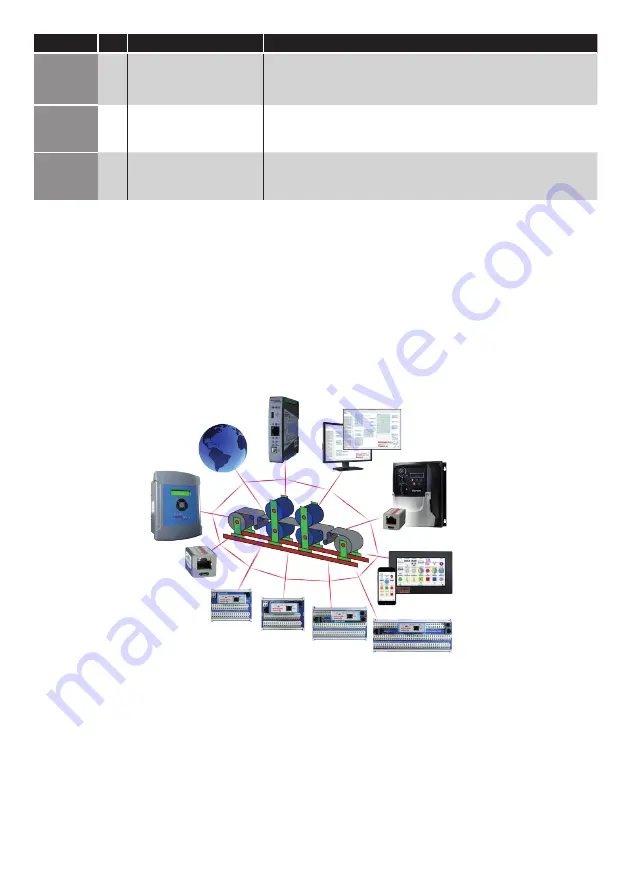
Fault Code No. Description
Suggested Remedy
41
Autotune Fault
The motor parameters measured through the autotune are not correct.
Check the motor cable and connections for continuity.
Check all three phases of the motor are present and balanced.
50
Modbus comms loss fault
Check the incoming Modbus RTU connection cable.
Check that at least one register is being polled cyclically within the timeout
limit set in P-36 Index 3.
51
CAN comms loss trip
Check the incoming CAN connection cable.
Check that cyclic communications take place within the timeout limit set in
P-36 Index 3.
NOTE
Following an over current or overload trip (1, 3, 4, 15), the drive may not be reset until the reset time delay has elapsed
to prevent damage to the drive.
drive.web
Distributed Control Technology
drive.web
Distributed Control Technology
provides high performance, peer-to-peer networking over Ethernet and
completely homogeneous systems integration for all Bardac AC and DC drive models, drive.web smart programmmable
controllers, flexible i/o, and savvyPanel industrial touch screens.
Easily build a completely integrated enterprise ... machine to management
drive.web
distributed control enables processessing resources to be shared between devices thereby ensuring cost
effective, full featured control for systems of any size or complexity. Peer-to-peer connections eliminate the constraints
imposed by a PLC in a conventionl control system.
• configure, monitor and control all your drives and devices from anywhere
• entire configurations are saved in the devices - you are not dependent on external storage or the “cloud”.
• provides full featured PAC, PLC and motion control functions on board
• add unlimited distributed smart i/o - precision analog, logic, encoders, RTDs, sensors, steppers
• build and document complete systems
• secure with multi-layer password protection and VPN access
• includes event driven email, network watchdogs, graphical state machine logic, IIoT tools, Internet access, a future.