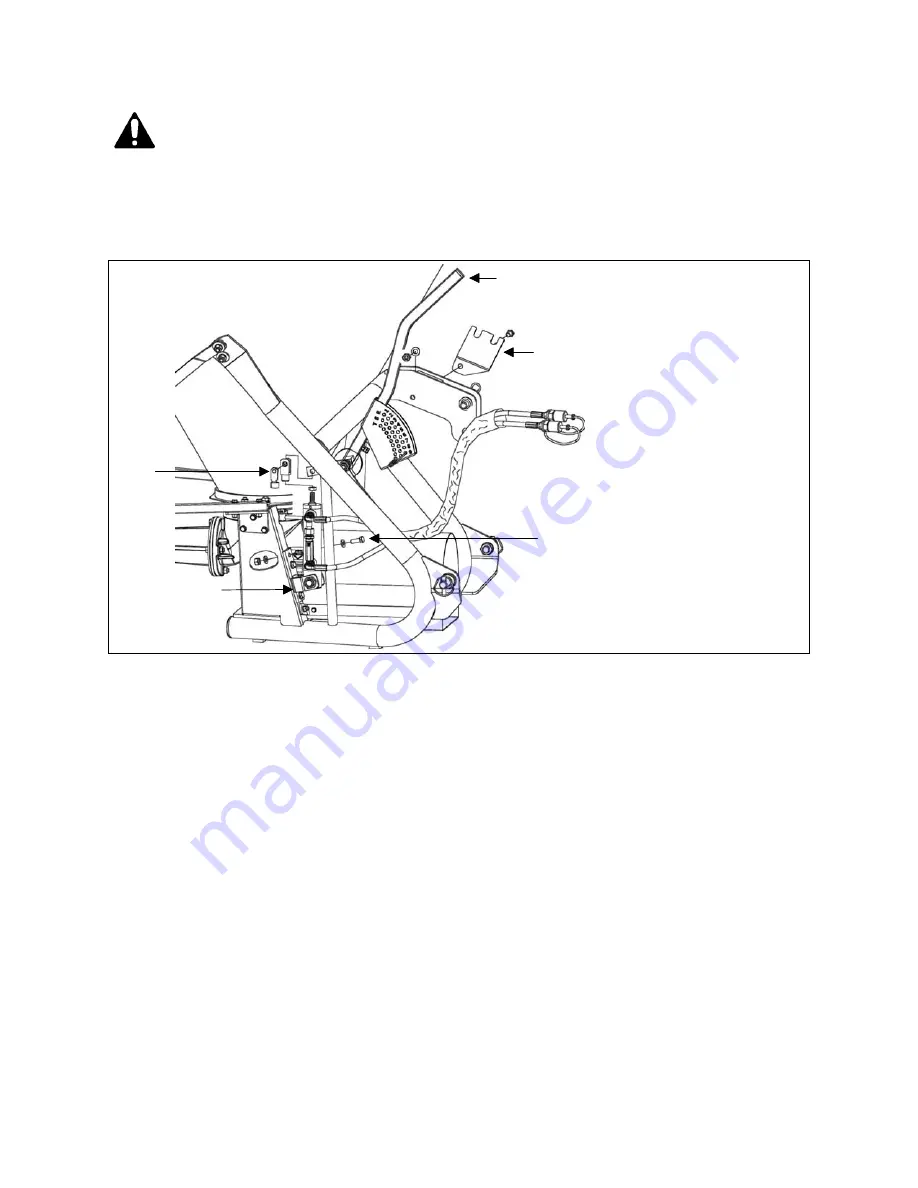
WARNING: High pressure hydraulic oil leaks can penetrate skin resulting in
injury, gangrene or death. Be sure to relieve any hydraulic oil pressure before
disconnecting any lines or pipes between spreader and tractor hydraulic system.
Check for oil leaks using a cardboard, never use hands.
The hydraulic gate control is designed to be assembled to the right hand side of the
pendular spreader. To assemble, proceed as follows:
1. With the spreader unhooked from the tractor and positioned on stable ground, line
up the three holes on the cylinder bracket to the holes on the side plate by the
gearbox
(see #1, fig. 16)
and secure them with the M10x30 bolts, the Ø10 washers
and M10 nuts
(see #2, fig. 16)
.
2. Remove the fixing pin that is assembled to the top cylinder yoke
(see #3, fig. 16)
.
Line up the hole on the top cylinder yoke with the hole on the opening lever bracket
that is on the spreader. Slide the fixing pin through the holes and secure it on the
yoke.
3. Secure the hydraulic hose retainer plate with the slots facing outwards to the left of
the top hitch bracket through the bolt and secure it with the M12x30 bolts, the Ø12
washers and M12 lock nuts
(see #4, fig. 16)
.
4. Remove the opening lever
(see #5, fig. 16)
from the frame as it will not function with
the hydraulic remote gate control assembled.
5. Position hydraulic hoses in a safe route towards the tractor and place the remotes
on the hose retainer bracket.
6. Tighten all hardware securely.
O
PERATION
23
BEFCO
T
URBO
-H
OP
O
PERATOR
’
S
M
ANUAL
Fig. 16 - Hydraulic gate control.
1
2
3
5
4