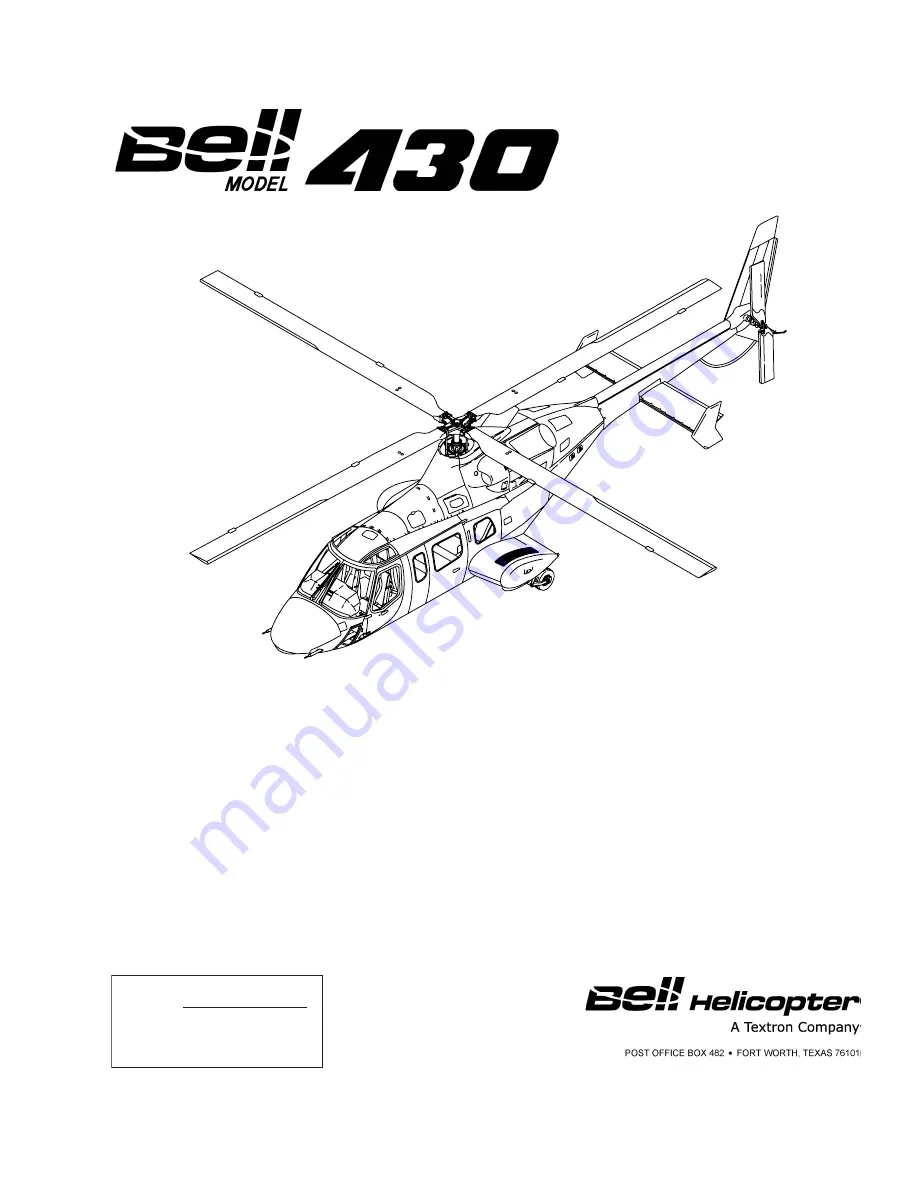
BHT-430-MM-2
NOTICE
The instructions set forth in this manual, as supplemented or modified by Alert Service Bulletins (ASB) or
other directions issued by Bell Helicopter Textron Inc. and Airworthiness Directives (AD) issued by the
applicable regulatory agencies, shall be strictly followed.
REISSUE — 30 JUNE 1999
REVISION 19 — 1 NOVEMBER 2012
COPYRIGHT NOTICE
COPYRIGHT
2012
BELL ® HELICOPTER TEXTRON INC.
AND BELL HELICOPTER TEXTRON
CANADA LTD.
ALL RIGHTS RESERVED
MAINTENANCE MANUAL
VOLUME 2
HANDLING AND SERVICING
Summary of Contents for 430
Page 6: ......
Page 12: ......
Page 16: ......
Page 36: ......
Page 68: ......
Page 74: ......
Page 82: ......
Page 88: ......
Page 114: ......
Page 116: ......
Page 124: ......
Page 130: ......
Page 132: ......
Page 134: ......
Page 136: ......
Page 138: ......
Page 140: ......
Page 142: ......
Page 144: ......
Page 146: ......
Page 154: ......
Page 168: ......
Page 172: ......
Page 176: ......