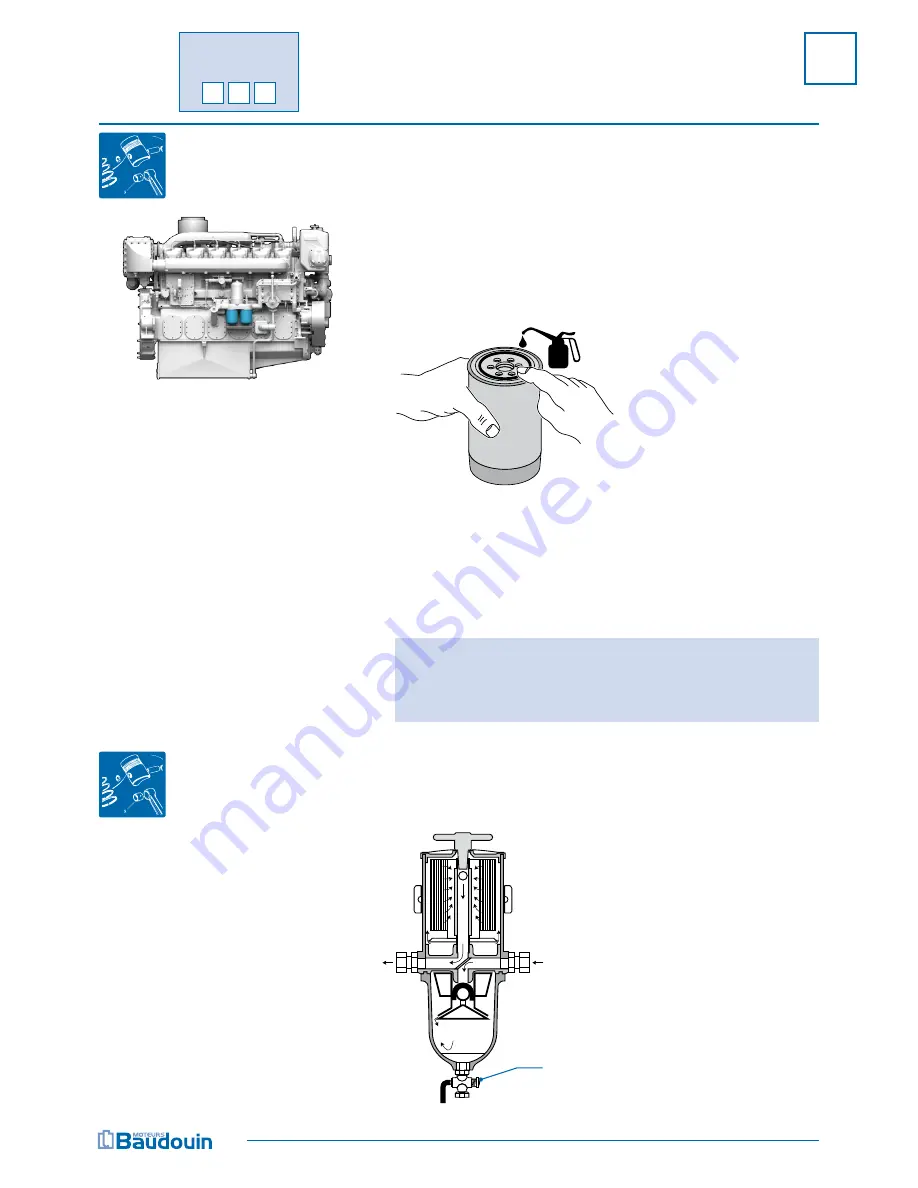
- 4/6 -
00374 - Edition 01 - September 1
1
Maintenance
D
400 - Maintenance operations
After 400 hours (P1 Service)
After 300 hours (P2 Service)
M1
Non-contractual
illustrations
PR Catalogue
see chapters
03
04
05
Catalogue
P.R.
05
Bleed the water separator filter- option
Open and let the water in the filter run until the fuel starts to
flow.
Bleed the water separator
Oil filter replacement
(ref. 15 04 168 0C)
The cartridges must be replaced every time the oil is
changed. Before removing the oil filters, clean the
surrounding surfaces.
The disposable oil cartridges are located on the starboard
side of the engine. To replace, unscrew the cartridges using a
filter wrench.
b
Clean the filter seal seat
on the engine.
b
Smear the seal with
engine oil, do not use
grease.
b
Screw the filter on
manually; do not use any
tools. Screw until the seal
makes contact and lock it
manually (an extra 3/4
turn).
b
Check the oil level. Pre-grease the engine then check the
oil level. Top up if necessary. Check that the filter is leakproof.
Catalogue
P.R.
04
Environmental precaution
There are laws regarding environmental protection and the
disposal of waste and hydrocarbons. To ensure compliance
with environmental protection laws, consult your local
authorities who will advise you.
Summary of Contents for 6 M26.2
Page 4: ......
Page 6: ......
Page 8: ......
Page 22: ......
Page 24: ......
Page 26: ......
Page 32: ......
Page 34: ......
Page 38: ......
Page 42: ......
Page 48: ......
Page 58: ......
Page 68: ......
Page 70: ......
Page 74: ......
Page 76: ......
Page 78: ......
Page 80: ......
Page 82: ......
Page 94: ......
Page 96: ......
Page 104: ......
Page 110: ......
Page 112: ......
Page 114: ......
Page 116: ......
Page 118: ......
Page 120: ......
Page 121: ......