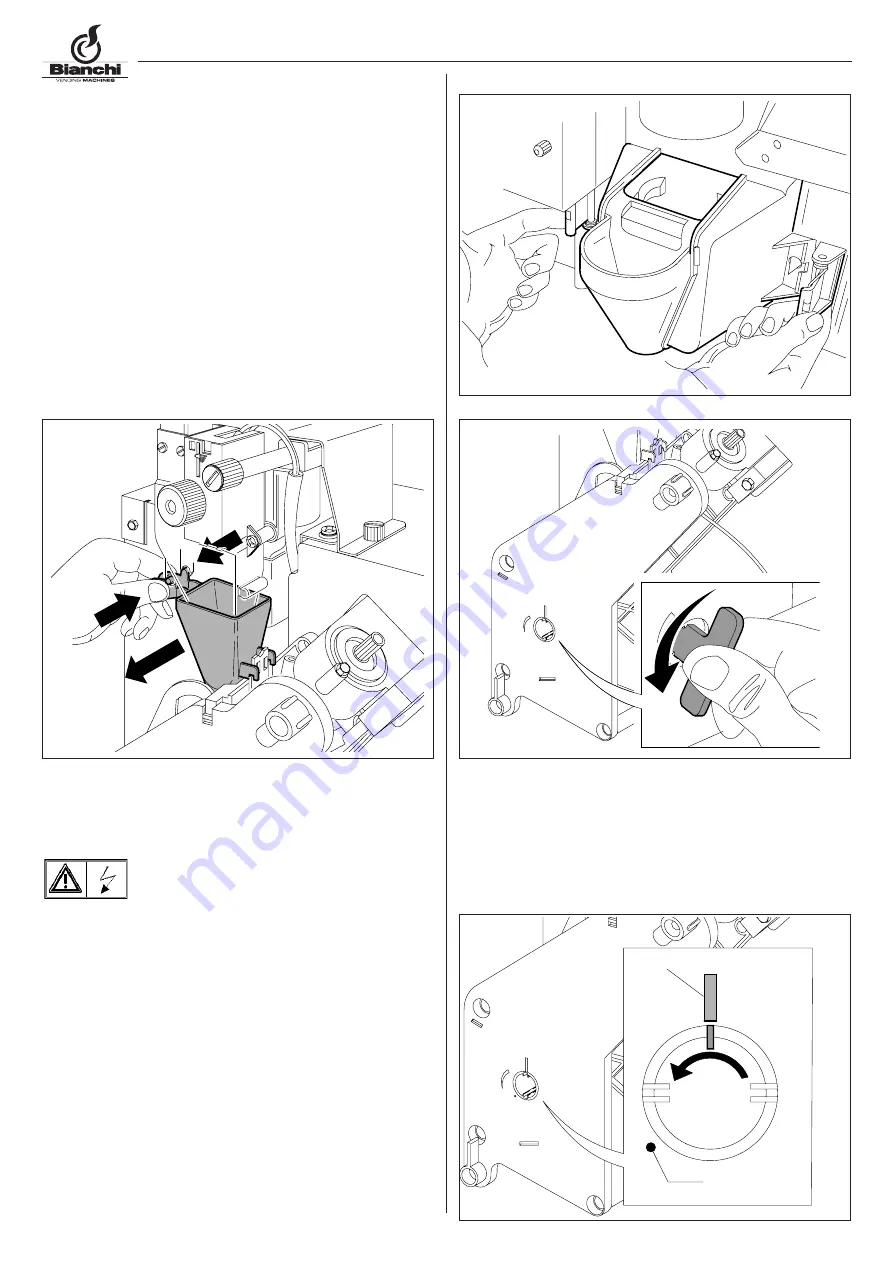
58
Fig.6.4
Fig.6.5
Fig.6.6
Fig. 6.7
– silicone water dispensing tubes.
– dispensing chamber (Fig. 6.4)
– coffee funnel and chute (Fig. 6.5)
Before effecting the re-assembly operations clean all the elements
carefully.
– remove all coffee powder residue; the unit can be removed
from its housing to make the task easier (Fig. 6.6)
6.2 Ordinary and Extraordinary Maintenance
The operations described in this section are purely indicative as
they are tied to variable factors such as the water hardness, hu-
midity, products used and workload, etc.
For all operations that require the disassembly of
the distributors’ components, make sure that the
latter is switched off.
Entrust the operations mentioned here below to qualifi ed per-
sonnel.
If the operations require that the distributor be switched on, entrust
them to specially trained personnel.
For more complicated interventions, such as removing the lime
build-up in the boilers a good knowledge of the equipment is
necessary.
Monthly effect the debacterisation of all the parts in contact with
food substances using chlorine based solutions following the
operations already described under chapter 4.5.3.
6.1.4 Product loading
When necessary provide for the loading of the products and/or
consumption materials of the automatic vending machine. For
these operations please refer to the operations described under
chapter 4.6.
COFFEE MACHINE TIMING CHECK PROCEDURE
Ensure that during the idle state, the rotating index is aligned with
the stage index (see fi g. 6.7)
Ensure that during the delivery stage that the rotating index is
not more than 1.5 mm in advance of the delivery reference point
(the rotating index must be at a delivery position of between 0
and 1.5 mm from the delivery point).
STAGE INDEX
DELIVERY
INDEX