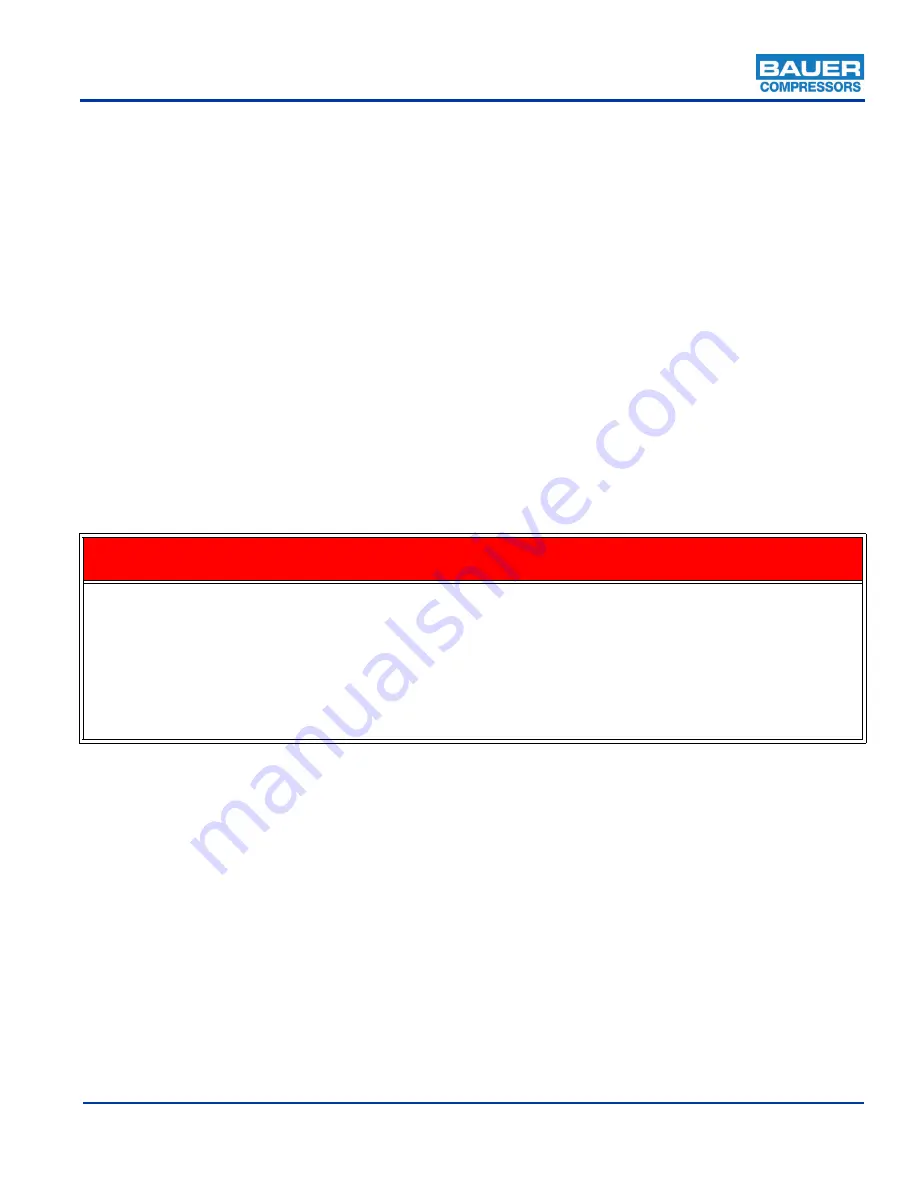
MVT26
October 2003
Section 4
Page 79
4.2.1.2
Cartridge
4.2.1.2.1
Cartridge Construction
The casing, top and bottom of all cartridges are aluminum and are packed with one or more of the follow-
ing ingredients.
1. A catalyst to convert carbon monoxide to carbon dioxide.
2. Activated carbon which absorbs oil vapors effecting taste and odor.
3. Molecular sieve to absorb oil and water.
4. An optional Securus
♦
sensor.
4.2.1.2.2
Cartridge Handling
1. Never open the protective packaging a cartridge comes in prior to its actual use. The highly sensitive
filter materials will absorb moisture from the atmosphere becoming saturated and useless.
2. Used cartridges must be disposed of in accordance with local regulations.
4.2.1.3
Coalescing Oil/Water Separator
The air leaving the final stage is cooled in the aftercooler to approximately 18 - 27°F (10 -15°C) above
ambient temperature and then enters the oil and water separator. The oil and water separator works by
means of a sintered metal filter which separates liquid oil and water particles from the compressed air.
4.2.1.4
Condensate Drain Valve
A manually operated valve used for maintenance and before start-up to drain the condensed liquids from
the coalescing oil and water separator.
4.2.1.5
Check Valves
Valves allowing compressed air to flow in only one direction. One is used to maintain pressure in the
chamber when the compressor is not operating. The other check valve prevents back-flow from filled
storage cylinders or tanks.
4.2.1.6
Bleed Valve
A manually operated valve used to release the pressure in the chamber before maintenance.
4.2.1.7
Pressure Maintaining Valve
The pressure maintaining valve ensures that pressure is built up in the system from the start of delivery,
thus achieving constant optimum purification. It also assures proper working conditions for the final
stage of compression.
WARNING
Dynamic Loading
The rapid depressurizing and repressurizing of the oil and water separator during condensate draining sub-
jects it to metallurgical stresses. To prevent catastrophic failure with the possibility of damage, injury or
death the oil and water separator (P/N 079416) must be replaced after 44,000 load cycles. A load cycle
equals one depressurization- repressurization. The BAUER recommended frequency of condensate drain-
ing is every fifteen minutes and is a balance between maximizing the life of the oil and water separator
chamber and maintaining the quality of the delivered breathing air.