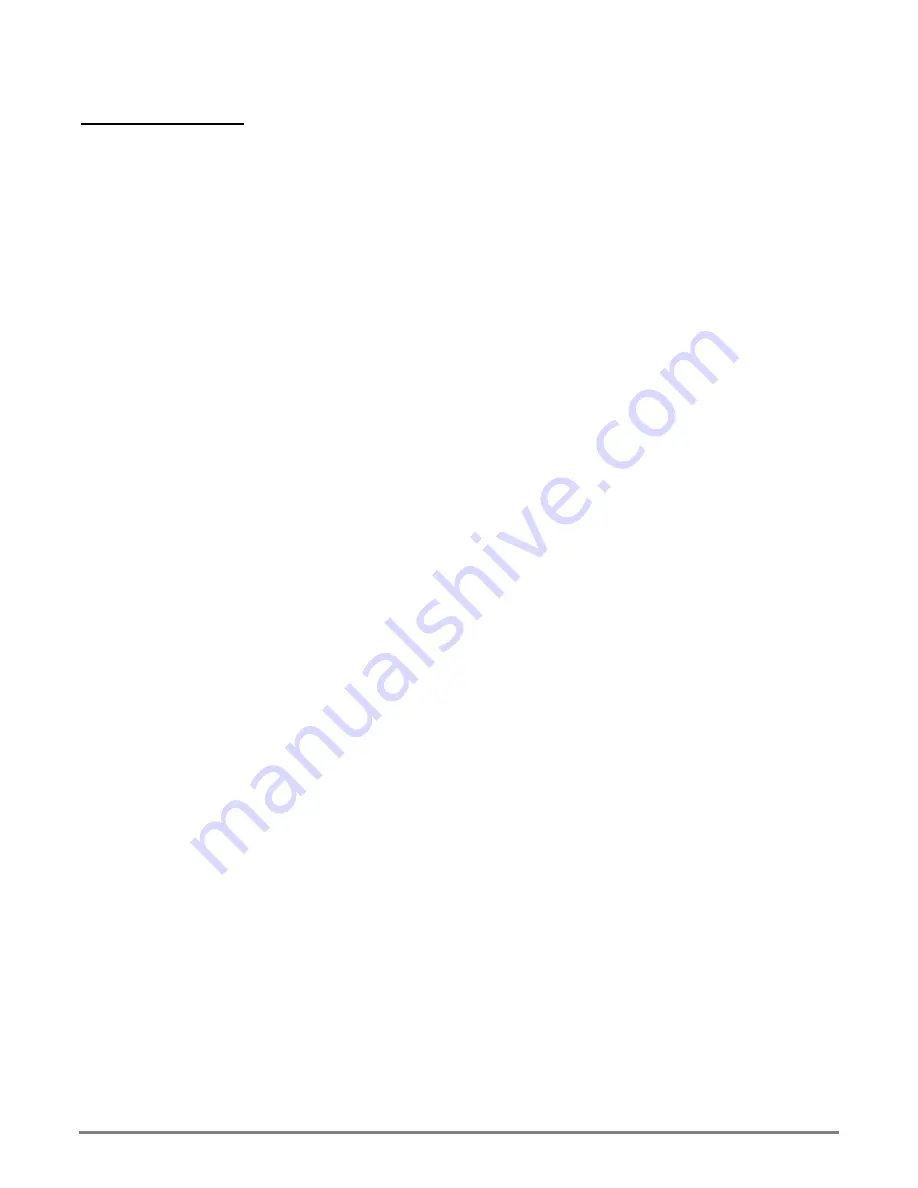
ETL File 3028821
35
V.B2006
Model BARO Rack Oven
4.
Power to heat circuit, low heat, slow heat
•
Check for 24VAC at wires 54 and 45 on hot surface igniter and ignition control
simultaneously. Ignition control should blink once and hot surface igniter
should glow red hot. If igniter glows intermittently replace igniter.
•
Ignition control proves hot surface igniter amps. After approximately 7 seconds
24VAC from ignition control should be present to wires 45 and 45A on pins 1
and 2 of main valve, and at 2 brown wires also plugged into pins 1 and 2 on
main valve. Valve should then open igniting burners.
•
Main valve coil (pins 1 and 2) with 2 brown wires unplugged should read 62
Ω
.
Redundant pilot valve (2 brown wires) should read 19
Ω
unplugged.
•
Once burners are lit 4 micro amps should be present from flame sensor to pin S2
on ignition control. If micro amps are weak check gas supply pressure, NG 5”-
14” and LP 10”-14” with never more than a ½” W/C pressure drop—this could
indicate low gas volume. Manifold pressure on
BARO-1G
3” NG and 8” LP.
Manifold pressure on
BARO-2G
2.5”-2.8” NG (see tag on valve) and 6” LP. If
gas supply is sufficient and micro amp reading is low replace flame sensor.
•
If burner does not stay lit long enough to develop a micro amp reading on flame
sensor check for continuity between wire 45 on valve and chassis ground.
•
Check oven calibration and probe
Ω
reading.
Temperature Erratic
1.
Temperature in display jumping
•
Make sure a program is correct (0 blower delay) and countdown timer is
running. Display temperature will jump around dramatically when Automatic
Energy Management System turns on; this is a normal energy saving feature. If
temperature stays at one temperature or drops before preheat temperature is
achieved or to turn AEMS off, (on software versions 3.07 and newer) contact
factory.
•
Temperature will drop when steam is run. More than 15 seconds of steam is not
recommended; at this point no more steam is generated and oven is drastically
cooled.
•
After temperature begins to climb in preheat the temperature should increase in
increments of 2-3 degrees every 4-7 seconds. If temperature is sticking on one
temperature in preheat and taking more than 7 seconds to change, check the
temperature probe to ensure that it is not grounded or contact factory for more
information.
Summary of Contents for BARO-G
Page 2: ......
Page 4: ......
Page 22: ...ETL3028821 20 REV B2006...
Page 35: ...ETL File 3028821 33 V B2006 Electrical Connections See page 16...
Page 42: ...ETL File 3028821 40 V B2006...
Page 43: ...ETL File 3028821 41 V B2006...
Page 44: ...ETL File 3028821 42 V B2006...