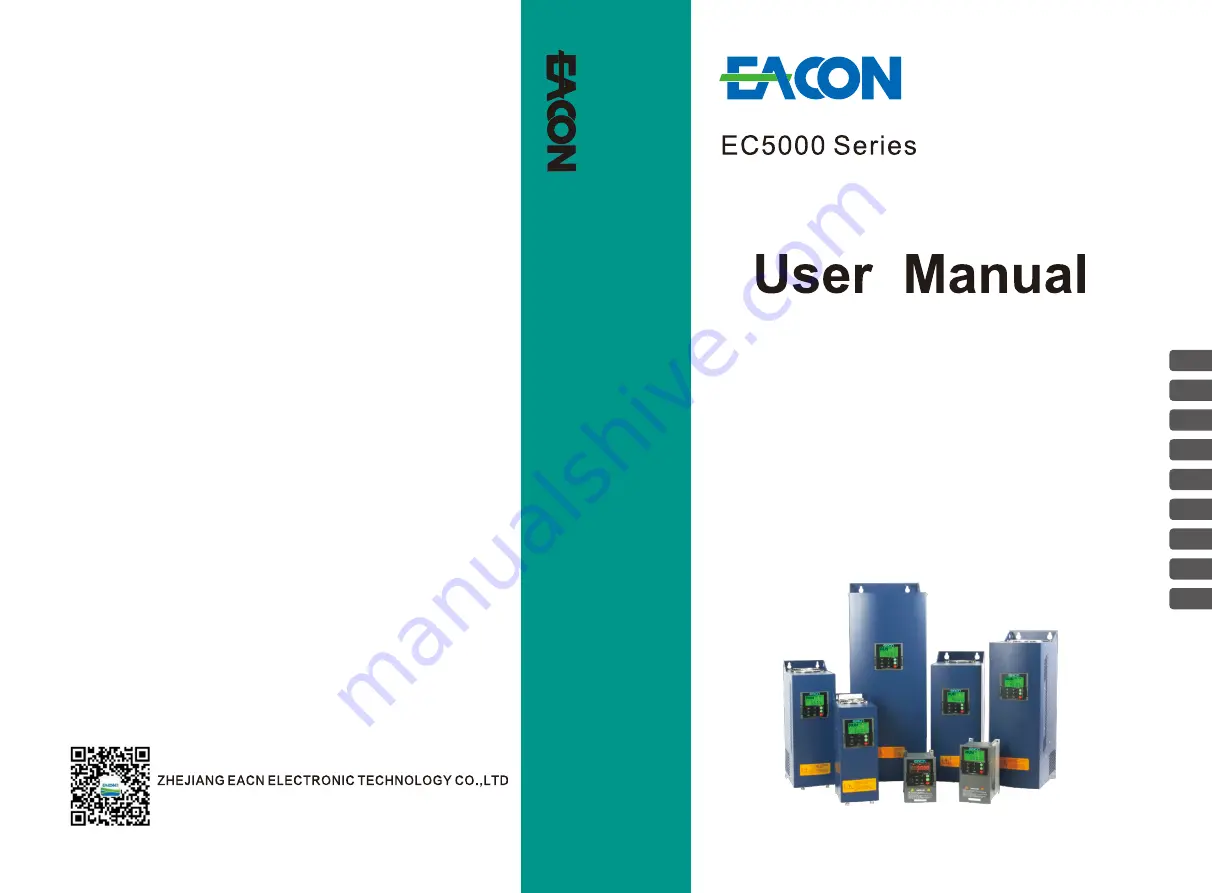
E-mail:[email protected]
AC Motor Driver
Manufacturer:
1
2
3
4
5
6
7
8
9
Read below information before use
Installation and Wire Layout
Operation and inspection
Operation keypad Panel
Description of Functional Parameter
MODBUS Communication Protocol
The diagnosis and the exclusion for the abnormalities
Maintenance inspection
Appendix
V2.5
Website:www.eacon.cc