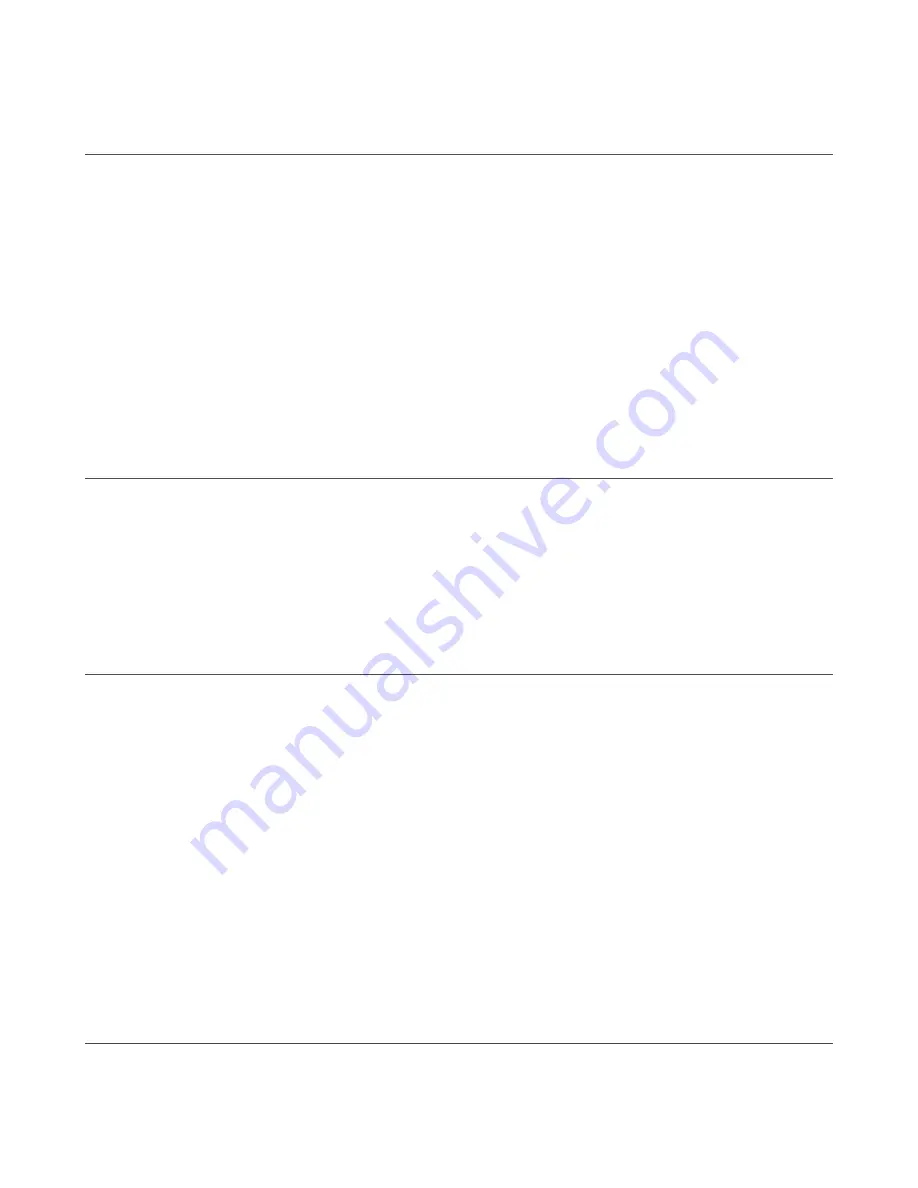
5
Configuration
Instructions
5.1 Install the
Software
The Parameter Setup
Software
CD includes an
installation
program that quickly and easily loads the MINI-ARRAY
configuration
program
into the computer. The MINI-ARRAY
configuration
program requires approximately 50 MB of hard disk space. Install as follows:
1. Use the Parameter Setup
Software
CD included with the controller, or download (
) per the
following:
• For models MAC-1, MACI-1, MACN-1, MACP-1, and MACV-1, use CD P/N 75877
• For models MAC16N-1 and MAC16P-1, use CD P/N 75878
2. Insert the
Software
CD into the CD drive.
