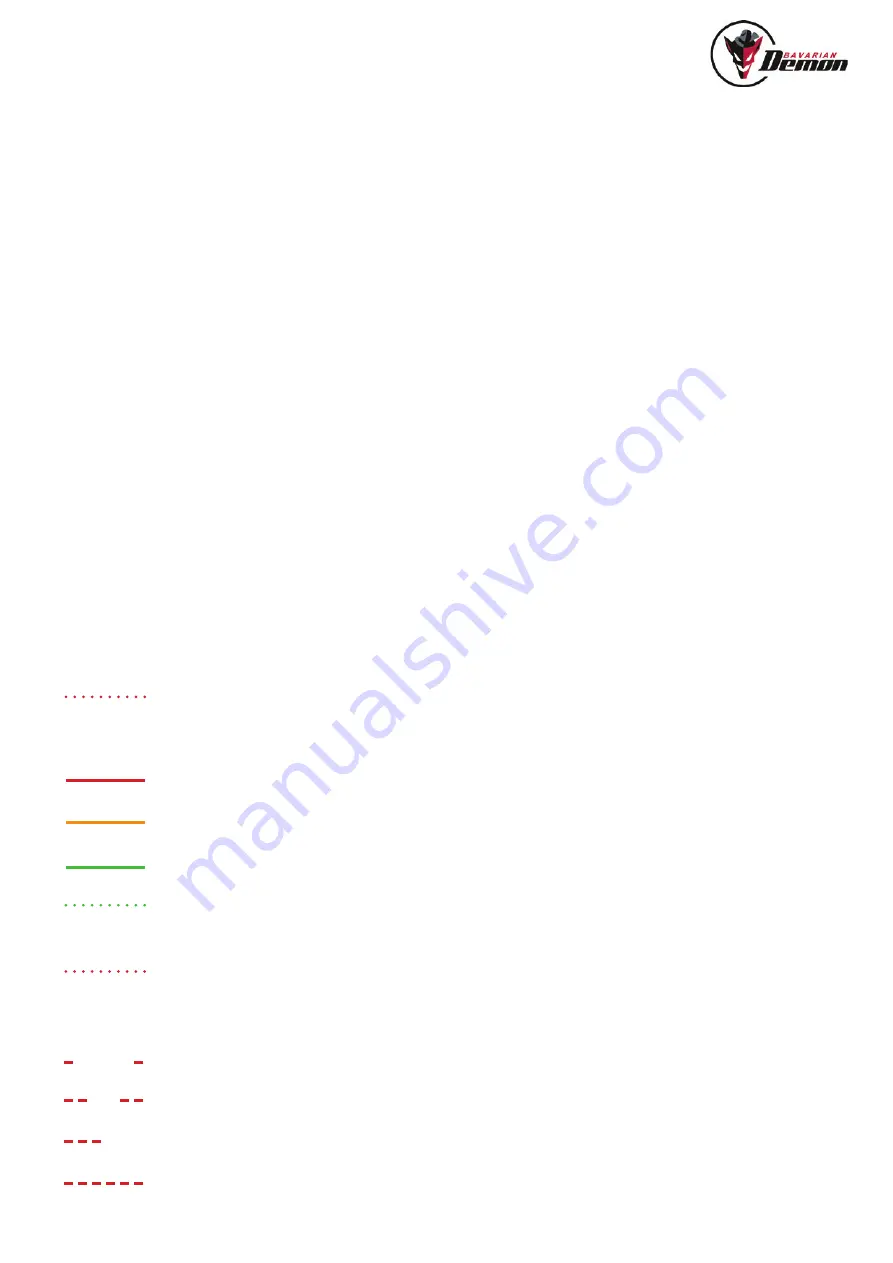
PLEASE NOTE WHEN CONNECTING
• As high servo currents can occur, a voltage supply should be routed directly to the device!
Also, the receiver should be supplied via the FBL system, not vice versa. Using the supplied cable loom and a BEC connected
to the receiver, the power supply via cable loom is possible. Anyway, a direct feed is preferable.
Use one of the following possibilities:
a) Battery connection / head 4 (in case no 4th head servo is used).
b) Programming connection (Note: using a Y-lead for easy handling, so the USB cable can be connected without unplugging the power cable).
c) In case of supply from a BEC controller, route a parallel supply cable (e.g. Y-cable) to either battery or programming connection of the FBL system. This
connection must not possess a signal line, i.e. the third pole may have to be cut.
d) For using only the tail gyro of the FBL system, you can either do a setup with deactivated head gyro (still using the internal mixer), or only connect the tail
gyro cables, plus one of the three-wired connectors (aileron or elevator input) only for supplying the receiver with power from the FBL system, connecting it
to any vacant socket of the receiver; preferably with disconnected signal-wire.
• Do not connect servos until the FBL system has been set to the correct servo type.
• Do not move the heli for the fi rst fi ve seconds after switching on (LED fl ashes red). The FBL system runs a self-test and needs standstill to do this, as otherwise
it does not activate the servos and starts to fl ash 3x red.
• In case using the cable loom: The cables coming from the receiver should all be laid as one common bundle. Single wires must not lie separately.
• The additional „head gyro“ and „tail gyro“ channels serve to set the respective gain (sensitivity) in fl ight. One potentiometer or slider on the transmitter each
should be assigned. As an alternative, and recommended for later on, a fi xed value can be programmed on the transmitter, a gyro menu can be used, or the
values can be programmed from the PC directly into the device if the corresponding channel is not connected. However, it is considerably easier and faster to
have a pot or slider at the transmitter to adjust directly in fl ight.
LED DISPLAY
SWITCHING ON
(fl ashes red)
Switch-on phase: do not move, no output of servo signals
OPERATION
(continuous red)
Centre of head gyro channel, minimum stabilisation (20%)
(continuous yellow-orange)
Active rigid stabilisation > 20%
(continuous green)
3SX only: Horizontal stabilisation ON
(fl ickering green)
3SX only: Horizontal stabilisation with collective pitch rescue action ON
SETTING UP
(fl ickering red)
(fl ickering red) If connected to [Diagnose] or [Trim] menu: Servos remain in neutral position
ERROR DURING SELF-TEST, NO SERVO SIGNAL OUTPUT
(1x)
Waiting
for
RC
signal
(2x)
Battery as from switch-on < 4V
(3x)
Movement during switch-on phase, repeat power-on
(6x)
3SX only: too extreme temperature (>55°C or <-15°C)
6