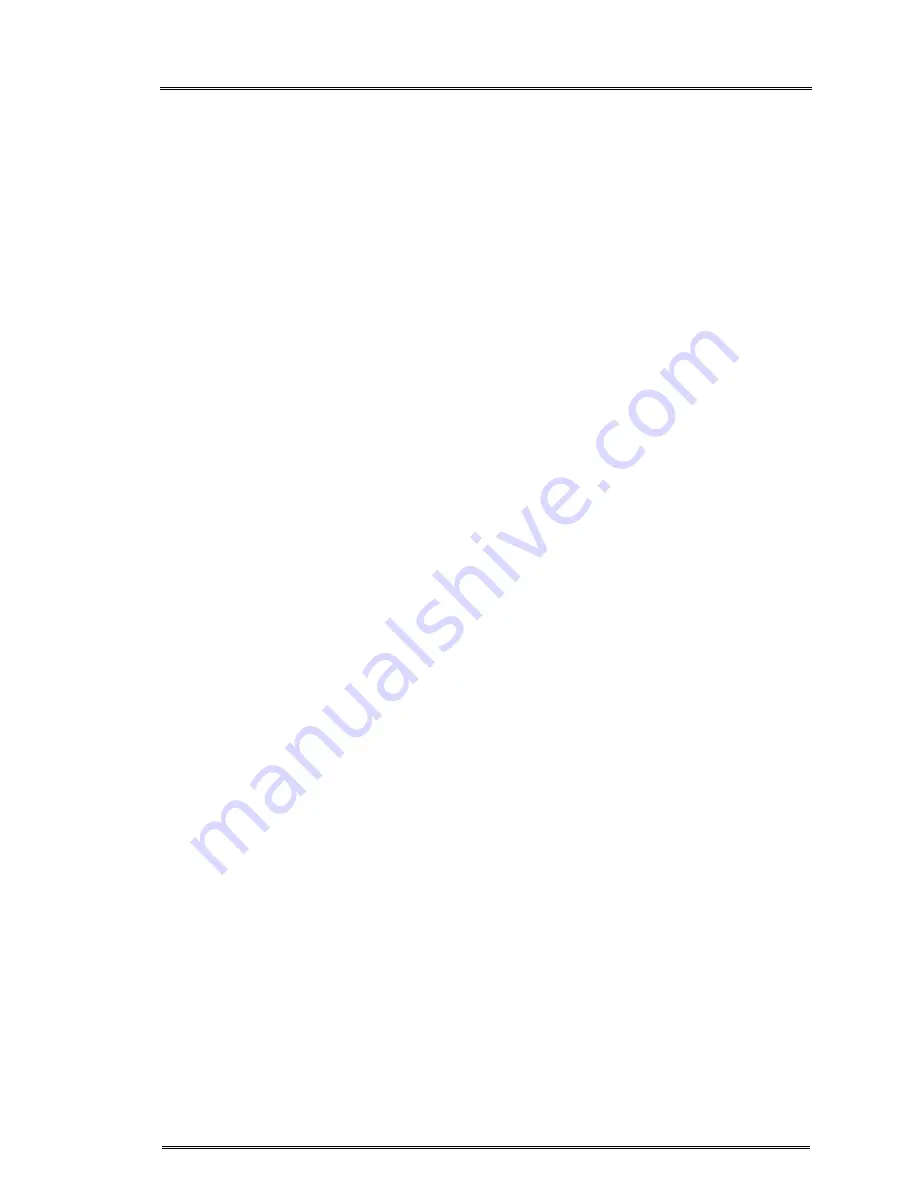
4. Theory of Operation
4-39
The daughter board contains: battery control circuitry, DC/DC power supply,
roller pump motor driver, valve motor driver, valve position sensors, pressure
transducer and amplifier, RS232 port, air detector electronics, sound transducer,
and door position sensor. The temperature probe assemblies, which are
mounted on the support housing, are connected to the daughter board by cables.
The daughter board mounts directly to the right hand side of the support housing.
OPERATION:
The battery control circuitry
charges the battery, maintains the fan running
while the system is off, and controls the power flow in the unit including power
on/off control.
The DC/DC power supply
contains a EMI filter, a DC/DC converter and
regulators. The supply outputs +5V, +80V, -100V and -105 V derived from a
20-30 volt input. The +5V and –100V have secondary regulators to ensure that
the output voltages remain within the specified tolerance limits. The supply is
current limited and contains a thermal fuse.
The pump motor driver
consists of a half bridge power driver that allows both
acceleration and braking of the pump motor. The driver has an over current
sense and independent shutdown control. The pump speed is controlled by a
pulse width modulated signal produced by the microcontroller, which is controlled
by the demanded flow rate that is set by the operator. The feedback is
accomplished by means of an encoder in the motor communicating with the
computer board.
The valve motor driver
contains two parts, the motor power driver and current
monitoring circuitry. The driver consists of four power MOSFETS in a bridge
configuration which is capable of driving the motor in both directions. The current
monitor circuitry sends a voltage to an analog-to-digital converter (ADC) input of
the microcontroller system that is proportional to the motor current, and also has
a limit comparator for shutdown in the event of an over current condition.
The valve position sensors
are Hall effect sensors that are placed at the proper
locations on the daughter board to detect a magnet that is mounted in the valve
wand magnet. These signals are sent to the computer module.
A pressure transducer
is strategically placed on the daughter board so as to
interface with the pressure chamber/air eliminator of the disposable set. The
pressure sensor is a Wheatstone bridge strain gauge, incorporating a diaphragm,
with diffused or implanted resistors in a bridge configuration. The pressure
sensor measures the pressure difference relative to atmosphere, or gauge
pressure. When pressure is applied to the diaphragm, the output shifts due to
piezoelectric effects created by mechanical strain in the four bridge resistors.
The sensor is powered by a constant current source, and an instrumentation
amplifier on the daughter board amplifies the signal produced. This signal is
applied to an ADC input of the microcontroller. The disposable set pressure
chamber must be installed flat to the pressure sensor diaphragm, or pressure
sensitivity will be affected.