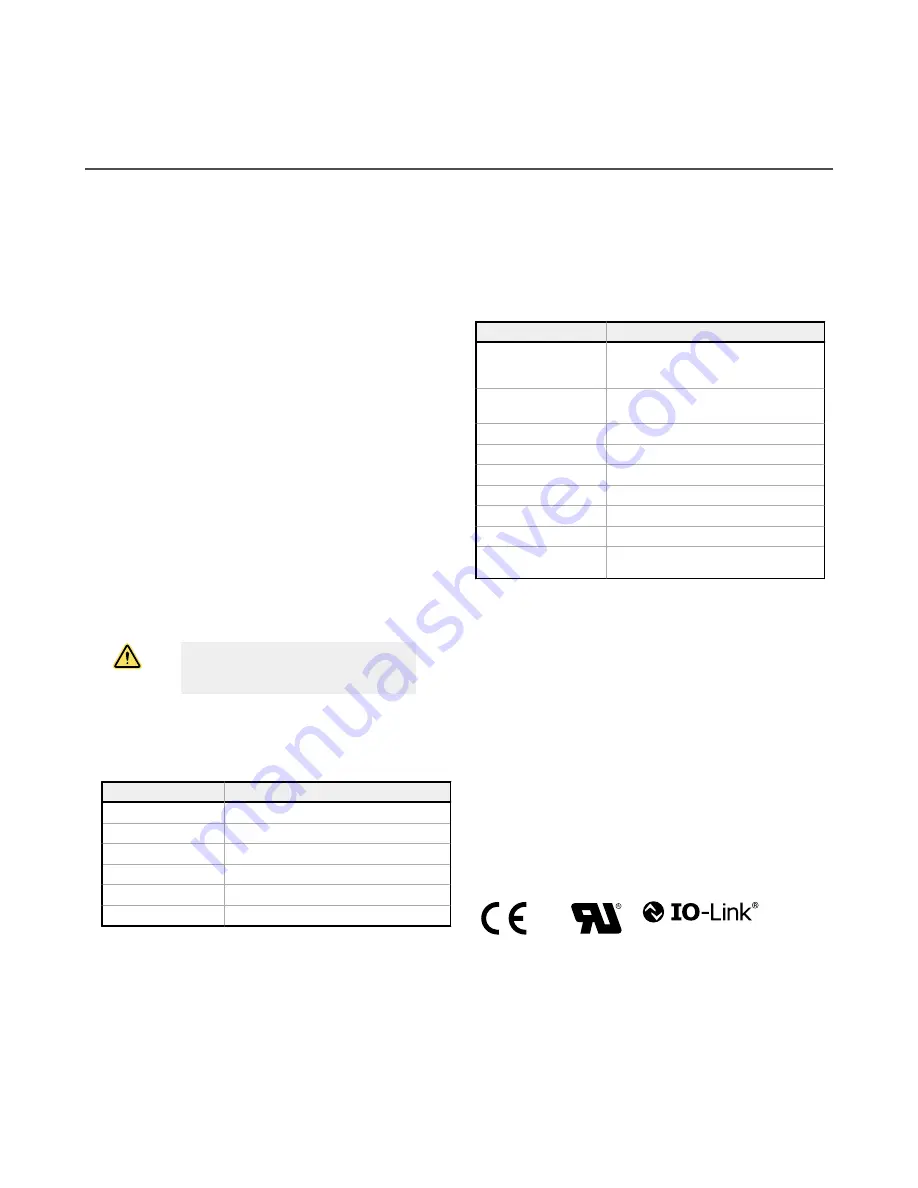
7 Specifications
7.1 Self-Contained Models: Specifications
Supply Voltage and Current
10 V dc to 30 V dc (10% maximum ripple within specified limits) at 30
mA
Supply Protection Circuitry
Protected against reverse polarity and transient overvoltages
Output Protection Circuitry
Protected against false pulse on power-up and continuous overload or
short-circuit of output
Output Configuration
Channel 1: IO-Link, Push/pull output, configurable PNP or NPN output
Channel 2: Multi-function remote input/output, configurable PNP or
NPN
Output Response Time
Momentary delay on power-up, < 0.5 s, output does not conduct during
this time
350 microseconds ON & OFF for high speed response time
1 millisecond ON & OFF for standard response time
2 millisecond ON & 1 millisecond OFF for robust response time
Repeatability
140 microseconds for high speed
175 microseconds for standard and robust
IO-Link Interface
Supports Smart Sensor Profile: Yes
Baud Rate: 38400 bps
Process Data Widths: 32 bits In, 8 bits Out
IODD Files: Provides all programming options of push button and
remote input wire, plus additional functionality. See the IO-Link Data
Reference Guide for more details.
Emitter LED
DV, CV, FP, and LP: Visible red, 625 nm
D models: Infrared, 940 nm
Indicators
Two LEDs (1 green, 1 amber)
Green On: Indicates power applied and sensor ready
Green Flashing: Indicates sensor operating in marginal state, in need of
reconfiguration
Amber On: Indicates output conducting
Factory Default Settings
Setting
Factory Default
TEACH/SET
D, DV, CV, and FP Models: Two-point Static
TEACH
LP Models: Light SET
Output Logic
D, DV, CV, and FP Models: Light Operate
LP Models: Dark Operate
Output Response Time
Standard
Offset Percentage
30%
Push Button
Unlocked
Auto Compensation
Enabled
OFF Delay
Disabled
Pin 4 Output
IO-Link Enabled Detection Output (Push-pull)
Pin 2 Output
Detection Output: High-speed output when using
IO-Link on Pin 4
Required Overcurrent Protection
WARNING: Electrical connections must be
made by qualified personnel in accordance
with local and national electrical codes and
regulations.
Overcurrent protection is required to be provided by end product
application per the supplied table.
Overcurrent protection may be provided with external fusing or via
Current Limiting, Class 2 Power Supply.
Supply wiring leads < 24 AWG shall not be spliced.
For additional product support, go to
.
Supply Wiring (AWG)
Required Overcurrent Protection (Amps)
20
5.0
22
3.0
24
2.0
26
1.0
28
0.8
30
0.5
Construction
Housing: ABS
Window: PMMA
Mounting Torque
Nose Mount: 18 mm mounting nut, 20 Ibf·in (2.3 N·m)
Side Mount: Two M3 screws, 5 Ibf·in (0.6 N·m)
Connections
PVC-jacketed 4-conductor 2 m (6.5 ft) or 9 m (30 ft) unterminated cable,
or 4-pin M12/Euro-style or 4-pin M8/Pico-style quick-disconnect, either
integral or 150 mm (6 in) cable, are available.
Models with a quick disconnect require a mating cordset
Operating Conditions
–40 °C to +70 °C (–40 °F to +158 °F)
95% at +50 °C maximum relative humidity (non-condensing)
Environmental Rating
IEC IP67
Application Notes
If the push button does not appear to be responsive, perform the push
button enable procedure
Certifications
WORLD-BEAM QS18 Expert with IO-Link
www.bannerengineering.com - Tel: + 1 888 373 6767
19