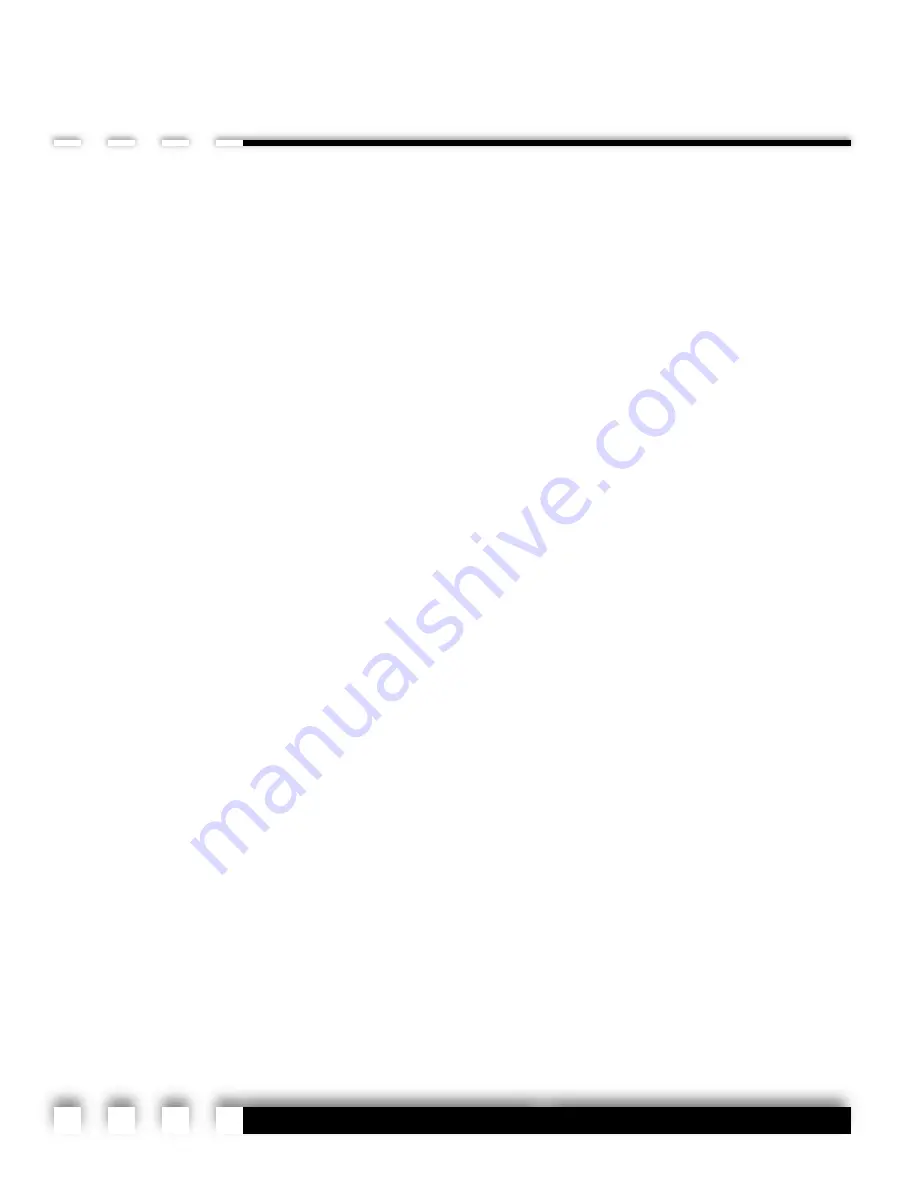
D10
the horizontal distance droplets will travel.
•
Relative humidity - In general, the lower the humidity, the greater the drift potential.
•
Air temperature - In general, higher temperatures mean increased drift potential.
