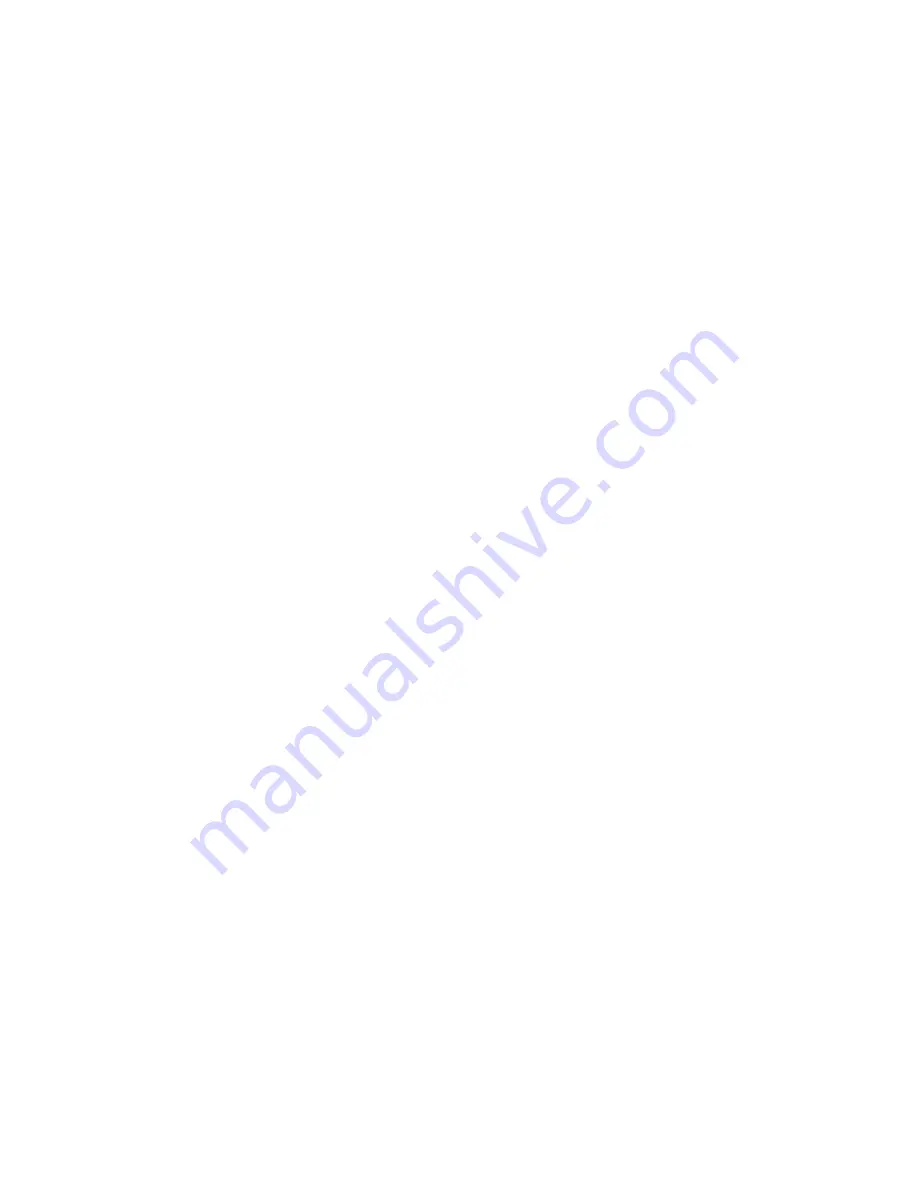
430
Rev. C
•
An uninterruptible calibration
A yellow dialogue box does not contain a STAT button next to the
countdown clock. During the initialization period there are several
uninterruptible calibrations mentioned in Cartridge Initialization (Init).
Uninterruptible calibrations are also encountered when a scheduled
calibration is postponed for 15 minutes. The user can typically
postpone a scheduled calibration by running samples when a
calibration is pending, or by interrupting the calibration (pushing the
STAT button) for up to 15 minutes.
Cartridge Initialization (Init)
When a new cartridge is installed the system must initialize the cartridge
and verify the performance of the sensors. In order to properly check the
electronics, fluidics, and performance of the sensors, the cartridge must go
through a 22 minute initialization (init).
When a new cartridge is placed correctly on the Rapidpoint 400 series
system, the system performs an electronic check, initializes the luer valve
on the cartridge, and primes the reagents. This is followed by a series of
calibrations to wet and establish the sensors’ performance.
The system is ready for its first sample analysis 22 minutes after the
cartridge is placed on the Rapidpoint 400 series system. Samples run at
this point are in retrocal mode. Twenty minutes after the init completes, the
system performs an uninterruptible 2-point calibration. After this
uninterruptible 2-point calibration is performed, a 1-point calibration is
scheduled 20 minutes later. If a sample is run before the 20 minute time
expires for this 1-point calibration during the initialization period, the
retrospective calibration with the sample replaces the scheduled 1-point
calibration and a new 20 minute timer begins.
