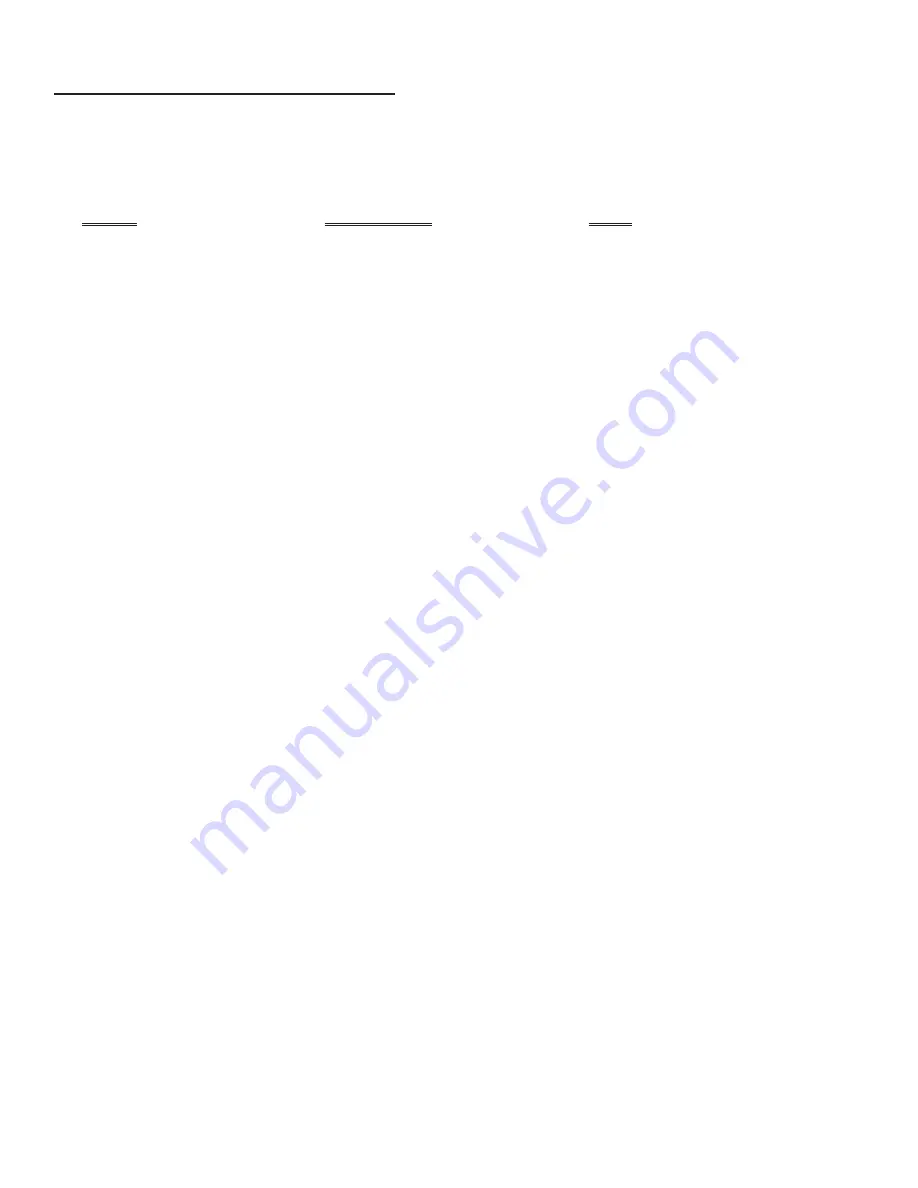
Manual, BWL-100.doc
T
ROUBLESHOOTING
G
UIDE
– BWL-100
WARNING: Care should be taken to identify all potential hazards and comply with all applicable safety procedures before
beginning troubleshooting or repairs.
CAUTION: Before performing any troubleshooting or repairs, the load must be removed from the platform. Then either raise the
platform and install the maintenance props, or fully lower the platform to the floor.
Only qualified individuals trained to understand mechanical devices and their associated electrical and hydraulic circuits, along
with the hazards that could result from them, should attempt troubleshooting and repair of this equipment.
Consult the factory for any problems not addressed in this manual.
Problem:
Possible cause(s):
Action:
Power unit doesn’t run when “UP”
button is pressed.
Transformer fuse is blown.
No supply voltage.
Upper-travel limit switch or wiring is
not connected; switch is engaged, or
bad.
Overload relay is tripped.
Control transformer failed.
Motor relay coil failed.
Test with meter; replace if bad.
Test with meter. Check fuses,
breakers, and overloads to determine
the cause.
Check connections to switch. Inspect,
test switch. Replace if bad.
Press reset button on overload relay.
Check for 24 VAC; replace if bad.
Test with meter; replace if bad.
Motor runs, platform doesn’t move.
Power unit not noisy.
Motor rotation is wrong.
Pump is failing to build pressure.
Lowering valve’s manual operator is
open.
Verify motor runs CW at the fan end.
Consult factory.
The manual operator should be pushed
down and rotated clockwise.
Motor hums or pump squeals, but the
platform does not move, or the
platform moves only slowly.
See last paragraph, above.
Excess voltage drop to motor; due to
power wire size too small, wire run
too long, or incoming voltage too low.
Motor is “single-phasing.”
Pressure relief opening at full pressure.
Contamination holding open the
lowering valve or the check valve.
Lowering valve’s manual operator is
open.
Same as above.
Check power installation for adequacy.
Check incoming voltage while motor
is running. Correct problem found.
Determine cause of loss of voltage on
one phase; correct.
Check for structural damage or binding
of the scissor legs, etc.
Check for platform overload
condition.
Remove and inspect. Clean per
instructions in “Power Unit
Operation.”
The manual operator should be pushed
down and rotated clockwise.
Platform raises, then drifts down.
See last two paragraphs, above.
Same as above.
Spongy or jerky platform movement.
Excessive air in the hydraulic cylinders.
Bleed air per the procedure described in
“Power Unit Operation.”
Platform
won’t
lower.
Toe guard switch or wiring is not
connected; switch is engaged, or bad.
Solenoid coil is bad.
Physical blockage of the structure.
Solenoid valve is plugged.
Check for a toe guard extrusion or
rubber corner that is stuck; adjust if
necessary. Inspect, test switches and
wiring with meter; replace if bad.
Check with multimeter on diode-check
function. (Reading for ohms will not
provide an accurate test of the coil.)
Inspect for foreign material or objects
that might block the leg set or its
rollers.
Remove and inspect. Clean per
instructions in “Power Unit
Operation.”
Platform lowers too slowly.
Pinched hose.
Velocity fuse locking (platform only
slowly creeps down).
Flow control valve sticking.
Check pressure hose for kinks.
Same as for jerky platform movement.
Remove and inspect. Clean per
instructions in “Power Unit
Operation”.
Platform lowers too quickly.
See last paragraph, above.
Same as above.
CAUTION: Do not use brake fluid or jack oils in the hydraulic system. If oil is needed, use an anti-wear hydraulic oil with a
viscosity grade of 150 SUS at 100°F (ISO 32 at 32°C) or a non-synthetic transmission fluid.
14 of 16
Beacon Industries, Inc.