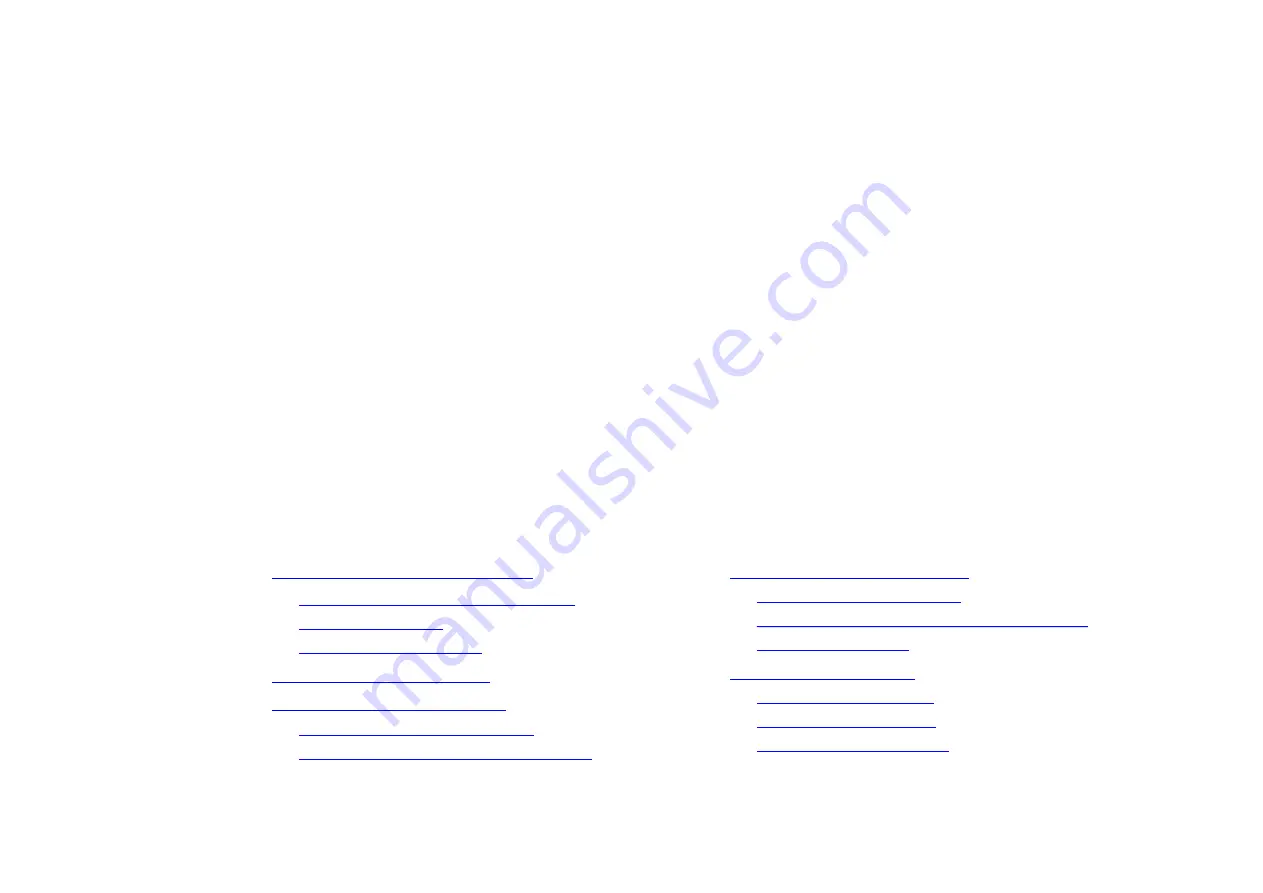
890SD Standalone Drive
5-1
890CS Common Bus Supply - Frames B & D; 890CD Common Bus Drive and 890SD Standalone Drive - Frames B, C & D
8
9
10
11
A
B
C
D
1
2
3
4
6
7
E
Chapter 5
890SD Standalone Drive
This chapter describes the mechanical and electrical installation of the 890SD Standalone Drive. It
discusses configuring your system, and how to turn the motor for the first time.
Follow the steps for a successful installation.
♦
Step 1: Mechanical Installation
Mechanical Installation Diagram
♦
♦
890SD Standalone Drive terminals
♦
Configure the 890SD Standalone Drive
♦