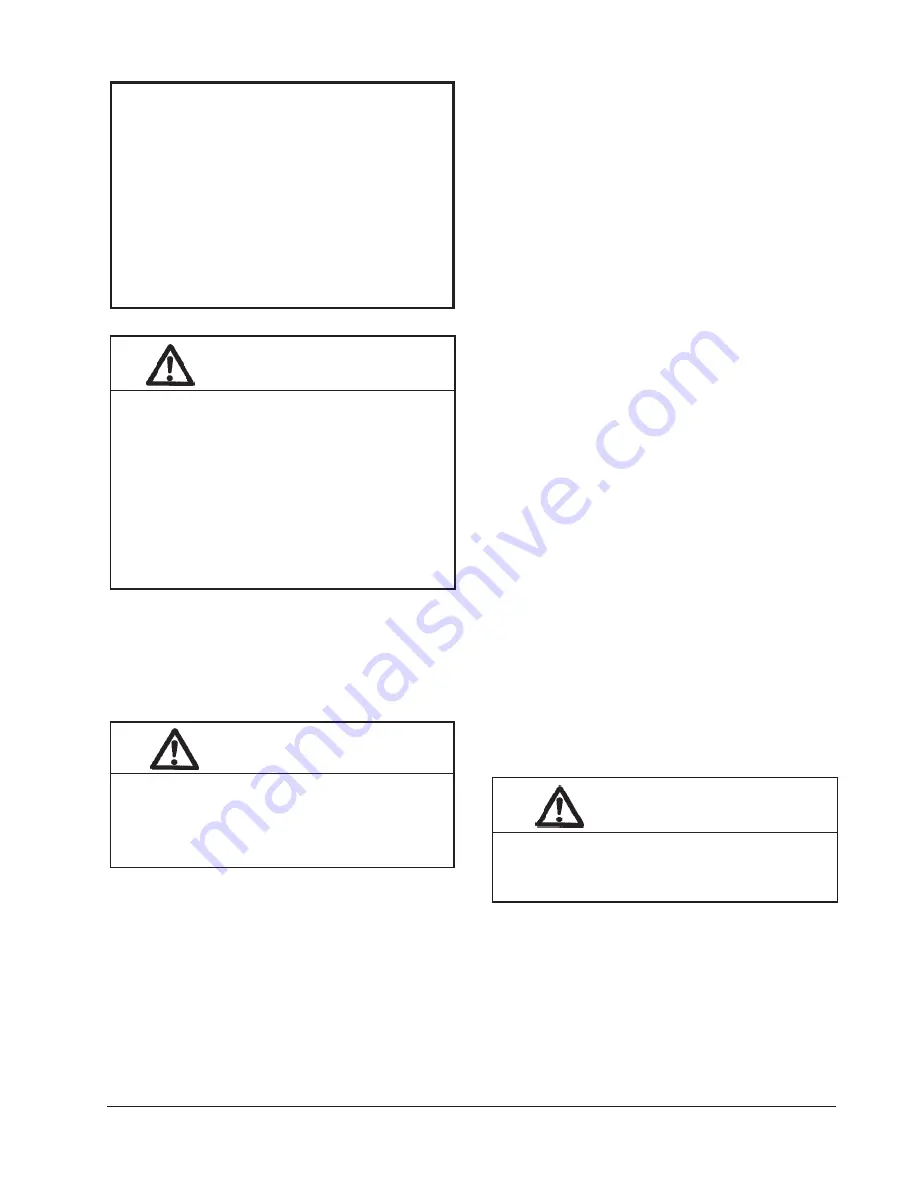
Manual 2100-486D
Page
22 of 37
18. MANIFOLD PRESSURE
ADJUSTMENT
You will need a 0 to 15 inch water manometer with 0.1
inch resolution and a 1/8" NPT manual shut off valve to
measure actual manifold pressure.
Depending on your local gas heating value and
elevation, you may need to adjust manifold pressure or
change orifices to get proper gas input rate. Check
with your local gas supplier to determine heating value
(BTU/cu. ft.) of natural gas in your area.
NOTE: If furnace is being installed at an altitude of
more than 6,000 feet above sea level, you
must derate the furnace. See Section 20
“Standard Orifice Sizing and High Altitude
Derate”.
19. CHECKING GAS INPUT RATE
It is the installer's responsibility to see that the BTU
input rate of the furnace is properly adjusted. Under-
firing could cause inadequate heat, excessive
condensation or ignition problems. Overfiring could
cause sooting, flame impingement or overheating of
heat exchanger.
1. Turn off gas at equipment shut off valve in gas
supply line just ahead of furnace.
2. Remove plug from outlet pressure tap in gas control
or gas manifold.
3. Install 1/8" NPT manual shut off valve in hole
vacated by plug. Make sure shut off valve is in off
position.
4. Attach manometer to 1/8" NPT manual shut off
valve just installed.
PROPANE (LP) GAS CONVERSION
This unit may be converted in the field for
use with Propane (LP) gas. Propane gas
conversion kit number WGCK-1 is designed
for conversions of units installed from
0 – 6,000 feet elevations. Propane gas
conversion kit number WGCK-2 is designed
for conversions of units installed from 6,001
– 10,000 feet elevations. These kits may
be purchased from your local distributor.
5. Slowly open equipment shut off valve in gas supply
line just ahead of furnace. Start furnace following
“Operating Instructions” on front door.
6. Slowly open 1/8" NPT manual shut off valve leading
to manometer.
7. Read manifold pressure on manometer.
8. Adjust manifold pressure by turning gas control
regulator adjusting screw clockwise to increase
pressure or turning counterclockwise to decrease
pressure. Manifold pressure must be within
allowable range as follows:
•
Natural gas manifold pressure must be between
3.2 and 3.8 inches W.C. Rated pressure is 3.5
inches.
•
Propane gas (LP) manifold pressure must be
between 9.7 and 10.3 inches W.C. Rated
pressure is 10 inches.
NOTE: For natural gas, if gas flow rate can't be
properly set within these pressure ranges
then you must change main burner orifices to
obtain proper gas flow rate.
9. Shut off furnace. Turn off gas at equipment shut off
valve in gas supply line just ahead of furnace. Install
outlet pressure tap plug in gas control. Turn on gas.
10. Check regulator adjustment cover screw and gas
control plug for gas leaks. Use a commercial soap
solution made for leak detection.
WARNING
Failure to adjust furnace to the proper firing
rate could cause heat exchanger failure.
WARNING
When converting from propane (LP) gas to
natural gas, the gas orifice spuds and gas
valve spring must be replaced and the gas
valve regulator pressure must be adjusted
correctly. Failure to do so can result in fire,
injury or death. Refer to Table 8 for proper
orifice sizing.
Natural gas spring kit, Part number 5603-007,
can be purchased through your local
distributor.
WARNING
Correct manifold pressure is necessary for
proper ignition and burner operation. Failure
to accurately adjust pressure could cause
heat exchanger failure.
Summary of Contents for WF0501-A
Page 13: ...Manual 2100 486D Page 13 of 37 FIGURE 6 COMMON WALL MOUNTING INSTALLATIONS...
Page 19: ...Manual 2100 486D Page 19 of 37 FIGURE 11 LOW VOLTAGE WIRING...
Page 20: ...Manual 2100 486D Page 20 of 37 FIGURE 12 GAS PIPE CONNECTION...
Page 34: ...Manual 2100 486D Page 34 of 37 230 208 60 1...
Page 35: ...Manual 2100 486D Page 35 of 37 115 60 1...