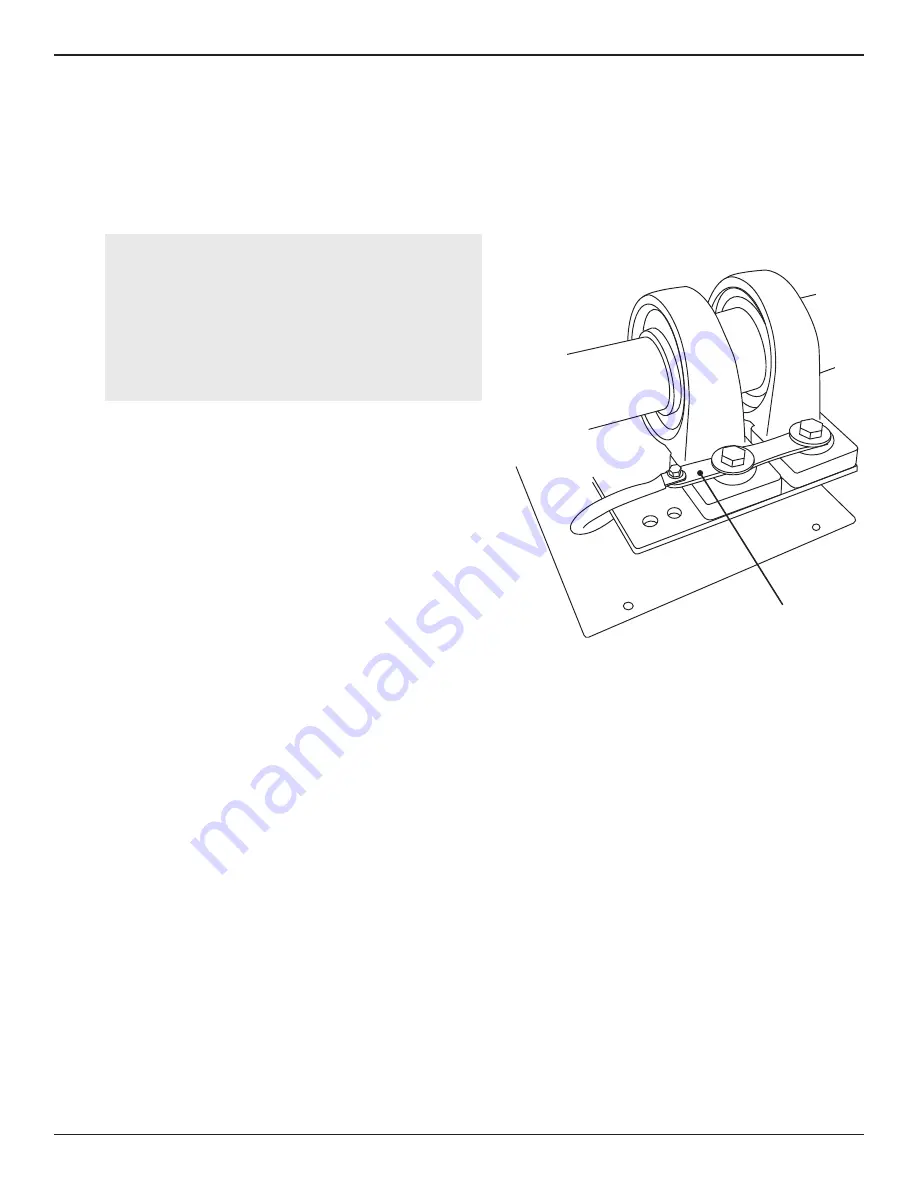
31
Bend-Tech Dragon A150
Troubleshooting Guide
Torch
04
Grounding The Torch
Early Dragon A150 machines achieve Torch ground via a carbon brush rod system. Bend-Tech
has found moving the ground cable location to the pillow block bearing mount results in a more
consistent ground for the Torch.
1. Using a ¾ in. wrench and a ¾ in. socket and
ratchet, remove the right side bolt on the rear
pillow block bearing.
2. Using a grinding wheel or sanding disc,
lightly remove the paint from the top
mounting surface around the pillow block
bearing mounting hole.
3. Bend-Tech can provide a mounting tab for
the Torch ground cable, or the Operator can
fabricate a ground cable mount using 3/16 in. steel.
4.
Place the mounting tab over the pillow block bearing mounting hole. Using the 3/4 in. wrench
and 3/4 in. socket and ratchet, reinstall the pillow block bearing mounting bolt that was
removed in step 1.
5. Using two ½ in. wrenches, remove the Torch ground cable mounting bolt from the carbon
brush rod mounting plate. Position the cable so the mounting bolt can be inserted through
the new ground tab and the Torch ground cable. Using the ½ in. wrenches, secure the
Torch ground cable to the grounding tab on the pillow block bearing.
Tools Required
•
3/4 in. wrench
•
3/4 in. socket and rachet
• Grinder/Sander
•
1/2 in. wrench (2)
Mounting Tab
Summary of Contents for DRAGON A150
Page 1: ...A150 Part 1 of 1 Maintenance Troubleshooting Revision 1 English 2020 Bend Tech LLC...
Page 12: ...xii Bend Tech Dragon A150 Troubleshooting Guide Contents...
Page 28: ...28 Bend Tech Dragon A150 Troubleshooting Guide Toolhead 03...
Page 34: ...34 Bend Tech Dragon A150 Troubleshooting Guide Torch 04...
Page 36: ...36 Bend Tech Dragon A150 Troubleshooting Guide Engraver 05...
Page 38: ...38 Bend Tech Dragon A150 Troubleshooting Guide Marker 06...
Page 44: ...44 Bend Tech Dragon A150 Troubleshooting Guide Gate 08...
Page 48: ...48 Bend Tech Dragon A150 Troubleshooting Guide Trolley 09...
Page 56: ...56 Bend Tech Dragon A150 Troubleshooting Guide X and Y Axis Maintenance 11...
Page 72: ...72 Bend Tech Dragon A150 Troubleshooting Guide Limit Switch Operation 15...
Page 77: ......