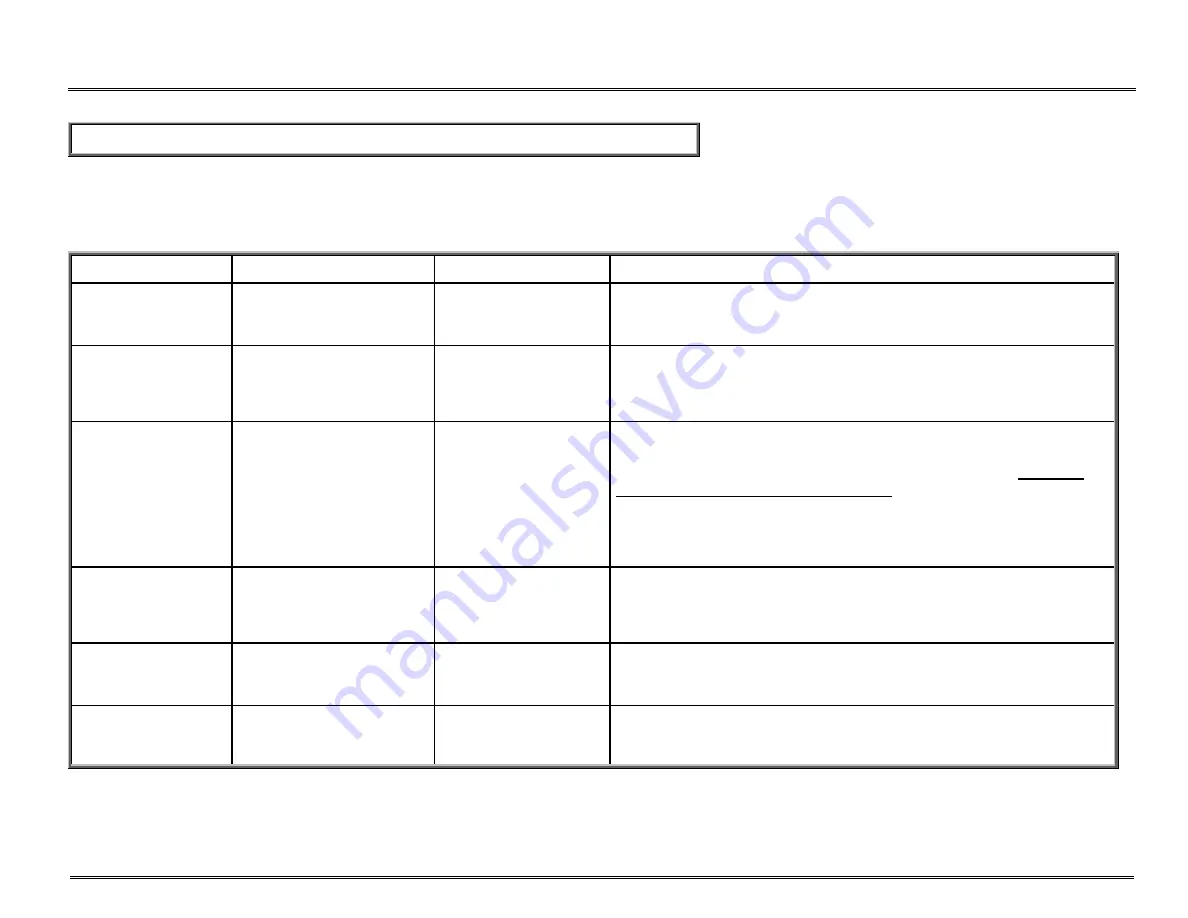
8. Alarms and Troubleshooting Guide
8-120
TROUBLESHOOTING OTHER OPERATIONAL DIFFICULTIES
There are times that problems occur that are outside the comprehensive surveillance system. These can be due to improper setup, faulty
accessory equipment, or internal failure of a component. This table describes several of these potential problems, the alarm that might be
generated (if any), and the corrective actions to take.
PROBLEM
POSSIBLE CAUSE
SYSTEM RESPONSE
OPERATOR ACTION
Battery No Heating
Power cord not plugged in
AC power
NA
Plug into AC receptacle; check power cord connection. Keep the system
plugged in to charge the battery.
Dim display
Display brightness in Setup
Routine has been turned
down to the lowest
brightness setting.
NA
Increase display brightness in System Setup, Chapter 6.
Flow rate is slowing
down or will not go at
the set rate
The system is keeping the
pressure in the line under
the Pressure Limit by
reducing the infusion rate.
Pressure reading
flashes at “Pressure
Status Line” and system
periodically beeps.
Check and remove kinks or obstructions in the tubing.
Use the appropriate infusion set recommended in the guide, Match the
Infusion Set to Flow Rate and Fluid Type in Chapter 3.
Increase flow by increasing the Pressure Limit. Change the Pressure
Limit in Calibration/Setup to a higher limit (maximum Pressure Limit is 300
mmHg).
Key pad does not
accept input
The keypad is being
continually depressed.
Key pad failure
Constant beep
Release the keypad and the constant beep will cease.
If the alarm persists, power down and service machine.
Keypad is too
sensitive or not
responsive
Keypad sensitivity in Setup
Routine has been set at
Fast or Slow.
NA
Reset keypad sensitivity in System Parameters Setup, Chapter 6.
No message, beep
tone
Power switch not completely
depressed or membrane
switch failed.
Depress power switch completely. If problem persists, replace the
membrane switch.