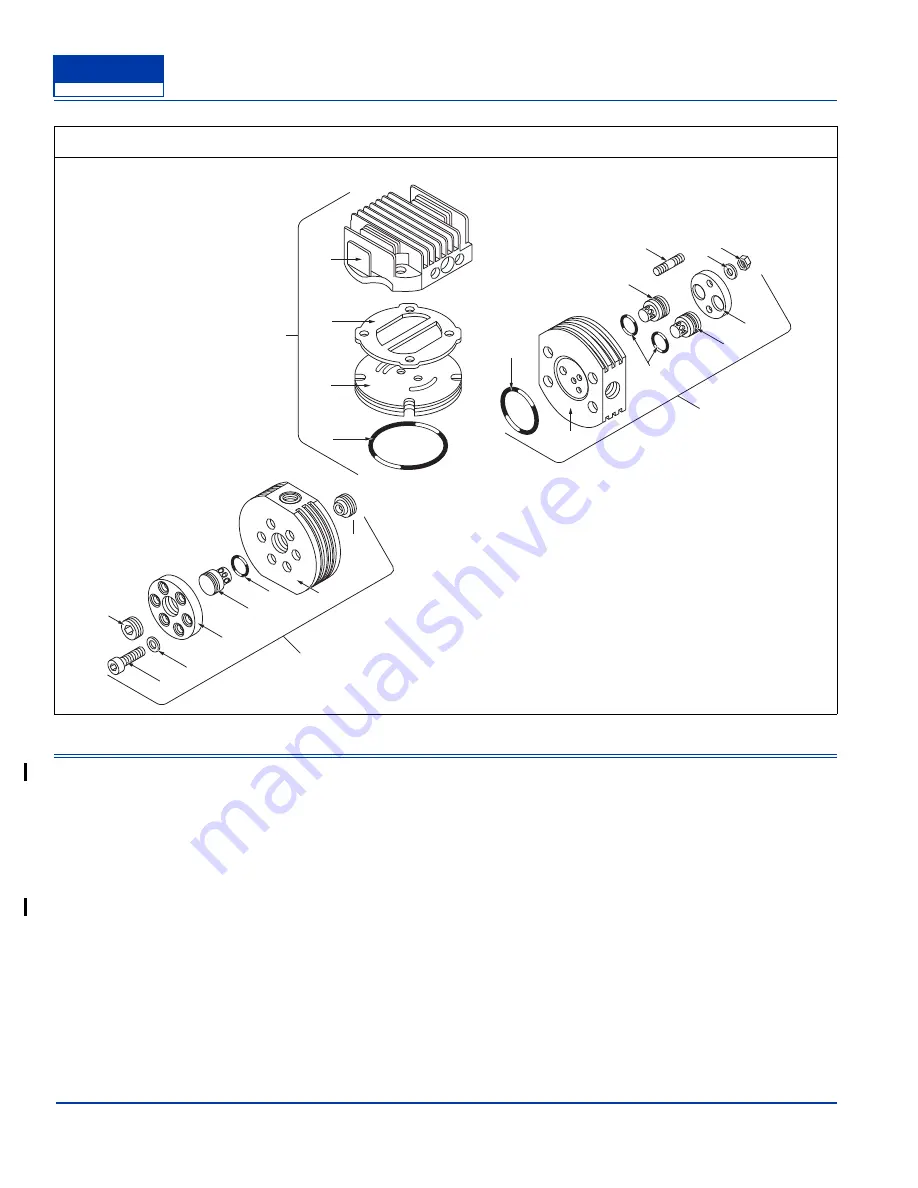
Junior II WT
Page 24
1st ed. Rev 0 Chg 3
BAUER
COMPRESSORS
#
KIT
Qty Part No.
Description
Notes
1
…
1
077179
1st Stage Valve Head Assembly
Items 2 through 5
2
…
1
58105
1st Stage Valve Head
3
…
1
58144
Gasket
4
.b.
1
N4860
Reed Valve
5
…
1
N3712
O-ring
6
…
1
069930
2nd Stage Valve Head Assembly
Items 7 through 15
7
a..
4
N1042
Hex Nut, Self Locking
8
…
4
N4640
Spring Washer
9
…
1
58133
2nd Stage Valve Cover
10
.b.
1
058136
Inlet Valve Assembly
11
…
2
N638
O-ring
12
…
1
58130
2nd Stage Valve Head
13
a..
1
N4868
O-ring
14 .b.
1
058135
Discharge Valve Assembly
Figure 3-12
Valve Heads and Valves
1
2
3
4
5
9
10
11
6
14
15
7
8
24
23
22
21
20
1
8
17
19
16
12
13