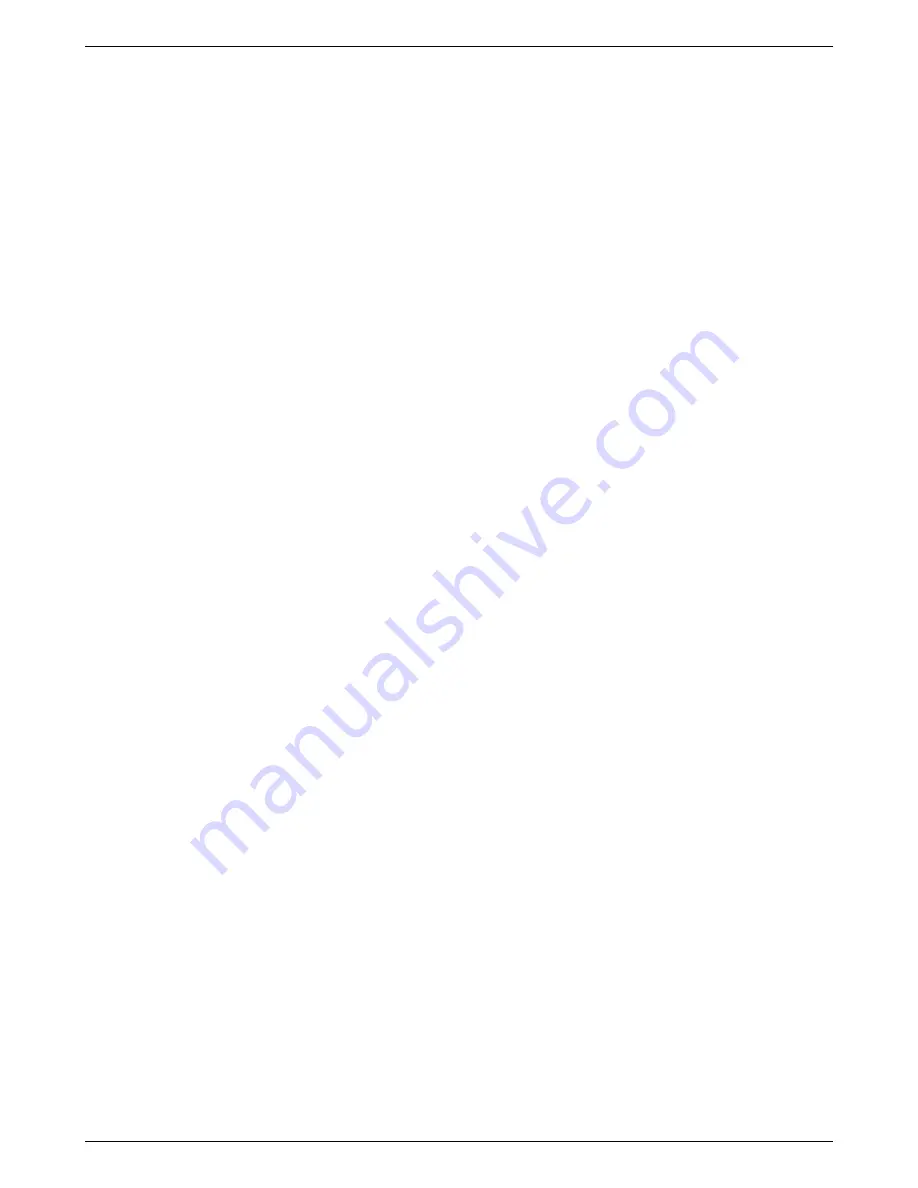
Technical description
DRYPOINT® RA 1080-8800
27
11.5 Refrigerating
compressor
The employed refrigerating compressors are constructed by leading manufacturers. The hermetically sealed
construction is absolutely gastight. The integrated safeguard protects the compressor against overheating and excess
current. The protection is automatically reset as soon as the nominal conditions are reached again.
11.6 Condenser
(air-cooled)
The condenser is the component in which the gas coming from the compressor is cooled down, condensed and
liquefied. Under no circumstances must the temperature of the ambient air exceed the nominal values. It is also
important that the condenser unit is kept free from dust and other impurities.
11.7 Condenser
(water-cooled)
The condenser is the component in which the gas coming from the compressor is cooled-down, condensed and
liquefied.
The water inlet temperature must not exceed the nominal values. Likewise, a correct flow must be ensured. The water
entering the condenser must be free from impurities.
11.8 Cooling-water
regulating
valve
The cooling-water controller serves to keep the condensation pressure or the condensation temperature constant
during water cooling. When the dryer is switched off, the valve automatically blocks the cooling-water flow.
