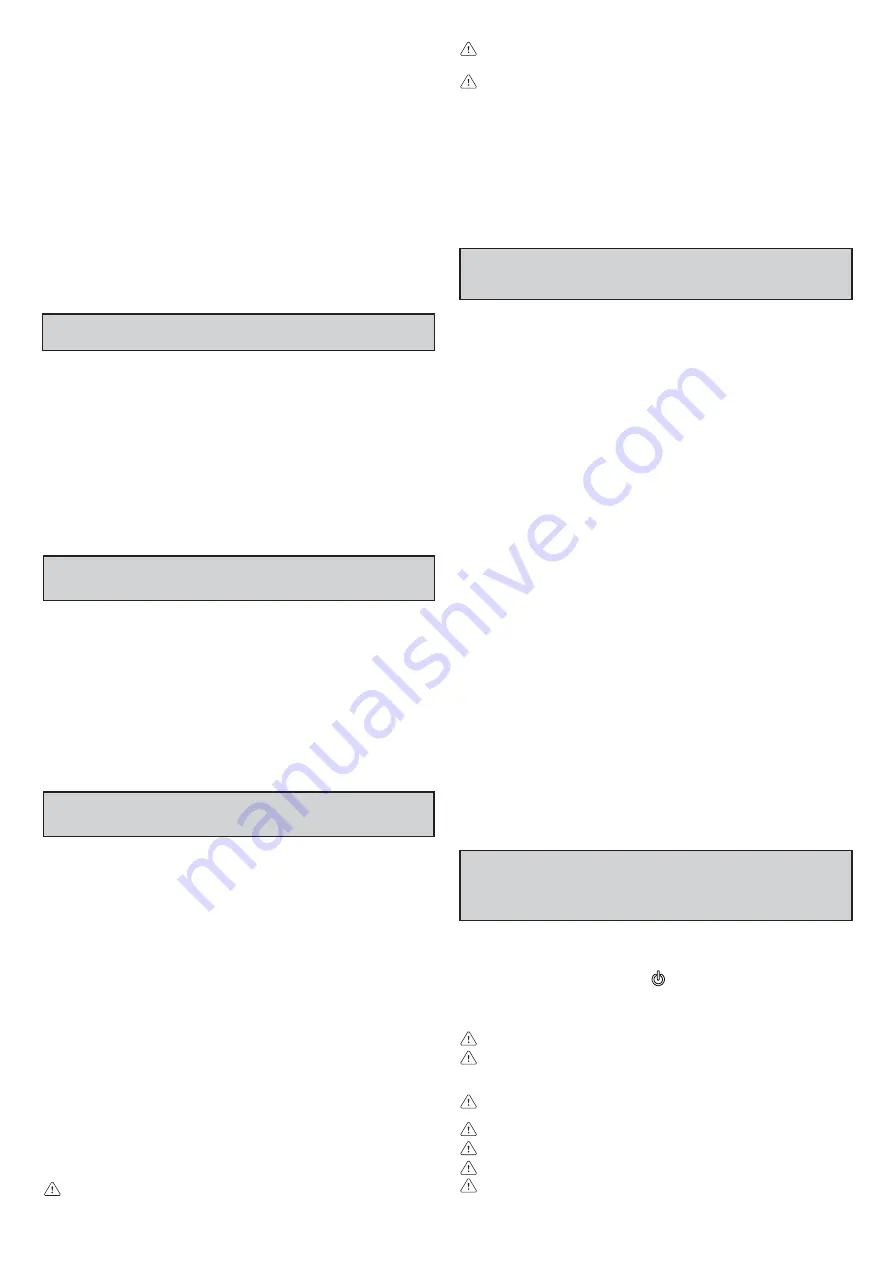
6
7
. FUMES
EXHAUSTION
AND BURNING AIR SUCTION (C.A.I. - R.A.I.)
Boiler is equipped with a system controlling proper exhaustion of
combustion products - fume thermostat (
12a-12b
,
fi
g. 82a-82b
page 134); in case of abnormality, this system immediately stops
appliance operation. Press the button to restore functionning
condition. If abnormality persists, do not perform any action, but
immediately call Technical Service; technicians will correct fume
exhaustion defect and test operation.
Refer to regulations in force for burnt product exhaustion.
It is compulsory using rigid pipes, junctions between elements
must be tight and all components must be resistant to tempe-
rature, condensates and mechanical stresses.
Device controlling proper fume exhaustion must never be de-
activated. Use original spare parts only when replacing it.
Exhaustion ducts which are not insulated can be dangerous.
Openings for burning air must comply with regulations in force.
If condensates are produced, insulate exhaustion duct.
Fig. 6b shows the top view of boiler with reference measures
for fume outlet distance between centres, from boiler support
plate.
Support plate and integrated pre-installation template are provided
for with the boiler (
fi
g. 2).
Mounting instructions:
•
fi
x the boiler support plate (
F
) with the template (
G
) to the wall
and use a plumb to check that it is perfectly horizontal
• trace out 4 holes (Ø 6 mm) for
fi
xing the boiler support plate (
F
)
and 2 holes (Ø 4 mm) for
fi
xing the pre-installation template (
G
)
• make sure all the measurements are correct, then drill holes in
the wall using a drill and point with the diameter given previously
•
fi
x the plate to the wall by the supplied anchor screws
• make hydraulic connections.
