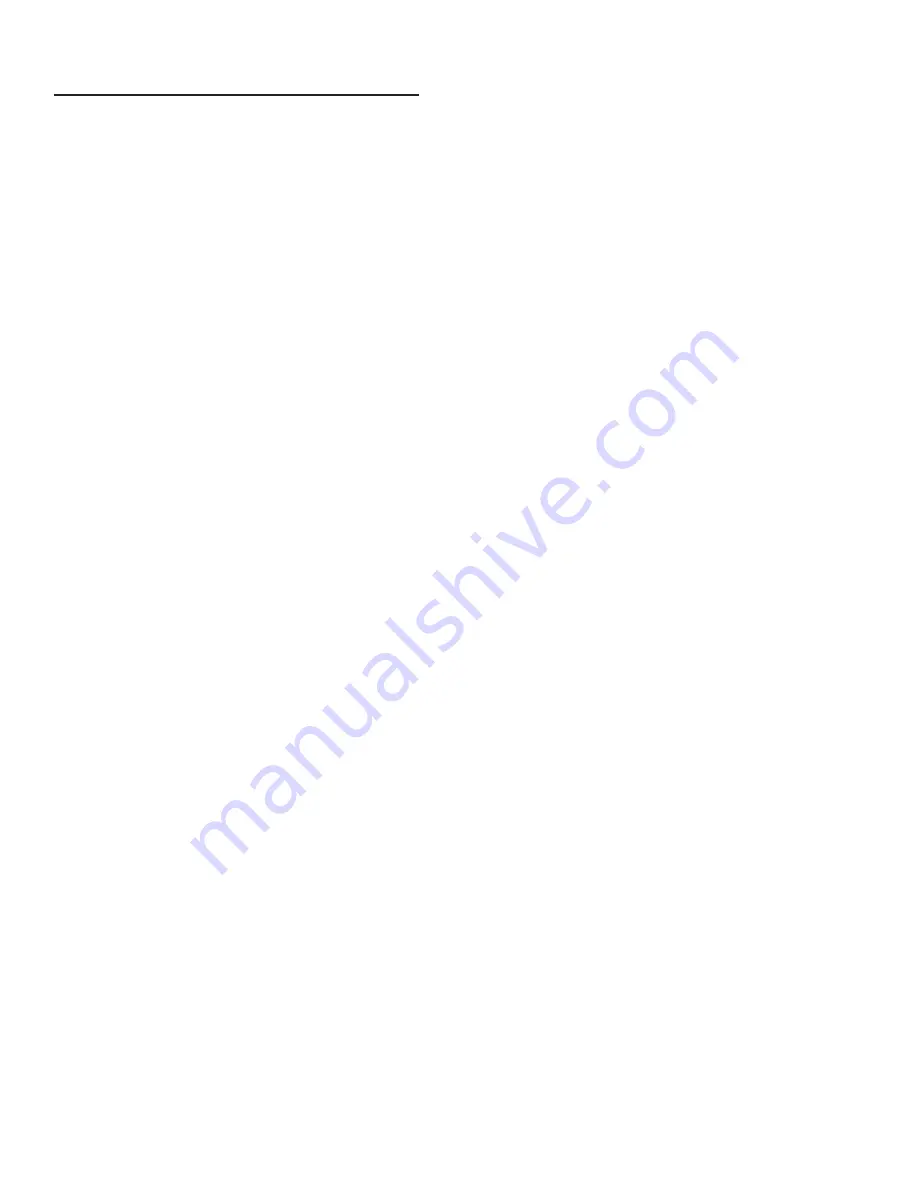
Manual, BWL-100.doc
I
NSTALLATION
I
NSTRUCTIONS
– BWL-100
1. For pit-mounted units, check that the pit conforms to the pit diagram.
Note: If the unit is to be placed into a pit, the required electrical and hydraulic connections to the dock lift should
be made before it is set into place.
2. Mount the power unit in the desired location. The standard 8’ hose will allow the power unit to be mounted
immediately adjacent to the lift. For mounting in other locations, a longer hose will be required. (Use ½” SAE
100R2 2-wire hydraulic hose with a 3,000 psi working pressure rating.)
3. Using an appropriate wiring method, connect the power supply to the power unit’s motor relay. Verify that the
motor supply voltage is the same as that shown on the machine dataplate (located on the middle of the right
platform side). Also verify that the correct control transformer primary leads are connected to the power supply
at the motor relay’s terminals.
4. Remove all steel strapping and shipping materials from the lift. Do not remove the lifting tabs.
5. Use rigging to pick up the unit at the two lifting tabs (one on each end of the platform) and move the lift into
place. Note: If the lift is being pit-mounted, guide the hose and the wires or cable into the pit (such as when a pit
conduit is present) when lowering it. Use care to avoid damage to the lift’s internal electrical and hydraulic
components from the underside. Remove the lifting tabs.
6. Connect the ½” hydraulic hose between the power unit and the lift’s frame.
Note: First, either flush or blow out the hose and fittings if any contaminants are observed inside them.
7. Install a jumper wire from terminal #3 to terminal #4 in the power unit’s control enclosure. Verify that the
overload relay setting matches the motor’s full-load amperage at the selected supply voltage.
8. Use the pendant control to raise the platform just high enough to allow the table’s safety maintenance props to be
placed into the frame. Use the manual valve to lower the platform so the leg set rests on the props. (Push down,
turn the knob CCW, and release it to open the lowering valve. Push down and turn CW to close it.)
9. Remove the jumper wire between terminal #3 and terminal #4.
10. At both the lift’s frame junction box and the power unit’s control enclosure, connect the five wires (including the
grounding wire) to the limit switch and toe guard circuit wires. See the electrical diagram in this manual.
11. Close and secure the control enclosure door and put the plastic cover over the power unit.
12. Cut and remove the plastic ties that hold the aluminum toe guard strips up during shipping. Verify that all the
strips drop down and move freely, and that the switch in the middle of each strip is not actuated.
13. Raise the platform to a height of 60”, measured from the bottom of the frame. Adjust the upper limit switch arm
(mounted on the non bridge-end of the frame) so that the motor turns off at that height.
14. Bleed the cylinders following the air bleed procedure at the bottom of the “Power Unit Operation” page.
Afterward, remove the maintenance props and lower the platform using the pendant control. Hold the “DOWN”
pushbutton for several seconds after the platform is lowered so that any air in the hose will be able to more easily
migrate to the reservoir.
15. While lowered, check the platform for proper lowered height, or that it is flush with the ground if pit mounted.
16. Raise the lift, install the maintenance props, and lower the leg set onto them once again.
17. Anchor the frame to the floor through each of the two 13/16” holes located near each frame corner.
18. Shim and/or grout under the full length of the frame sides.
19. Remove the maintenance props and operate the lift through several full up/down cycles. Verify that the upper
travel limit switch (mounted in the frame) and the toe guard switches (around the perimeter of the platform)
function properly.
20. Check the hydraulic oil level. It should be filled to within 3” of the top of the reservoir. If oil is needed, use an
anti-wear hydraulic oil with a viscosity grade of 150 SUS at 100°F (ISO 32 at 40°C) or a non-synthetic automatic
transmission fluid.
21. Clean up any debris or spilled oil, and verify that all of the warning and safety labels are intact.
3 of 16
Beacon Industries, Inc.