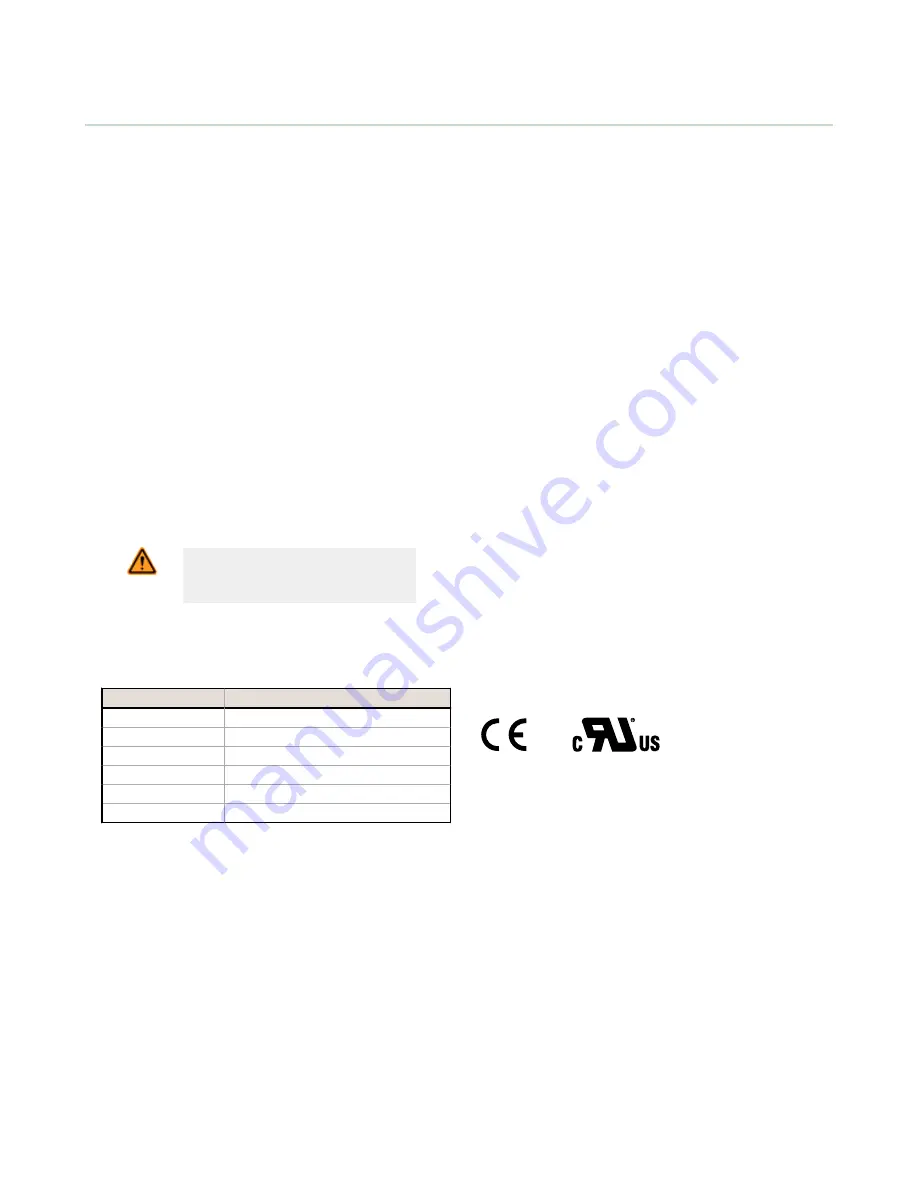
Specifications
Sensing Beam
Standard sensors: 660 nm visible red or 525 nm visible green,
depending on model
Models with bussable power: 660 nm visible red
Supply Voltage
Standard sensors: 10 to 30 V dc (10% maximum ripple) at less than
45 mA exclusive of load
Models with bussable power: 12 to 30 V dc (10% maximum ripple) at
less than 45 mA exclusive of load
Supply Protection Circuitry
Protected against reverse polarity, over voltage, and transient voltage
Delay at Power Up
Standard Sensors: 200 milliseconds maximum; outputs do not conduct
during this time
Models with Bussable Power: 850 milliseconds maximum; outputs do
not conduct during this time
Output Rating (Standard Sensors)
Standard Sensors: 150 mA maximum load at 25° C (derate 1 mA per
°C increase)
OFF-state leakage current: < 5
μ
A at 30 V dc
ON-state saturation voltage: NPN: < 200 mV at 10 mA; 1 V at 150 mA
load; PNP: < 1 V at 10 mA; 1.5 V at 150 mA load
Output Rating (Models with Bussable Power)
Models with Bussable Power: 100 mA maximum load (derate 1 mA per
°C above 30 °C)
OFF-state leakage current: < 5
μ
A at 30 V dc
ON-state saturation voltage: NPN: < 1.5 V; PNP: < 2 V
Supply 15 V or more: up to 16 units with 100 mA outputs
Less than 15 V supply (9 m cable): up to 4 units with 100 mA outputs;
up to 8 units with 50 mA outputs
Required Overcurrent Protection
WARNING: Electrical connections must be
made by qualified personnel in accordance
with local and national electrical codes and
regulations.
Overcurrent protection is required to be provided by end product
application per the supplied table.
Overcurrent protection may be provided with external fusing or via
Current Limiting, Class 2 Power Supply.
Supply wiring leads < 24 AWG shall not be spliced.
For additional product support, go to
.
Supply Wiring (AWG)
Required Overcurrent Protection (Amps)
