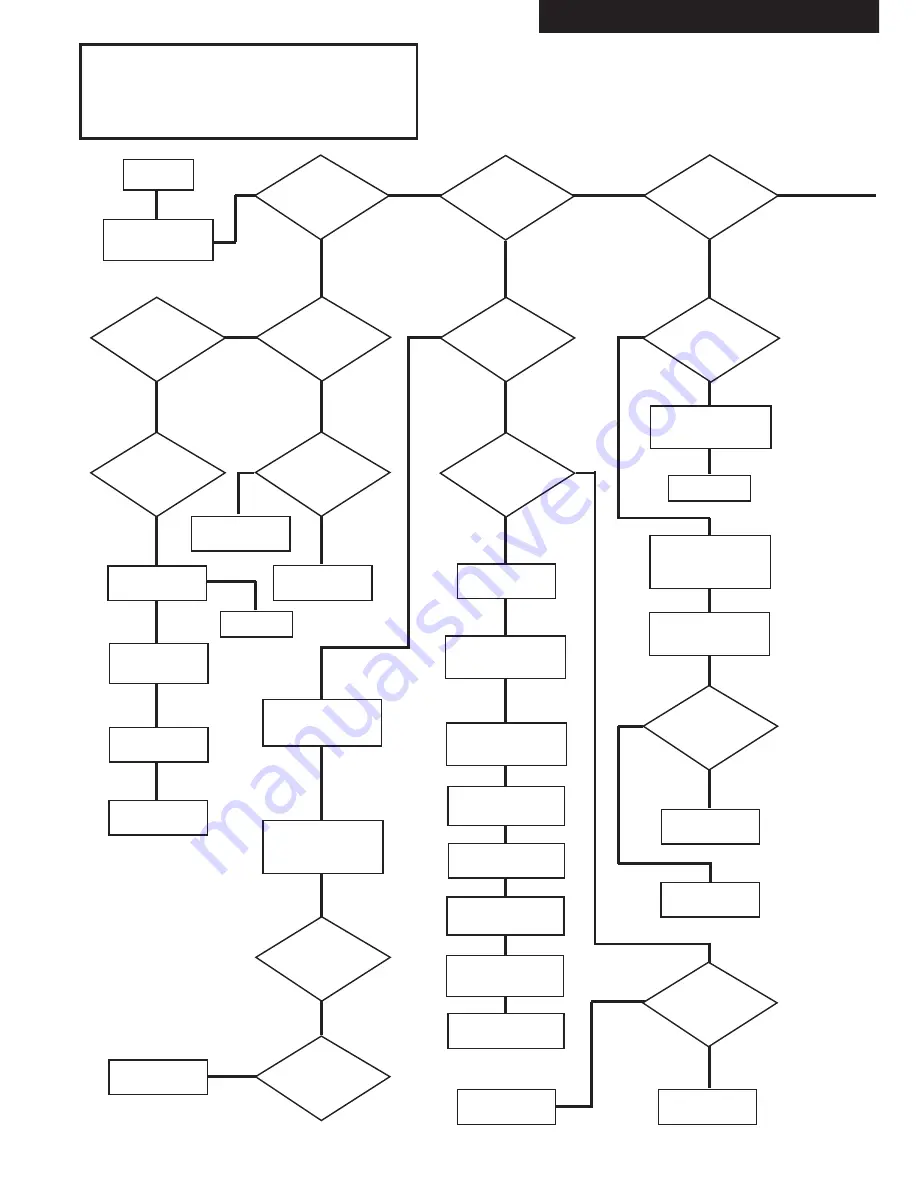
11.0
Fault Finding
42
START
Replace fan
Replace harness
Replace pressure
switch
Replace fan
Replace
thermostat
Does fan run ?
Is
there a clear
constant spark at
the electrode ?
Change
potentiometer
Is
there mains voltage
at S/L input ?
Is
there mains voltage
at Pump L output ?
Check fuse on
circuit board
Check pump wiring
Note: This can occur if
the boiler has
overheated
Reset by turning
control knob OFF, wait
10 seconds then turn
ON
Does
lockout light
go out ?
Is
"Fan On"
light on ?
Check control knob
is turned on
Check that the wires
are connected to the
thermostat sensor
Check that the fan &
pressure switch plug is
connected
Is there
continuity between
C & NC terminals
on the pressure
switch ?
Check pressure switch
pipes for leaking or
blockage
Note: Under cold
conditions fan run up
time may exceed
1 min
Ensure external
controls are calling
for heat
Does pump run ?
Is
"Pilot On"
light on ?
Is
lockout light
on ?
Is
"Boiler On"
light on ?
Is
there mains voltage
at P/L input ?
Is
there mains at
the fan
connection ?
Is there
continuity across
the overheat
thermostat ?
YES
NO
YES
YES
YES
YES
YES
NO
YES
YES
NO
NO
NO
NO
NO
YES
YES
YES
NO
NO
NO
NO
YES
NO
No continuity - change
sensor
Check continuity
across pilot solenoid
(1.5 K OHM)
No continuity - change
pilot solenoid
Check continuity
across sensor
(1 M OHM at 20
o
C)
Investigate
pump
Change PCB
No continuity
across fuse,
change fuse
YES
YES
Change PCB
Check & clean
electrode. Check gap &
lead
YES
Check external
wiring
NO
Check Potentiometer
(see table)
Before starting FAULT FINDING carry out
preliminary electrical system checks i.e.
Earth Continuity, Polarity, Short Circuit
and Resistance to Earth.
Summary of Contents for Solo 3 30 PF
Page 45: ...13 0 Notes 45 ...
Page 46: ...13 0 Notes 46 ...