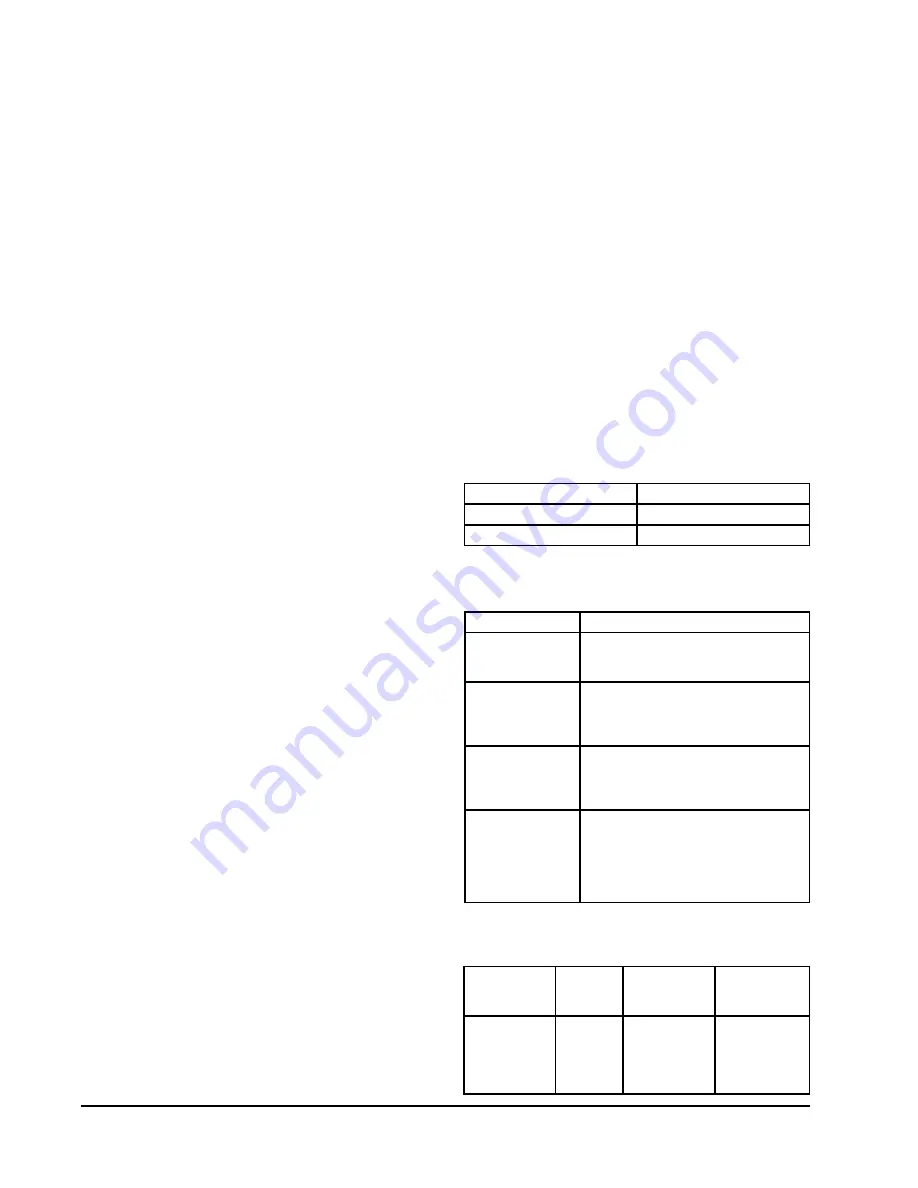
Manual 2100-628
Page
12 of 24
WIRING – MAIN POWER
Refer to the unit rating plate for wire sizing information
and maximum fuse or circuit breaker size. Each
outdoor unit is marked with a “Minimum Circuit
Ampacity”. This means that the field wiring used must
be sized to carry that amount of current. Depending
on the installed KW of electric heat, there may be
two field power circuits required. If this is the case,
the unit serial plate will so indicate. All models are
suitable only for connection with copper wire. Each
unit and/or wiring diagram will be marked “Use Copper
Conductors Only”. These instructions
must be
adhered
to. Refer to the National Electrical Code (NEC) for
complete current carrying capacity data on the various
insulation grades of wiring material. All wiring must
conform to NEC and all local codes.
The electrical data lists fuse and wire sizes (75° C
copper) for all models including the most commonly
used heater sizes. Also shown are the number of field
power circuits required for the various models with
heaters.
The unit rating plate lists a “Maximum Time Delay
Relay Fuse” or circuit breaker that is to be used with
the equipment. The correct size must be used for
proper circuit protection and also to assure that there
will be no nuisance tripping due to the momentary high
starting current of the compressor motor.
The disconnect access door on this unit may be locked
to prevent unauthorized access to the disconnect. To
convert for the locking capability, bend the tab located
in the bottom left-hand corner of the disconnect
opening under the disconnect access panel straight
out. This tab will now line up with the slot in the door.
When shut, a padlock may be placed through the hole
in the tab preventing entry.
See “Start Up” section (page 17) for important
information on three phase scroll compressor start ups.
See Table 6 on page 23 for Electrical Specifications.
WIRING – LOW VOLTAGE WIRING
All 230/208V 1 phase equipment has dual primary
voltage transformers. All equipment leaves the factory
wired on 240V tap. For 208V operation, reconnect
from 240V to 208V tap. The acceptable operating
voltage range for the 240 and 208V taps are:
TAP RANGE
240
253 – 216
208
220 – 187
NOTE: The voltage should be measured at the field
power connection point in the unit and while
the unit is operating at full load (maximum
amperage operating condition).
18 guage copper, color-coded thermostat cable is
recommended. See Figure 7 on page 14 for thermostat
connections.
Low Voltage Connection
These units use a 24-volt AC low voltage circuit.
The “
RT
” terminal is the 24V transformer output,
and the “
R
” terminal is the 24VAC
hot
terminal for
the operation of the equipment. “
RT
” and “
R
” are
connected with brass jumper bar which can be removed
and “
RT
” and “
R
” connected to external NC (normally
closed) contact such as a fire/smoke detector that will
cause immediate shutdown of the equipment upon
activation.
“
C
” terminal is
grounded
.
“
G
” terminal is the
fan input
.
“
Y
” terminal is the
compressor input for cooling
“
W1
” terminal is the
1st stage electric heat
.
TABLE 3
THERMOSTAT WIRE SIZE
Transformer
VA
FLA
Wire Gauge
Maximum
Distance
(Feet)
55
2.3
20 gauge
18 gauge
16 gauge
14 gauge
12 gauge
45
60
100
160
250
TABLE 1
LOW VOLTAGE CONNECTIONS
FOR DDC CONTROL
Fan Only
Energize G
Cooling Mode
Energize Y, G
Heating Mode
Energize W1, G
Part Number
Predominate Features
8403-057
(TH3110D1040)
1 stage Cool, 1 stage Heat
Electronic Non-Programmable
Auto or Manual changeover
8403-058
(TH5220D1151)
2 stage Cool, 2 stage Heat
Electronic Non-Programmable
HP or Conventional (Default: HP)
Auto or Manual changeover
8403-059
(TH5220D1219/U)
2 stage Cool, 2 stage Heat
Electronic Non-Programmable
HP or Conventional (Default: AC)
Auto or Manual changeover
8403-060
(1120-445)
3 stage Cool; 3 stage Heat
Programmable/Non-Programmable
Electronic
HP or Conventional
Auto or Manual changeover
Dehumidification Output
TABLE 2
WALL THERMOSTAT