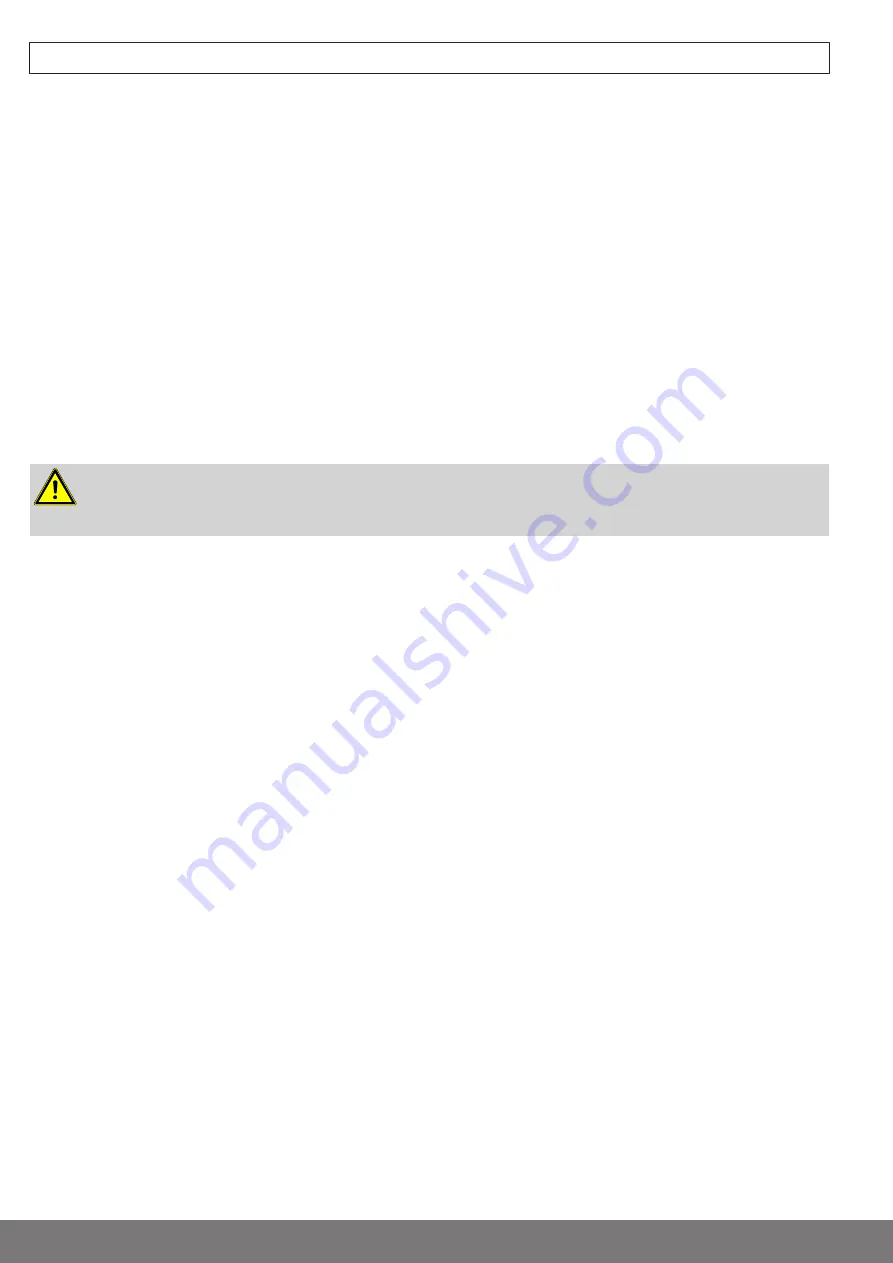
Safety instructions
The following safety instructions and warnings are intended to avert hazards and to prevent property damage and personal injury.
Instructions for the user
General information
•
The drive must be disconnected from its power source during cleaning and maintenance and when re-
placing parts.
•
All work, including maintenance and cleaning, on electrical installations as well as other system parts
must always be performed by trained technicians, in particular qualified electricians.
•
Children from the age of 8 years and persons with reduced physical, sensory or mental capabilities or
lack of experience and/or knowledge may use these devices, provided they are supervised or have
been instructed in the safe use of the device, and have understood the hazards involved. Children must
not play with the device.
•
Systems have to be checked regularly by authorised specialists for wear and damage.
•
Always put damaged systems out of operation immediately until they are repaired by an authorised
specialist.
•
Do not operate equipment if people or objects are within the danger zone.
•
Observe the danger zone of the equipment during operation.
•
Ensure that there is adequate clearance (at least 40 cm) between moving parts and adjacent objects.
Caution
Safety instructions for avoiding serious injuries.
•
Crushing or shearing points must be avoided or protected.
Instructions for installation and commissioning
General information
•
Observe the safety instructions in EN 60335-2-97. Please note that this list of safety instructions is not
exhaustive, since it would be impossible for the standard to include all sources of danger. For example,
the design of the operated product, the way the drive works in the situation it is installed in or even the
way the end product is mounted in the end user’s place of use cannot be taken into consideration by
the drive manufacturer.
If any questions or uncertainties regarding the safety instructions contained in the standard arise,
please contact the manufacturer of the part or end product in question.
•
All applicable standards and regulations for electrical installation must be complied with.
•
All work, including maintenance and cleaning, on electrical installations as well as other system parts
must always be performed by trained technicians, in particular qualified electricians.
•
Only use spare parts, tools and accessory devices which have been approved by the drive manufac-
turer.
Unapproved third-party products or modifications to the system and its accessories represent a risk to
your safety and the safety of others. This means that the use of unapproved third-party products, or
modifications which have not been agreed with or approved by us, are prohibited. We do not accept li-
ability for damage or injury arising from such actions.
•
Position switch with OFF presetting within sight of the driven product, but away from moving parts, at a
height of over 1.5 m. This must not be publicly accessible.
•
Permanently mounted control devices must be positioned where they can be seen.
•
Rated torque and duty cycle must be suitable for the requirements of the driven product.
Technical data - rated torque and service life can be found on the type plate of the tubular drive.
•
Hazardous moving parts of the drive must be installed at a height of over 2.5 m above floor level or any
other surface from which the drive can be accessed.
•
To ensure safe operation of the system after commissioning, the limit positions must be correctly set/
programmed in.
•
Drives with a H05VV-F connecting cable may only be used indoors.
•
Drives with a H05RR-F, S05RN-F or 05RN-F connecting cable may be used both indoors and outdoors.
•
To connect the drive to the driven part, solely mechanical accessory components made by the drive
manufacturer from the current product catalogue may be used. The components must be installed in
accordance with the manufacturer's instructions.
4 - en
Summary of Contents for E12
Page 25: ...Declaration of conformity 25 en ...
Page 26: ...26 ...
Page 27: ...27 ...
Page 28: ......