•
Droplet size - With most chemicals, controlling spray droplet size is a key factor in
controlling drift. The smaller the droplet, the slower it will fall, the faster it will evaporate
and the further it will drift horizontally, particularly if winds are also a factor. Droplet
size is primarily determined by nozzle orifice size, spray angle and spray pressure.
Therefore, an increase in nozzle orifice size and/or a decrease in pressure is one way to
increase droplet size and decrease the potential for drift.
•
Boom height - Boom height is an important factor in controlling drift. A boom that is set
too high obviously favors drift, since droplets have farther to fall, thus having more time
and opportunity to drift off course. Doubling the boom height, in effect, doubles the
length of time required for droplets to reach the target canopy. That, in turn, doubles the
horizontal distance droplets can travel during their fall.
Managing Drift
To manage drift while spraying chemicals with the Pro-Mount 360:
•
Spray when wind velocity and direction doesn't favor drift. Do not spray when winds are
gusty or under any condition which will allow drift to move to an off-target area. That
includes spraying when wind is blowing toward a crop that doesn't have a resistant gene,
such as Roundup Ready crops.
•
Use a combination of nozzles and spray pressures that minimizes fine droplets. Keep spray
pressure within the range suggested by the nozzle manufacturer and use a larger nozzle –
one that delivers 10 to 20 gpm – if necessary.
•
Keep boom height at the lowest possible effective height while spraying.
Summary of Contents for PRO-MOUNT 360
Page 9: ...A8 SPECIFICATIONS ...
Page 11: ...A10 A H E F Safety Sign Locations C D G B J SMV Emblem P N 69290 ...
Page 19: ...B6 ...
Page 28: ...C9 Raven 440 Spray Wiring Diagram ...
Page 29: ...C10 Raven 450 Spray Wiring Diagram ...
Page 31: ...C12 ...
Page 49: ...E6 ...
Page 53: ...G2 TANK MOUNTING ASSEMBLY ref parts list on page G1 ...
Page 55: ...G4 400 GALLON TANK MOUNTING ASSEMBLY ref parts list on page G3 ...
Page 57: ...G6 BOOM STOW ASSEMBLY ref parts list on page G5 ...
Page 59: ...G8 FRAME ASSEMBLY LIFT PINS ref parts list on page G7 ...
Page 60: ...G9 FRAME ASSEMBLY PARKING STANDS LIFT TOWER ref parts list on page G7 ...
Page 61: ...G10 FRAME ASSEMBLY CENTER SECTION ref parts list on page G7 ...
Page 65: ...G14 BOOM ASSEMBLY CENTER SECTION ref parts list on page G12 ...
Page 66: ...G15 BOOM ASSEMBLY LEFT HINGE ref parts list on page G12 ...
Page 67: ...G16 BOOM ASSEMBLY RIGHT HINGE ref parts list on page G12 ...
Page 69: ...G18 BOOM WING ASSEMBLY ref parts list on page G17 ...
Page 70: ...G19 BOOM WING ASSEMBLY ref parts list on page G17 ...
Page 71: ...G20 BOOM WING HINGE END DETAILS ref parts list on page G17 ...
Page 72: ...G21 BOOM WING MID SECTION DETAILS ref parts list on page G17 ...
Page 73: ...G22 BOOM WING TIP DETAILS ref parts list on page G17 ...
Page 75: ...G24 BOOM HYDRAULIC SCHEMATIC ...
Page 79: ...G28 STEP PLUMBING DETAILS ref parts list on page G27 ...
Page 81: ...G30 STEP ASSEMBLY ref parts list on page G29 ...
Page 83: ...G32 Boom Valve Plumbing ASSEMBLY ref parts list on page G31 ...
Page 85: ...G34 3 SECTION BOOM PLUMBING DIAGRAM ref parts list on page G33 ...
Page 87: ...G36 5 SECTION BOOM PLUMBING DIAGRAM ref parts list on page G35 ...
Page 91: ...G40 RINSE TANK ASSEMBLY ref parts list on page G39 ...