After installing the boiler, the screws
D
1
(
fi
g. 3a) can be removed. After
installing the boiler and connecting it to the water and gas supplies,
fi
t the lower cover (
A-B
,
fi
g. 3b) so that its hooks slip into the relative
slots in the lower part of the boiler. Fix the lower cover with the screw
C
(
fi
g. 3c) contained in the documentation envelope in the boiler.
Before connecting appliance to gas pipe network, check the fol-
lowing:
• regulations in force are met
• gas type used is the same as set for appliance operation
• pipes are clean.
Gas must be piped externally. If the pipe goes through a wall it must
go through the central opening in the lower part of the template. It
is recommended to install an appropriately sized
fi
lter on the gas
line in case gas from the mains contains some small solid particles.
After installation make sure that all the joints have been made airtight
conforming to standard installation practices.
4
. GAS
CONNECTION
Position and dimensions of hydraulic connections are speci
fi
ed in
fi
gure 2
:
A -
CH return
3/4”
B -
CH delivery
3/4”
C -
gas connection
3/4”
D -
DHW outlet
1/2” (C.A.I.-MIX C.S.I. only)
E -
DHW inlet
1/2” (C.A.I.-MIX C.S.I. only)
F -
Support plate
G -
Pre-installation template
If water hardness exceeds 28°Fr, it is recommended to use water
softeners, to prevent any limestone deposit in boiler due to exces-
sively hard water.
3
. HYDRAULIC
CONNECTIONS
To access the electrical connections, proceed as follows:
- unscrew the lower cover
fi
xing screw (
C
,
fi
g. 3c)
- pull the cover towards you and remove (
A-B
) (
fi
g. 4a)
- loosen the
fi
xing screws (
D
) and remove the shell (
fi
g. 3a)
- lift up the panel and turn it forwards
- open the terminal board covers making them slide in the direction
of the arrows (
fi
g. 4b:
E
high voltage connections 230 V,
F
low
voltage connections,
G
water tank sensor connections only MIX
R.S.I.-R.A.I.).
Connect the appliance to the mains power supply with a switch
featuring a distance of at least 3,5 mm (EN 60335-1, category III)
between each wire.
The appliance uses alternating current at 230 Volt/50 Hz, has a
power input of 88 W (C.A.I. - R.A.I.), 120 W (26kW MIX C.S.I.), 150
W (30kW MIX C.S.I. - MIX R.S.I.) and 160 W (35kW MIX C.S.I. - MIX
R.S.I.) and complies with EN 60335-1 standard. Connect the boiler
to a safe earth circuit according to current legislation.
Live and neutral (L-N) connections should also be respected.
The boiler can operate with phase-neutral or phase-phase power
supply. For
fl
oating power supply, without an earth-bonded
conductor, it is necessary to use an insulation transformer with
secondary anchored to ground.
The earth conductor must be a couple of cm longer than
the others.
5
. ELECTRIC
CONNECTION
The central heating system can be
fi
lled up once the water mains
have been connected up.
This must be done while the installation is cold by:
• giving two or three turns to the cap of the automatic air vent valve
(
A
,
fi
g. 5a and 5b) to open it;
• making sure the cold water inlet tap is open (MIX C.S.I. - C.A.I.
only)
• opening the
fi
lling tap (
C,
on the boiler for MIX C.S.I. - C.A.I.,
external for MIX R.S.I. - R.A.I.) until the pressure on the hydrometer
(
D
) is between 1 and 1,5 bar (blue zone) (
fi
g. 5a and 5b).
Close the
fi
lling tap after
fi
lling it up.
The boiler is equipped with an ef
fi
cient air separator so that there
is no need to do anything manually.
The burner only ignites when air venting has
fi
nished.
NOTE (MIX C.S.I. - C.A.I. only):
even if the boiler is
fi
tted with a se-
mi-automatic
fi
lling system, open tap
C
to
fi
ll the circuit the
fi
rst time.
NOTE (MIX R.S.I. - R.A.I. only):
manual
fi
lling tap is not supplied
with the boiler, foresee one external or verify if external water tank
has one.
Empty the system by:
• switching off the boiler
• connect the rubber hose, supplied standard, to the boiler drain
valve (
E
,
fi
g. 5a and 5b)
• loosening the valve by hand (
E
)
• emptying out the lowest parts of the system.
DHW system emptying (MIX C.S.I. - C.A.I. only)
The hot water system must be emptied every time there is risk of
freezing by:
• turning off the tap at the mains
• turning on all the hot and cold taps
• emptying out the lowest parts of the system.
ATTENTION
The safety valve outlet (
B
) must be connected to a suitable col-
lection system.
The manufacturer shall not be held liable if the safety valve should
eventually cause
fl
ooding.
6
.
FILLING AND EMPTYING THE SYSTEM
Gas and/or water pipes may not be used to earth electrical
equipment.
The installer is responsible for making sure that the ap-
pliance has an adequate earthing system; the manufacturer
shall not be held liable for eventual damages caused by
incorrect usage or failing to earth the boiler.
Use the
supplied power cable
to connect the boiler to the mains
power supply.
Connect the ambient thermostat and/or time clock as shown in the
electrical diagram on page 145.
When replacing the power cable, use a HAR H05V2V2-F cable,
3 x 0,75 mm
2
, Ø max. external 7 mm.