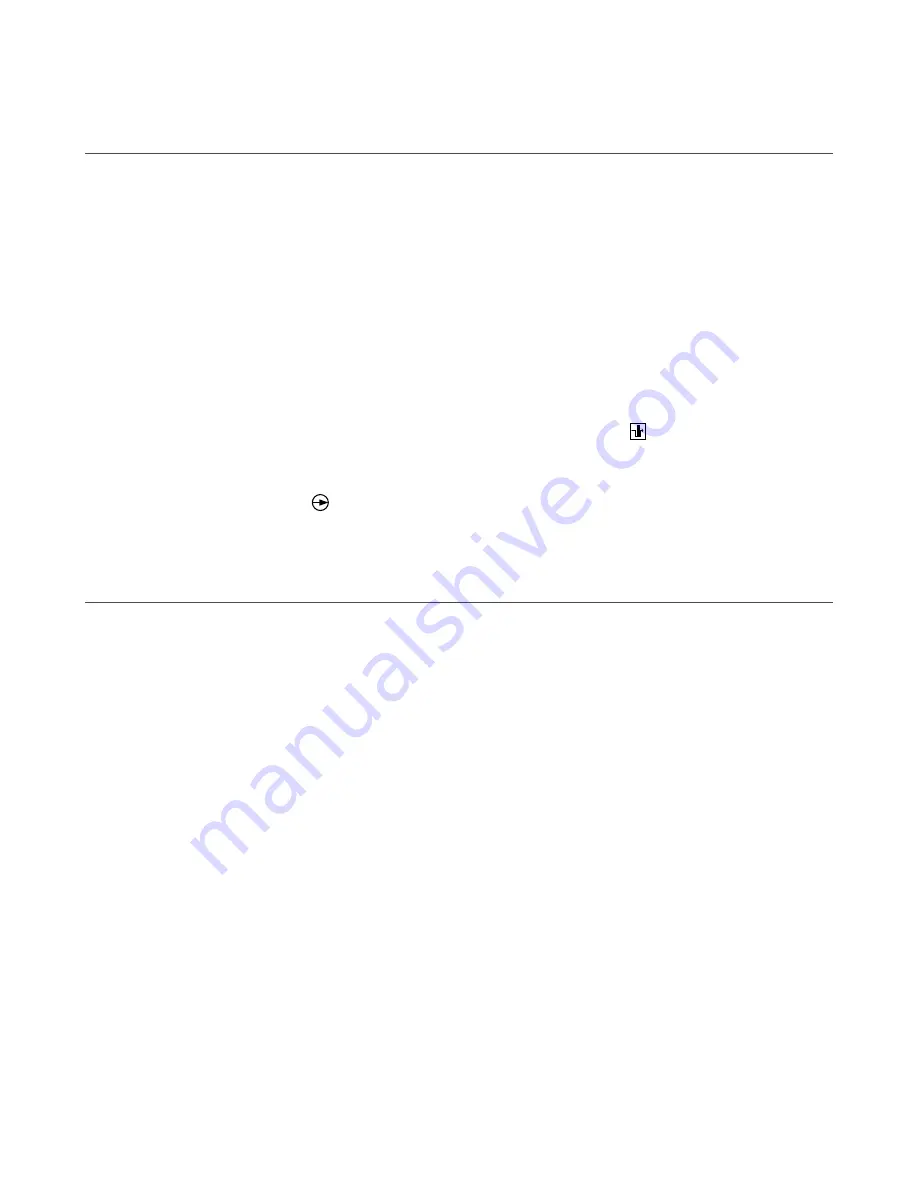
To reset the Escape Release Mechanism, turn the dial 180° counterclockwise. The unit is now ready normal operation.
2.4 Access the Wiring Chamber
1. To access the wiring chamber, loosen the top cover's four screws (centered at top, bottom, and on each side) with a
screwdriver (TX 10).
The screws are captive screws and should not come all the way out of the cover.
2. Select the best wiring entrance and, if required, thread in the ½" x 14 NPT conduit adapter (SI-QS-M20, ordered
separately) or an M20 × 1.5 cable gland (SI-QS-CGM20, ordered separately). For more information, see
on p. 20.
3. Tighten the conduit adapter or cable gland to 6 N·m.
The switch knockout breaks loose with the final turns of the conduit adapter or cable gland.
2.4.1 Wiring the Terminals
The electrical contacts of the switching elements have screw connections. Use a flathead screwdriver to loosen and tighten
the terminals.
See
on p. 3 for contact assignments. The connections require a stranded flexible wire with ferrule having a cross
section of 0.34 mm
2
to 1.5 mm
2
. Strip length should be between 6 mm and 7 mm. Tighten the screws to 0.8 N·m.
When using the locking mechanism for personal protection, use the contacts marked with
. Because the locking element
can only go to the engaged position if the actuator is present, this contact signifies the closed position and the locking
status of the guard so it can be checked by the monitoring device of the safety circuit (per ISO 14119).
When using the locking mechanism for process control purposes (only the fact that the door is closed is used for personnel
safety), the contacts marked with the
symbol can be used, which signals the status of the actuator (present or not).
For units with pre-installed M12 quick disconnect connections, please refer to the corresponding model addendum for pin
assignments.
2.5 Connection to a Machine
Perform a risk assessment to determine the means of interfacing the switch(es) with the machine control circuit. Although
Banner Engineering always recommends the highest level of safety in any application, it is the responsibility of the user to
safely install, operator and maintain each safety system and comply with all relevant laws and regulations.
To ensure the highest level of reliability (e.g. Control Reliable or Category 4/PL e), we recommend wiring the safety contacts
from two safety switches per interlocked guard in a dual-channel connection to a safety module, safety controller, or other
safety related parts of the control system (see
on p. 20 for a list of safety evaluation devices from Banner
Engineering) that comply with the required level of safety performance as shown.
SI-GL42 Series Locking-Style Safety Interlock Switch
www.bannerengineering.com - Tel: + 1 888 373 6767
13