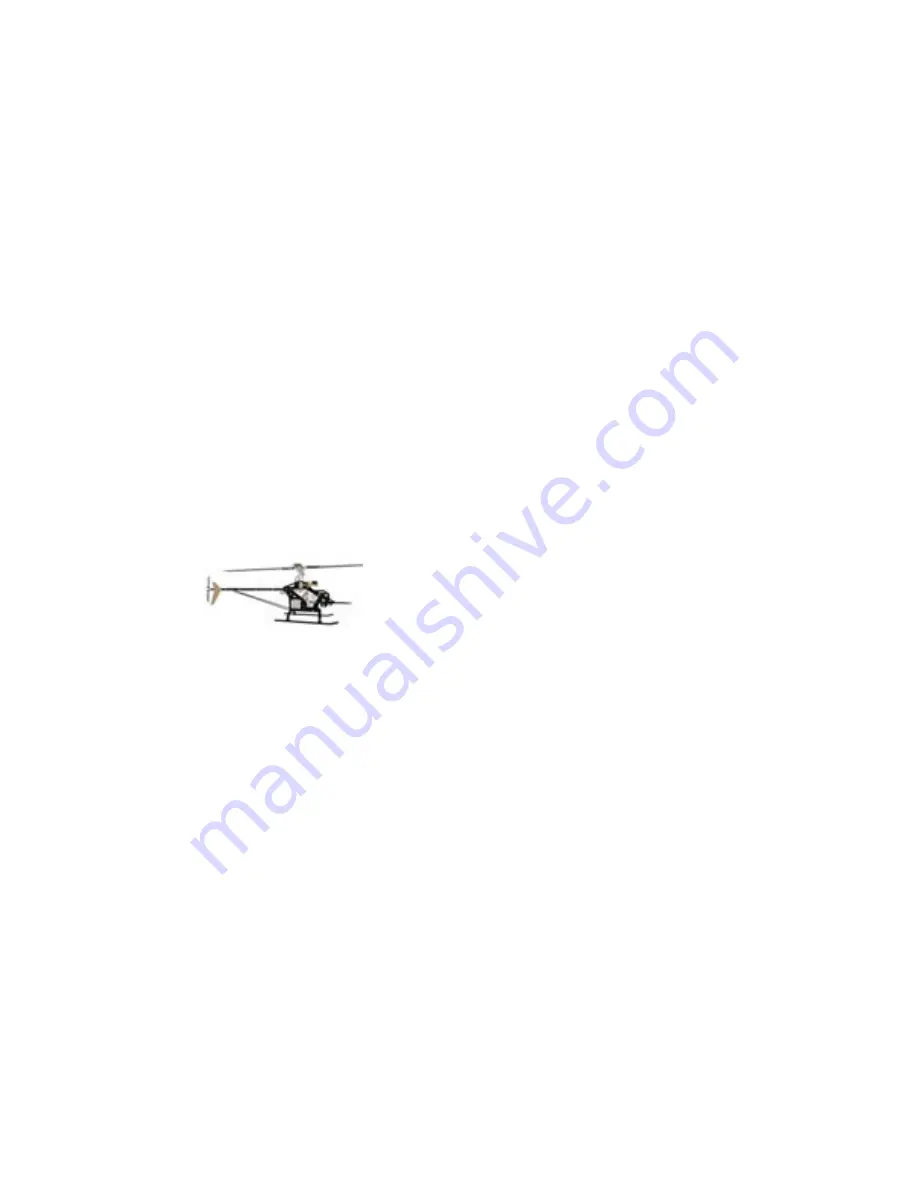
The first of its kind, interchangeable modular engineered helicopter to
accommodate the beginner to a FAI expert…
An idea in 1994 to manufacture an interchangeable, modular helicopter, led to
the research and development in 1995. Focusing on quality, engineering
details, and price, a prototype was produced. After extensive test flights and
fine-tuning, the INTREPID HELICOPTER is now what you see today. The first
of its kind, strength combined with simplicity for easy maintenance and flying.
Although beginners can successfully build and fly their INTREPID, the process
can be made significantly easier with the help of an experienced modeler and
instructor pilot. We recommend that all beginners join the Academy of Model
Aeronautics (AMA). The AMA is a non-profit organization that provides services
for modelers. The AMA can help you locate a model aircraft club in your area
with an instructor pilot (you can also check with your local hobby shop).
Membership benefits include a monthly magazine and liability insurance. Many
flying clubs require an AMA modeler’s license to operate a model on their flying
field. For more information on the AMA contact:
Academy of Model Aeronautics
5151 East Memorial Drive
Muncie, IN 47302
Phone: (317) 287-1256
Summary of Contents for Intrepid Magnum Tazer
Page 1: ...This manual is for the Intrepid Magnum Tazer and Intrepid Magnum Tazer 800...
Page 7: ......
Page 88: ......