• If the program does not auto-start, browse to your CD drive, click Setup.exe, then select START, then select RUN. The
Welcome dialog box appears. Select Next, and follow the prompts in the dialog boxes as they appear.
• If the program does auto-start, the Welcome dialog box appears. Select Next, and follow the prompts in the dialog boxes as
they appear.
3. The
installation
program decompresses the
files.
A status dialog box monitors the progress of the
installation.
4. An
Installation
Completed dialog box appears. Select OK. Reboot your computer for the changes to take
effect.
After
the
software
is installed, a MINI-ARRAY shortcut icon is placed on your desktop. Double-click on the MINI-ARRAY icon to
launch the program, then follow the
configuration
instructions.
5.2
Define
the
Communication
The MINI-ARRAY
software
permits serial
communication
via RS-232 between the MAC controller and the PC. The minimum
connections
to the DB-9 connector on the MINI-ARRAY Controllers are listed in
on page 15. DO NOT use a “null
modem” RS-232 cable.
To
configure
the COM port of the PC, follow these steps.
1. Select the
Options
> Serial Port menu.
The program supports serial
communication
via the COM1-COM2 port of the computer.
2. Select either COM1 or COM2.
3. Check Save
Settings
on Exit (if it is not already checked) to store the COM port
selection.
5.3 Alignment
Alignment status is
continuously
displayed by the green LED indicator on the Receiver and the controller.
When all unblanked beams are clear, and excess gain of all beams is more than 3×, the green alignment indicators are ON.
When the excess gain of one or more beams drops to between 3× and 1×, the green ALIGN LED on the controller remains ON, but the
yellow LED on the receiver comes ON to indicate a marginal alignment warning.
The MINI-ARRAY
software
can display the status of each beam in the array. This is helpful for
final
alignment or when analyzing how the
MINI-ARRAY is viewing objects in the sensing array. To use these feature, go to the Mini-Array > Alignment menu or press the F3 key.
The Alignment screen
identifies
the
location
of the
first
and last beams made (clear) and broken (blocked), plus the total number of
beams made and broken. The beams are numbered in sequence from the cable end of the sensors to the top end. This is valuable
during setup, for analyzing exactly what is being seen by the light screen. (The
Diagnostics
screen indicates any problems with the
emitter
or the receiver.)
Models MAC-1, MACP-1, MACN-1, MACV-1, and MACI-1—To display current
information,
select the desired Channel Status
Option
(Broken, Made or Both) and select Run. The chart on the right side of the screen shows the status (broken or made) of each beam in the
array. Beam status is
continuously
updated to allow accurate
positioning
of the array, and/or analysis of sensing response.
To exit the Alignment screen,
first
select Stop, then select Exit.
Models MAC16P-1 and MAC16N-1—The Alignment screen displays the status of each beam along the
entire
length of the light screen.
The
information
displayed includes the total number of
optical
channels (labeled as Beams), the number of blocked, made, and blanked
beams. Each channel state is indicated as either 1-made, 0-blocked, or B-blanked. Other alignment
functions
allow the user to scan on a
step command and to adjust the blanking
fields.
Each channel can be individually blanked. When a channel is blanked, the controller
ignores the state of the channel and does not consider the channel when
calculating
measurement mode data.
5.4 Parameter Setup Files (PSFs)
The input and output response of the MAC controller is programmed using the PSF
Configuration
screen. To access the PSF
Configuration
screen, go to Edit PSF under the Main menu or press the F4 key.
A-GAGE
®
MINI-ARRAY
®
Measuring Light Screen System
16
www.bannerengineering.com - Tel: 763.544.3164