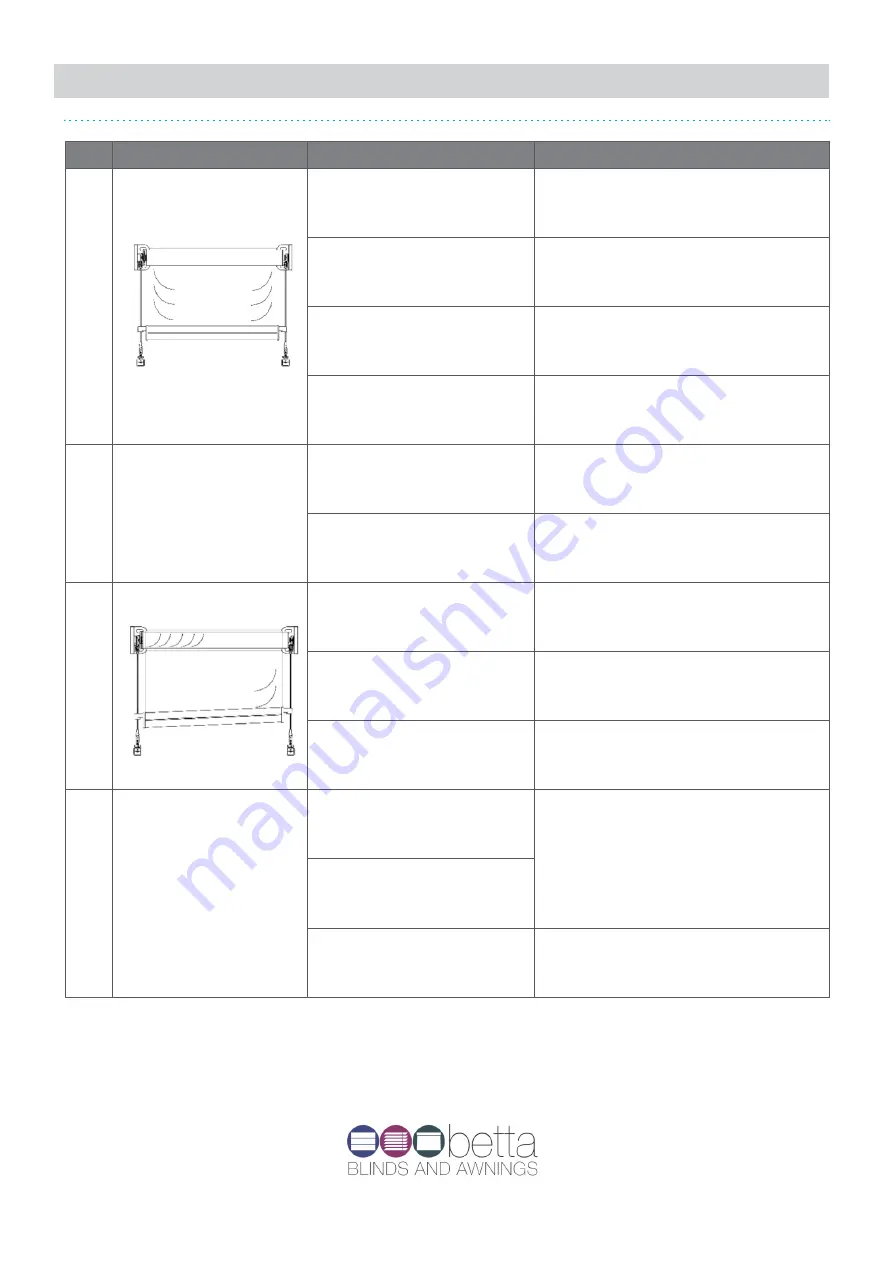
SECTION C
| TROUBLESHOOTING
NO.
PROBLEM
CAUSE
SOLUTION
1
Ripples along sides of fabric
Blind rolled up for an extended period of time.
This occurrence is inherent to roller systems and is more
prevalent in some fabrics. Leave blind down for 1
–
4 hours;
most ripples should disappear.
Not enough weight in weight bar.
Refer to Product Specs.
Add ballast.
Installation is not square.
Check blind roll is installed level.
Fabric permanently damaged due to
inadequate handling during assembly,
transportation, installation or use.
Replace fabric and ensure it is handled with care.
2
Blind does not fully open / jams
Position of wire guides at base is incorrect.
Check if wire guide fixing at floor/base are positioned in line
with the Top Terminal. If fixing is too far inwards of the
terminal then reposition. Refer to Part C, Step 1 of this
document for wire guide positioning details.
Incorrect motor stop limits used.
Refer to motor instructions to reset stop limits.
3
Ripples along sides of fabric
Blind roll is not level, thus weight bar ap- pears
uneven.
Ensure blind is installed level.
Blind has been operated in excessive wind
conditions.
Check blind roll when the blind is fully raised. If ripples are
evident on roll, open blind fully (without the presence of wind)
to allow the blind to track down evenly. Raise and lower blind a
number of times to check operation.
Fabric is not installed straight.
Ensure fabric is assembled straight onto tube and weight bar.
4
Locks go out of sync
Locks are not level
Lower blind until fabric is slack then lift one side so that the
lock disengages
Uneven Weight Bar (see above)
Obstruction preventing weight bar lowering
through lock
Remove obstruction to allow weight bar to reach its low- est
point.
Page. 18