Summary of Contents for RapidPoint 400 Series
Page 1: ...Service Manual 105953 Rev C 2003 02...
Page 29: ...Rev C Mechanical Descriptions 29 Rapidpoint 400 Series System left side 1 Diskette drive...
Page 62: ...62 Rev C...
Page 112: ...112 Rev C...
Page 114: ...114 Rev C...
Page 116: ...116 Rev C Rapidpoint 400 Series Systems Menu Map...
Page 117: ...Rev C System Diagrams and Cable Drawings 117 Fluidic Diagrams...
Page 118: ...118 Rev C...
Page 119: ...Rev C System Diagrams and Cable Drawings 119...
Page 120: ...120 Rev C...
Page 121: ...Rev C System Diagrams and Cable Drawings 121...
Page 122: ...122 Rev C...
Page 123: ...Rev C System Diagrams and Cable Drawings 123...
Page 124: ...124 Rev C...
Page 125: ...Rev C System Diagrams and Cable Drawings 125...
Page 126: ...126 Rev C...
Page 127: ...Rev C System Diagrams and Cable Drawings 127...
Page 128: ...128 Rev C Rapidpoint 400 Series Systems Electronic Block Text Diagram...
Page 131: ...Rev C System Diagrams and Cable Drawings 131 D C Power Harness Assembly 113836...
Page 132: ...132 Rev C Diskette Drive Cable Assembly 570255 Diskette Power Harness 570254...
Page 134: ...134 Rev C Inboard 2 Harness 113523 LCD Backlight Cable Assembly 108771...
Page 135: ...Rev C System Diagrams and Cable Drawings 135 Preamp Module Cable Assembly 570269...
Page 136: ...136 Rev C UIP Display Cable Assembly 570263 UIP LPT1 COM2 Cable Assembly 570267...
Page 138: ...138 Rev C Flex Circuit Display 570516 100 Pin Cable Assembly 111326 Patch Cord Cable 122254...
Page 139: ...Rev C System Diagrams and Cable Drawings 139 Fiber Bundle Assembly 1315271...
Page 140: ...140 Rev C...
Page 142: ...142 Rev C...
Page 148: ...148 Rev C...
Page 154: ...154 Rev C...
Page 258: ...258 Rev C...
Page 260: ...260 Rev C...
Page 262: ...262 Rev C Handle Pawl...
Page 263: ...Rev C Illustrated Parts Lists 263 Wash Waste Switch Rubber Feet...
Page 264: ...264 Rev C Display Display Bracket...
Page 267: ...Rev C Illustrated Parts Lists 267 Front Door Door Hook...
Page 268: ...268 Rev C Cartridge Interface Assembly Front Door Switch...
Page 271: ...Rev C Illustrated Parts Lists 271 Diskette Drive Diskette Drive Cable Shield...
Page 273: ...Rev C Illustrated Parts Lists 273 Connector UIP PCB UIP PCB with Cables...
Page 274: ...274 Rev C Main PCB Main PCB Attached to Frame...
Page 276: ...276 Rev C AQC Latch Assembly Front View AQC Latch Assembly Rear View 1 AQC latch assembly...
Page 277: ...Rev C Illustrated Parts Lists 277 Cover...
Page 282: ...282 Rev C Pump Housing Peri pump Motor and Mount...
Page 283: ...Rev C Illustrated Parts Lists 283 Peri pumps Spring Plate...
Page 284: ...284 Rev C Connector Block Cartridge Handle...
Page 285: ...Rev C Illustrated Parts Lists 285 Preamp Cable Cover...
Page 289: ...Rev C Illustrated Parts Lists 289 Power Module Frame Power Entry with Switch...
Page 290: ...290 Rev C Rear Interconnect Board Fan...
Page 291: ...Rev C Illustrated Parts Lists 291 Power Supply Patch Cord with Ferrite Filter...
Page 292: ...292 Rev C Hard Drive...
Page 296: ...296 Rev C Neon Board Assembly Part Number 131526...
Page 298: ...298 Rev C...
Page 302: ...302 Rev C...
Page 351: ...Rev C Replacing Components 351 a Remove the four thread forming screws from the motor mount...
Page 380: ...380 Rev C...
Page 381: ...Rev C Spare Parts 381 Spare Parts Spare Parts Listing 383...
Page 382: ...382 Rev C...
Page 386: ...386 Rev C...
Page 400: ...400 Rev C...
Page 426: ...426 Rev C...
Page 432: ...432 Rev C...
Page 438: ...438 Rev C...
Page 458: ...458 Rev C...