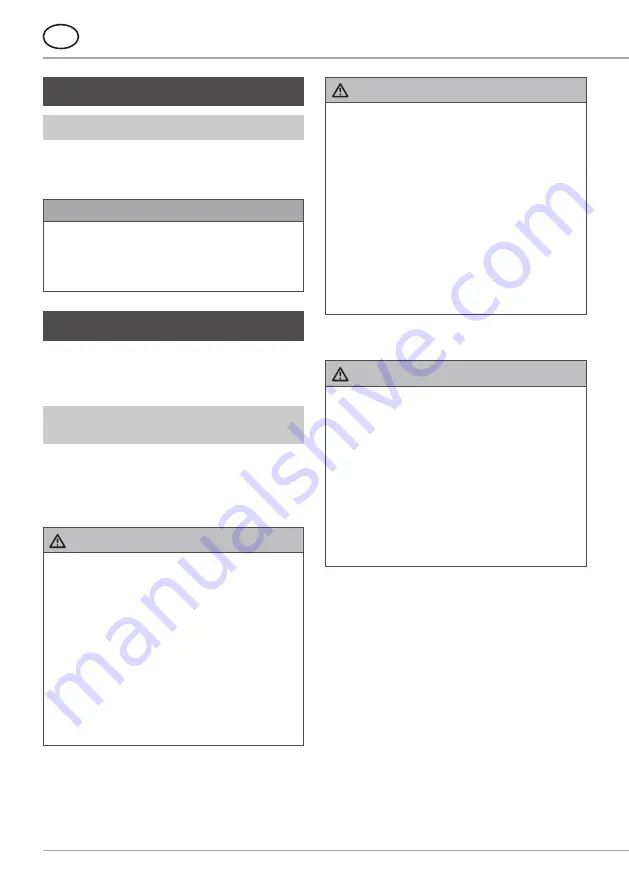
9
MABasic 200, 400, 450, 850
GB
Before using for the first time
Transport inspection
As standard, the machine is supplied with
the components indicated in the
Delivery
contents
section.
NOTE
►
Check for visible signs of damage or
missing items on delivery. Report an
incomplete or damaged delivery to
your dealer/supplier immediately.
Preparation
This section contains important instructions
on the required preparation before begin-
ning any work.
Additional safety measures for
certain work
Additional safety precautions must be
taken for the following operations with the
machine:
Non-horizontal work position
WARNING
Risk of injury from a falling machine .
When working in an inclined or vertical
position or during overhead work, the
machine must be secured using the safe-
ty lashing strap (21) supplied to prevent it
from falling.
►
Before using, check the safety lashing
strap for proper function. A damaged
safety lashing strap may not be used.
Replace a damaged safety lashing
strap immediately.
WARNING
►
Attach the safety lashing strap in such
a way that the machine can fall away
from the operator if it slips.
►
Lay the safety lashing strap as tightly
as possible around the handle of the
machine.
►
Before beginning work, check that the
safety lashing strap and the lock is
firmly seated.
►
Use the protective equipment stipulat-
ed in the section
Personal protective
equipment.
Work on scaffolding
WARNING
Risk of falling from sudden oscillating
movements of the machine .
When working on scaffolding, the
machine can make a sudden oscillating
movement on starting or in the event of
interruption to the power supply.
►
Secure the machine with the safety
lashing strap (21) supplied.
►
Wear a safety harness to protect
yourself against falling.
Before using for the first time