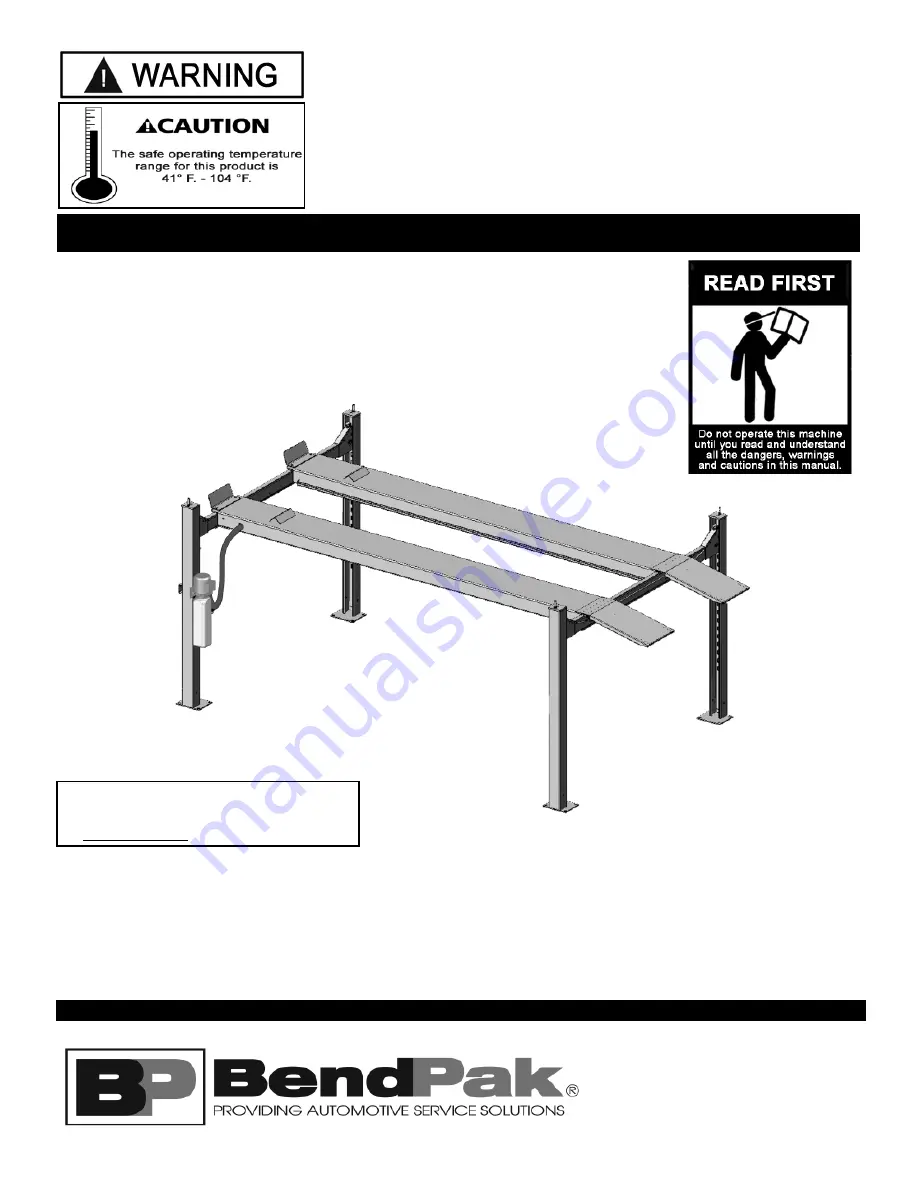
INSTALLATION AND OPERATION MANUAL
SHIPPING DAMAGE CLAIMS
When this equipment is shipped, title passes to the
purchaser upon receipt from the carrier. Consequently,
claims for the material damaged in shipment must be made
by the purchaser against the transportation company at the
time shipment is received.
BE SAFE
Your new lift was designed and built with safety in mind.
However, your overall safety can be increased by proper
training and thoughtful operation on the part of the operator.
DO NOT operate or repair this equipment without reading
this manual and the important safety instructions shown
inside.
1645 Lemonwood Dr.
Santa Paula, CA. 93060, USA
Toll Free 1-800-253-2363
Tel: 1-805-933-9970
Fax: 1-805-933-9160
www.bendpak.com
Keep this operation manual near the
machine at all times. Make sure that
ALL USERS read this manual.
14,000 POUND CAPACITY
COMMERCIAL GRADE
FOUR-POST LIFTS
MODELS:
HD-14SS
HD-14
HD-14X
HD-14 TL
PLEASE READ THE ENTIRE CONTENTS OF THIS MANUAL PRIOR TO INSTAL-
LATION AND OPERATION. BY PROCEEDING YOU AGREE THAT YOU FULLY
UNDERSTAND AND COMPREHEND THE FULL CONTENTS OF THIS MANUAL.
FORWARD THIS MANUAL TO ALL OPERATORS. FAILURE TO OPERATE THIS
EQUIPMENT AS DIRECTED MAY CAUSE INJURY OR DEATH.
REV D 08-13-10
p/n 5900037
Summary of Contents for HD-14
Page 8: ...8 Assembly View ...
Page 21: ...21 ...
Page 27: ...27 HD 9 12 12X 14 14X Series Rolling Jack Air Line Installation Kit Part 5174009 REV 06 04 09 ...
Page 28: ...28 Adapter Plate Required for HD 9 12 14 Adapter Plate Required for HD 9 12 14 ...
Page 31: ...31 ...
Page 32: ...32 ...
Page 38: ...38 ...