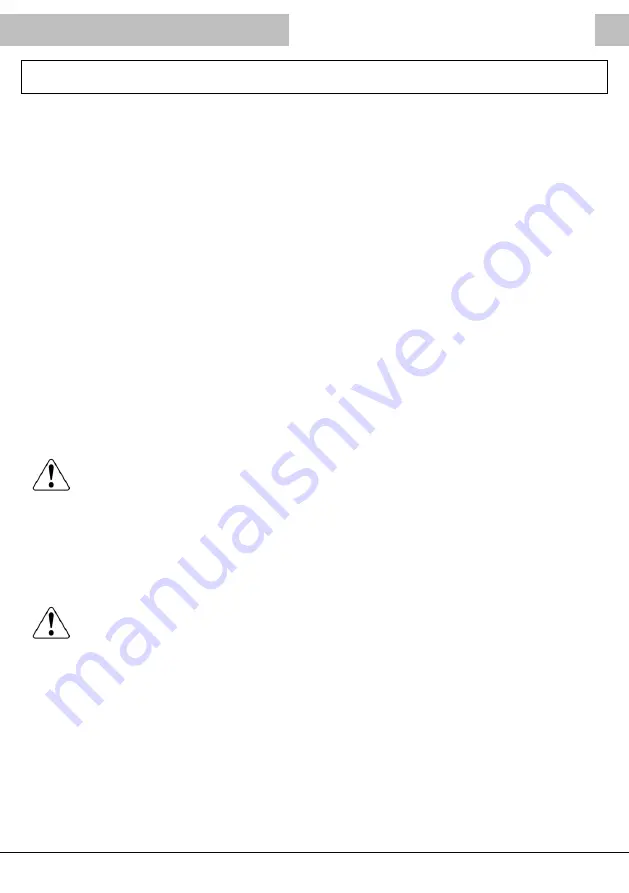
BCS 660HY Hydrostatic Commander
BCS660HY/0819
Page 13
Pre-Operation Checks
Refer to Figures 1a and 1b on pages 11-12
Before switching on the engine:
Check if the air intake grills for cooling the engine are clean.
Check the engine oil level
(fig. 1a, 22)
.
Check the gear oil level
(fig. 1a, 14)
.
Check that the PTO engagement lever is in neutral position
(fig. 1a, 3)
.
Chech that the air filter
(fig. 1b, 25)
is clean, if not then it must be cleaned.
Check that the safety equipment, including blade guards, is clean and free from obstructions,
and that the blade is sharp.
Check
t
hat the handlebar adjustment is working, by using the lever
(fig. 1a, 3)
and moving the
handlebars to the side position
(fig. 1a, 12)
.
Check that there is sufficient fuel in the tank.
IMPORTANT!
Use clean fuel, fresh and stored in appropriate containers, otherwise the
injector, fuel pump, carburetor, or the plug could be damaged.
Remove the cap
(fig. 1b, 18) and fill the fuel tank using a funnel with a fine filter.
Avoid the use of contaminated fuel, old or poorly preserved, the manufacturer and retailer
assume no responsibilities for damage to unit due to poor quality and poor preservation of the
fuel by the owner of the machine.
IMPORTANT!
Diesel engines. Every 30-40 days start the engine and let it run for a few
minutes to keep the injector and the pump operating, and to prevent it from sticking.