20
5.0
22
3.0
24
2.0
26
1.0
28
0.8
30
0.5
Output Protection
Protected against output short-circuit, continuous overload, transient
over-voltages, and false pulse on power-up
Output Response Time
500 microseconds (normal mode) or 200 microseconds (high-speed
mode)
Repeatability
100 microseconds (normal mode) or 66 microseconds (high-speed
mode)
Adjustments
2 push buttons and remote wire
•
Expert-style configuration (Static and Dynamic TEACH, and
Window Set)
•
Manually adjust (+/–) sensitivity (from push buttons only)
•
LO/DO, OFF-delay, and response speed configurable (from
push buttons or remote wire)
•
Push button lockout (from remote wire only)
Factory Default Settings: Light Operate, Normal Speed, No Delay
Push-button or remote programming of response time, OFF-delay,
light/dark operate, and display
Indicators
8-segment red bar graph: Light-to-dark signal difference relative to
taught condition (Window Set); Sensing contrast (Static or Dynamic
TEACH)
Green Status Indicators: LO, DO, High Speed (HS), and OFF-Delay
Green LED: Power ON
Yellow LED: Output conducting
Construction
Black ABS/polycarbonate alloy (UL94 V-0 rated) housing, clear
polycarbonate cover
Environmental Rating
IEC IP50, NEMA 1
Connections
Standard Sensors: PVC-jacketed 2 m or 9 m (6.5 ft or 30 ft) 6-wire
integral cable or integral 6-pin Pico-style quick-disconnect
Models with Bussable Power: Main units: PVC-jacketed 2 m or 9 m
(6.5 ft or 30 ft) 5-wire integral cable; Sub-units: PVC-jacketed 2 m or
9 m (6.5 ft or 30 ft) 2-wire integral cable
Operating Conditions
Temperature:
−
10 °C to +55 °C (+14 °F to +131 °F)
Storage Temperature:
−
20 °C to +85 °C (
−
4 °F to +185 °F)
90% at +55 °C maximum relative humidity (non-condensing)
Certifications
D10 Expert
™
Series with Bar Graph Display and Discrete Output
10
www.bannerengineering.com - Tel: +1-763-544-3164
P/N 117830 Rev. G