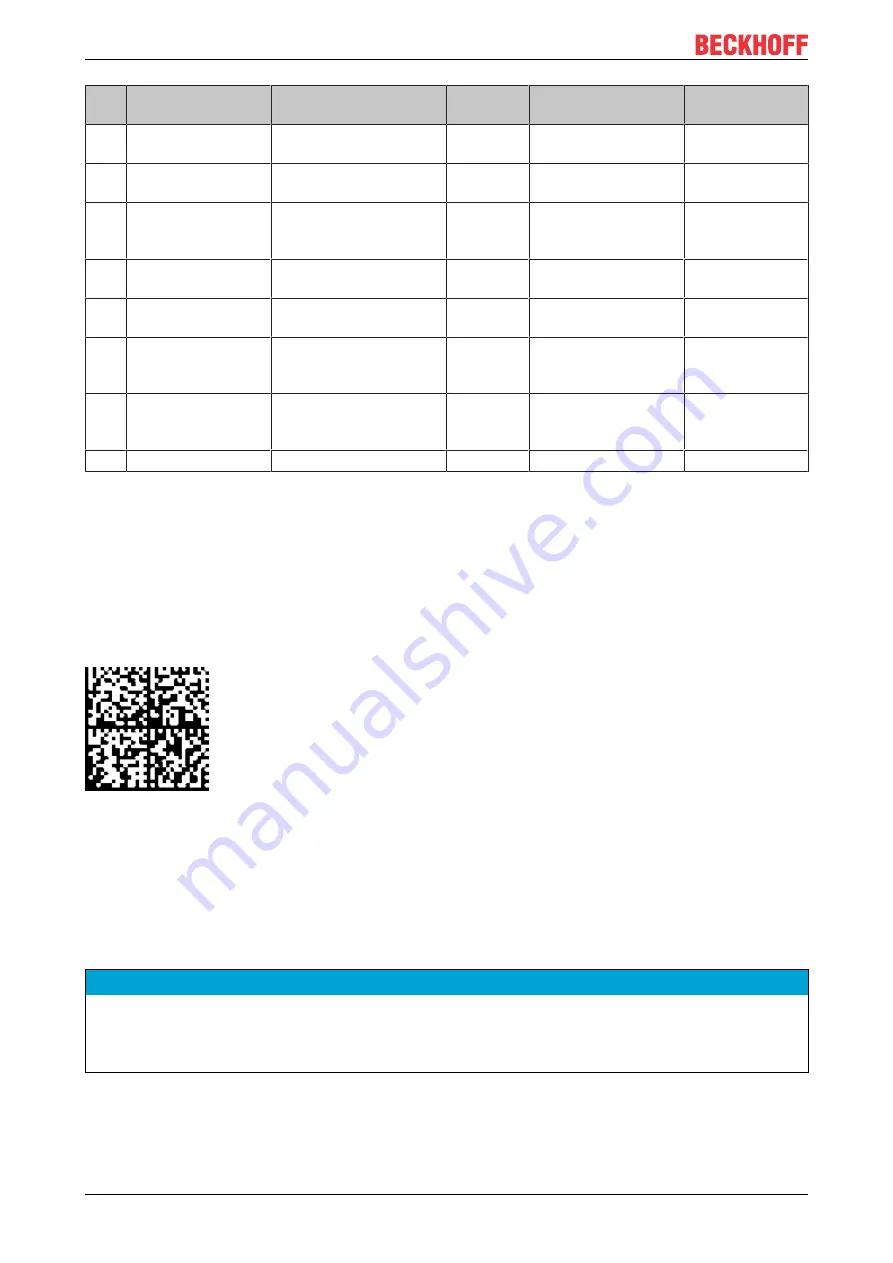
Appendix
EPP6228-0022
74
Version: 1.3
Posi-
tion
Type of
information
Explanation
Data
identifier
Number of digits
incl. data identifier
Example
1
Beckhoff order
number
Beckhoff order number
1P
8
1P
072222
2
Beckhoff Traceability
Number (BTN
)
Unique serial number,
see note below
SBTN
12
S
BTNk4p562d7
3
Article description
Beckhoff article
description, e.g.
EL1008
1K
32
1K
EL1809
4
Quantity
Quantity in packaging
unit, e.g. 1, 10, etc.
Q
6
Q
1
5
Batch number
Optional: Year and week
of production
2P
14
2P
401503180016
6
ID/serial number
Optional: Present-day
serial number system,
e.g. with safety products
51S
12
51S
678294
7
Variant number
Optional: Product variant
number on the basis of
standard products
30P
32
30P
F971, 2*K183
...
Further types of information and data identifiers are used by Beckhoff and serve internal processes.
Structure of the BIC
Example of composite information from positions 1 to 4 and with the above given example value on position
6. The data identifiers are highlighted in bold font:
1P
072222
S
BTNk4p562d7
1K
EL1809
Q
1
51S
678294
Accordingly as DMC:
Fig. 46: Example DMC
1P
072222
S
BTNk4p562d7
1K
EL1809
Q
1
51S
678294
BTN
An important component of the BIC is the Beckhoff Traceability Number (BTN, position 2). The BTN is a
unique serial number consisting of eight characters that will replace all other serial number systems at
Beckhoff in the long term (e.g. batch designations on IO components, previous serial number range for
safety products, etc.). The BTN will also be introduced step by step, so it may happen that the BTN is not yet
coded in the BIC.
NOTE
This information has been carefully prepared. However, the procedure described is constantly being further
developed. We reserve the right to revise and change procedures and documentation at any time and with-
out prior notice. No claims for changes can be made from the information, illustrations and descriptions in
this information.