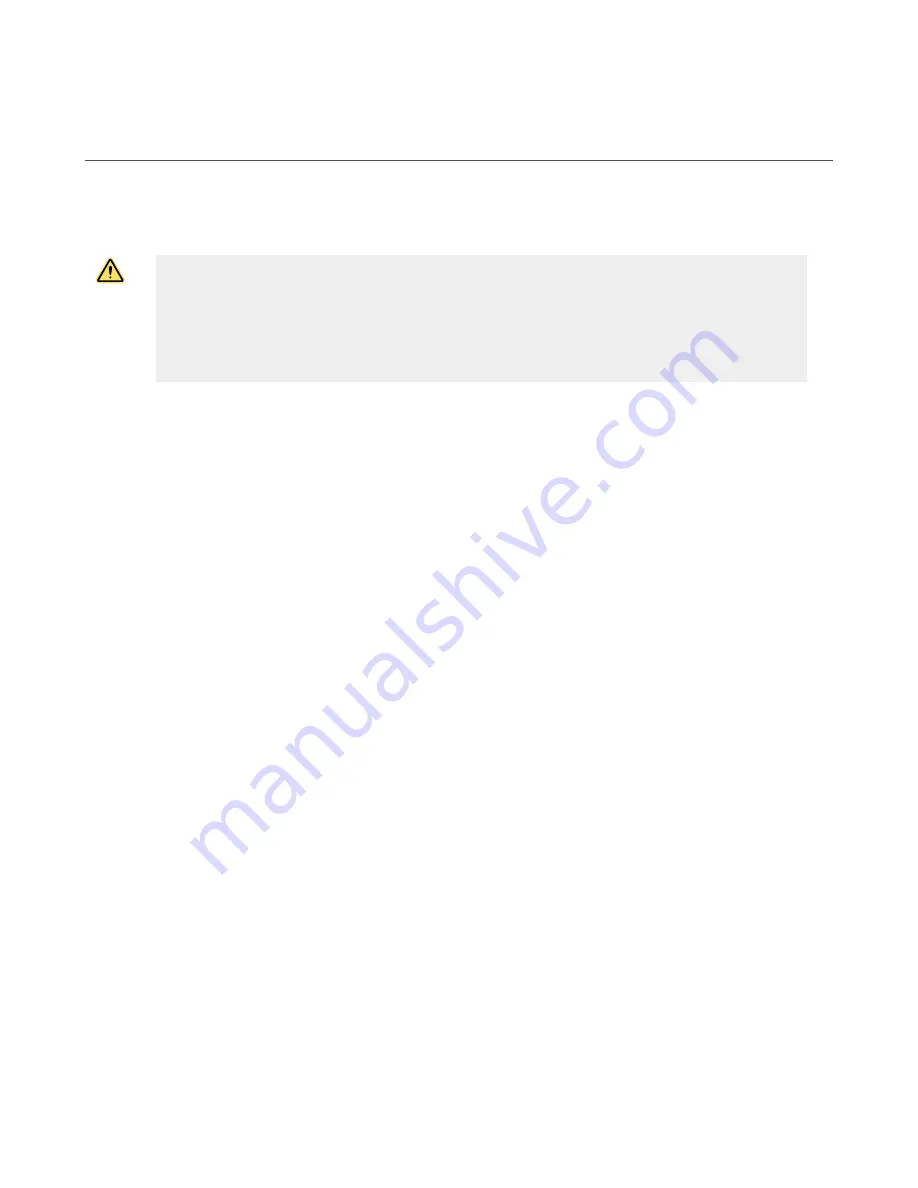
3 Operating Instructions
3.1 Checkout Procedures
Banner Engineering highly recommends performing the checkouts as described. However, a qualified person (or team)
should evaluate these generic recommendations considering their specific application and determine the appropriate
frequency of checkouts. This will generally be determined by a risk assessment, such as the one contained in ANSI B11.0.
The result of the risk assessment will drive the frequency and content of the periodic checkout procedures and must be
followed.
WARNING:
• Test multiple safety devices individually
• Failure to test each safety device individually could result in undetected faults and create an
unsafe condition that could result in serious injury or death.
• When two or more safety devices are used, individually actuate each device, causing a stop or
open-contact condition, then reset/rearm the safety module (if using manual reset mode). This
allows the monitoring circuits to check each device and its wiring to detect faults.
3.1.1 Initial and Daily Checks
Verify the functioning of the safety switch(es) and the interlocked guard (if applicable) at designated periods. Verify at initial
installation by a
qualified person
, verify daily or before each use by a
designated person
, and as part of the regular periodic
checkout procedure listed below to ensure proper operation.
A
qualified person
possesses a recognized degree or certificate or has extensive knowledge, training, and experience to be
able to solve problems relating to the safety switch installation. A
designated person
is identified in writing by the employer
as being appropriately trained to perform a specified checkout procedure.
1. Inspect for breakage of the switch body or actuator
2. Verify good alignment and full engagement of the actuator
3. Confirmation that the safety switch is not being used as an end stop
4. Inspect for loosening, corrosion, or damage to the mounting hardware of the switch body and actuator
5. Verify that it is not possible to reach any hazard point through an opened guard (or any opening) before hazardous
machine motion has completely stopped
6. Verify switch(es) operation per specific application. For example, the machine cycle stops and/or can not be initiated
when the actuator is removed from the switch body.
7. If more than one safety switch(es) and the interlocked guard is used, perform this procedure individually for EACH
device.
3.1.2 Periodic Checks
A
qualified person
(as defined above) should check for the following on a periodic schedule determined by the user, based
upon the severity of the operating environment and the frequency of switch actuations. At a minimum, this should take
place once a year (lockout/tagout procedures for controlling hazardous energy may be required):
1. Inspect the wiring chamber for signs of contamination, deterioration, loose connections, or damage
2. Inspect the sealing at the cable entry and all electrical wiring for continuity and damage
3. Verify that wiring and installation conforms to the instructions in this document and that there are no signs of
tampering or defeat
4. Perform the initial/daily checkout listed above
See also the machine manufacturer's recommendations for additional instructions. If any of these checks cannot be
verified, do not attempt to use the machine until the defect or problem has been corrected.
SI-GL42 Series Locking-Style Safety Interlock Switch
16
www.bannerengineering.com - Tel: + 1 888 373 6767