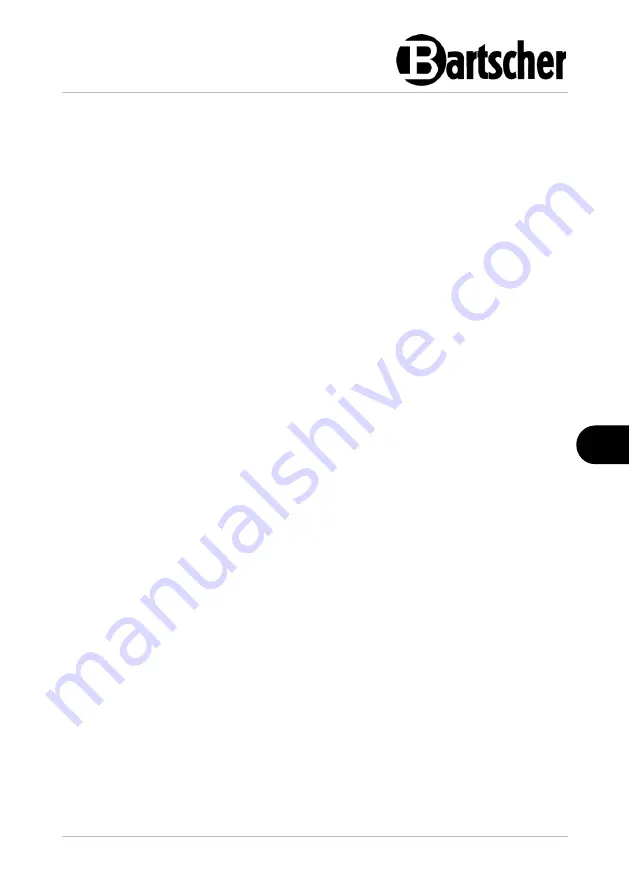
Cleaning and Maintenance
117623-117723
67 / 74
EN
7
Cleaning and Maintenance
7.1
Safety Instructions for Cleaning
• Before cleaning, disconnect the appliance from the power supply.
• Leave the appliance to cool down completely.
• Make sure water does not enter the appliance. Do not immerse the appliance in
water or other liquids during cleaning. Do not clean the appliance with a
pressurized water jet.
• Do not use any sharp or pointed, nor metal implements (knife, fork, etc.). Sharp
or pointed implements may damage the appliance, and when in contact with live
parts, they may cause electric shock.
• For cleaning, do not use any scouring agents that contain solvents nor corrosive
cleaning agents. They may damage the surface.
7.2
Cleaning
User's Regular Cleaning
1. To secure correct operation, hygiene and efficiency, clean the appliance
regularly at the end of each working day, and, if necessary, also in the
meantime or when the appliance is not to be used for a longer time.
With regular cleaning you may avoid burning leftovers of baked goods and roasts.
2. Remove food from the appliance.
3. Provided the grate, trays and GN containers were used, remove them.
4. Clean the thermal processing chamber with lukewarm water with soap, a soft
cloth or a sponge. Thoroughly rinse with fresh water, paying attention not to
leave any cleaning agent residues. To end with, dry the thermal processing
chamber thoroughly.
5. In the case of stubborn soiling, use special cleaning agents. Observe
instructions of such a cleaning agent's manufacturer.
6. Clean the appliance from the outside with a soft, damp cloth. Dry all cleaned
surfaces thoroughly. If needed, use only special cleaning agent for stainless
steel. Usage of inadequate cleaning agents may cause oxidation of the
appliance.
7. Regularly clean the fume extractor.