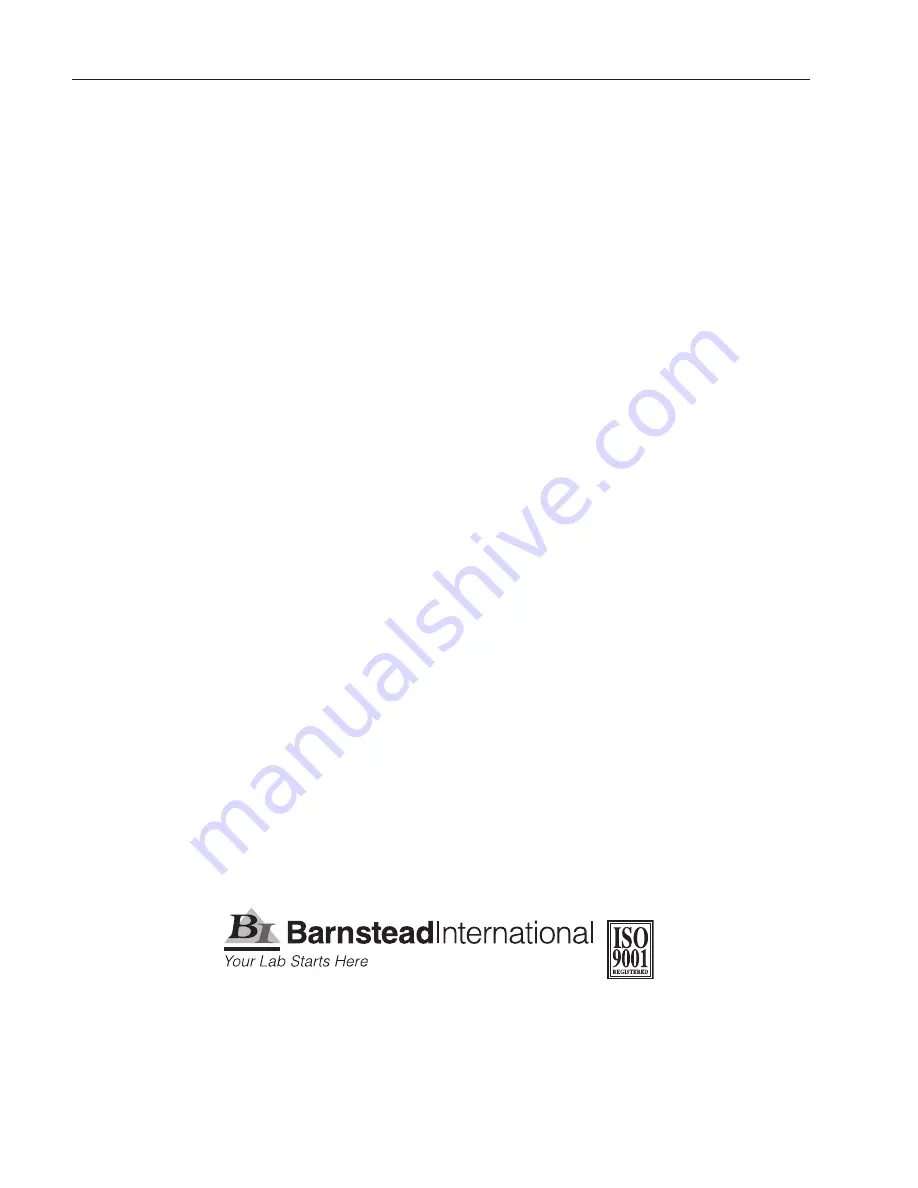
56
56
Two Year Limited Warranty
Barnstead International (“BARNSTEAD”) warrants that if a product manufactured by Barnstead shall be free of
defects in materials and workmanship for two (2) year from the first to occur of (i) the date the product is sold
by BARNSTEAD or (ii) the date the product is purchased by the original retail customer (the “Commencement
Date”). Except as expressly stated above, BARNSTEAD MAKES NO OTHER WARRANTY, EXPRESSED OR
IMPLIED, WITH RESPECT TO THE PRODUCTS AND EXPRESSLY DISCLAIMS ANY AND ALL WARRAN-
TIES, INCLUDING BUT NOT LIMITED TO, WARRANTIES OF DESIGN, MERCHANT ABILITY AND FITNESS
FOR A PARTICULAR PURPOSE.
An authorized representative of BARNSTEAD must perform all warranty inspections. In the event of a defect
covered by BARNSTEAD’s warranty, BARNSTEAD shall, as its sole obligation and exclusive remedy, provide
free replacement parts to remedy the defective product. In addition, for products sold by BARNSTEAD within
the continental United States or Canada, BARNSTEAD shall provide provide free labor to repair the products
with the replacement parts, but only for a period of ninety (90) days from the Commencement Date.
BARNSTEAD’s warranty provided hereunder shall be null and void and without further force or effect if there is
any (i) repair made to the product by a party other than BARNSTEAD or its duly authorized service represen-
tative, (ii) misuse (including use inconsistent with written operating instructions for the product), mishandling,
contamination, overheating, modification or alteration of the product by any customer or third party or (iii) use
of replacement parts that are obtained from a party who is not an authorized dealer of BARNSTEAD.
Heating elements, because of their susceptibility to overheating and contamination, must be returned to the
BARNSTEAD factory and if, upon inspection, it is concluded that failure is due to factors other than excessive
high temperature or contamination, BARNSTEAD will provide warranty replacement. As a condition to the
return of any product, or any constituent part thereof, to BARNSTEAD’s factory, it shall be sent prepaid and a
prior written authorization from BARNSTEAD assigning a Return Materials Number to the product or part shall
be obtained.
IN NO EVENT SHALL BARNSTEAD BE LIABLE TO ANY PARTY FOR ANY DIRECT, INDIRECT, SPECIAL,
INCIDENTAL, OR CONSEQUENTIAL DAMAGES, OR FOR ANY DAMAGES RESULTING FROM LOSS OF
USE OR PROFITS, ANTICIPATED OR OTHERWISE, ARISING OUT OF OR IN CONNECTION WITH THE
SALE, USE OR PERFORMANCE OF ANY PRODUCTS, WHETHER SUCH CLAIM IS BASED ON CON-
TRACT, TORT (INCLUDING NEGLIGENCE), ANY THEORY OF STRICT LIABILITY OR REGULATORY
ACTION.
The name of the authorized Barnstead International dealer nearest you may be obtained by calling
1-800-446-6060 (319-556-2241) or writing to:
2555 Kerper Boulevard
P.O. Box 797
Dubuque, Iowa 52001-0797
Phone: 563-556-2241 or 800-553-0039
Fax: 563-589-0516
E-mail: [email protected]
www.barnstead.com
Summary of Contents for Harvey Hydroclave MC8
Page 49: ...49 49 APPENDIX Figure 32 Power I O PC Board 230 VAC...
Page 50: ...50 50 Figure 33 MC10 Printer Power Supply Board 230 VAC APPENDIX...
Page 52: ...52 52 Figure 34 Power I O Board 115 VAC APPENDIX...
Page 53: ...53 53 APPENDIX Figure 35 MC10 Printer Power Supply Board 115 VAC...
Page 54: ...54...
Page 55: ...55...