11.9 Filter
dryer
Despite controlled vacuuming, traces of moisture can accumulate in the refrigeration cycle. The filter dryer serves to
absorb this moisture and to bond it.
11.10 Capillary tube
The capillary tube is a copper tube with a reduced diameter which is located between the condenser and the
evaporator, serving as a restrictor to reduce the pressure of the refrigerant. The pressure reduction serves to reach an
optimum temperature inside of the evaporator. The lower the outlet pressure at the capillary tube, the lower the
evaporation temperature.
The length and the inner diameter of the capillary tube are exactly dimensioned to ensure the performance of the
dryer. Settings or maintenance works are not required.
11.11 Aluminium heat exchanger
The heat exchanger module consists of an air/air heat exchanger, an air/refrigerant heat exchanger, and of a high-
performance separator. The compressed air flows top-down through the heat exchanger. The large cross-sections of
the flow passages cause low flow rates and low compressed-air losses. In the air/air heat exchanger, the heat
exchange is effected in a reverse current. This guarantees maximum heat transfer. The heat transfer in the
air/refrigerant heat exchanger also takes place in a reverse current. This allows full evaporation of the refrigerant. The
high-performance separator ensures almost complete separation of the condensate. Maintenance of the high-
performance separator is not required.
11.12 Hot-gas bypass valve
At partial load, the valve directly returns a part of the hot gas to the suction line of the refrigerating compressor. The
evaporation temperature and the evaporation pressure remain constant.
11.13 Refrigerant pressure switches LPS – HPS
To ensure the operational reliability and the protection of the dryer, a series of pressure switches are installed in the
gas cycle.
LPS :
Low-pressure appliance on the suction side of the compressor, which is triggered when the pressure dros
below the predetermined value. The values are reset automatically as soon as the nominal conditions are re-
established.
HPS :
The high-pressure appliance on the discharge side of the compressor is activated when the pressure exceeds
the predetermined value. The values are not reset automatically when the nominal conditions are re-
established. Reset takes place manually via a button on the appliance.
Summary of Contents for DRYPOINT RA 1080-8800
Page 24: ...Technical data 24 DRYPOINT RA 1080 8800 10 2 Technical data DRYPOINT RA 1080 8800 3 460 60 ...
Page 42: ...Maintenance troubleshooting spare parts and dismantling 42 DRYPOINT RA 1080 8800 ...
Page 45: ...Appendices DRYPOINT RA 1080 8800 45 13 1 2 Dimensions DRYPOINT RA 2400 4400 ...
Page 46: ...Appendices 46 DRYPOINT RA 1080 8800 13 1 3 Dimensions DRYPOINT RA 5400 6600 ...
Page 47: ...Appendices DRYPOINT RA 1080 8800 47 13 1 4 Dimensions DRYPOINT RA 7200 8800 ...
Page 49: ...Appendices DRYPOINT RA 1080 8800 49 13 2 2 Exploded diagram DRYPOINT RA 1080 2200 AC ...
Page 50: ...Appendices 50 DRYPOINT RA 1080 8800 13 2 3 Exploded diagram DRYPOINT RA 2400 4400 AC ...
Page 51: ...Appendices DRYPOINT RA 1080 8800 51 13 2 4 Exploded diagram DRYPOINT RA 5400 6600 AC ...
Page 52: ...Appendices 52 DRYPOINT RA 1080 8800 13 2 5 Exploded diagram DRYPOINT RA 7200 8800 AC ...
Page 53: ...Appendices DRYPOINT RA 1080 8800 53 13 2 6 Exploded diagram DRYPOINT RA 1080 2200 WC ...
Page 54: ...Appendices 54 DRYPOINT RA 1080 8800 13 2 7 Exploded diagram DRYPOINT RA 2400 4400 WC ...
Page 55: ...Appendices DRYPOINT RA 1080 8800 55 13 2 8 Exploded diagram DRYPOINT RA 5400 6600 WC ...
Page 56: ...Appendices 56 DRYPOINT RA 1080 8800 13 2 9 Exploded diagram DRYPOINT RA 7200 8800 WC ...
Page 71: ...Appendices DRYPOINT RA 1080 8800 71 ...
Page 72: ...Appendices 72 DRYPOINT RA 1080 8800 ...
Page 73: ...Declaration of conformity CE DRYPOINT RA 1080 8800 73 14 Declaration of conformity CE ...
Page 74: ...Declaration of conformity CE 74 DRYPOINT RA 1080 8800 ...