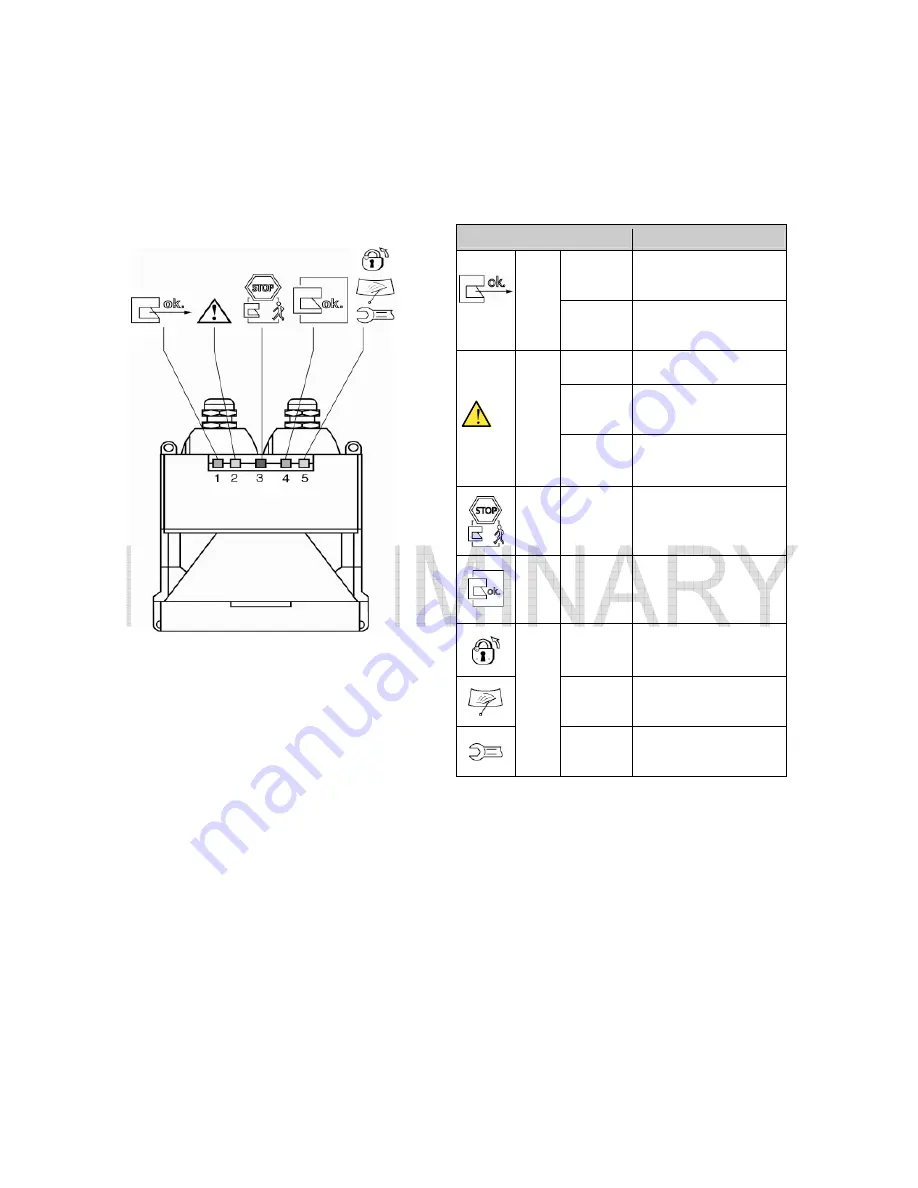
Banner AG4 Series Safety Laser Scanner
8
P/N 144924 05/2009
Product Manual
1.1
Status Display
Five LEDs on the housing front show the Scanner's operating status.
LED Diagnostic Key
LED
Meaning
ON
Sensor function is active; the
active PF is clear.
1, green
Flashes @
2 Hz
Fault on the field pair control
inputs.
ON
Active WF is selected.
Flashes @
2 Hz
Front screen is dirty.
2, yellow
Flashes @
4 Hz
ConfigPlug configuration is not
compatible with the Scanner
.
3, red
ON
Safety outputs or switching
function (OSSD 1 and 2) are
switched off.
4, green ON
Safety outputs or switching
function (OSSD 1 and 2) are
switched on.
ON
Start/restart interlock is active.
Flashes @
2 Hz
Front screen is dirty.
5, yellow
Flashes @
4 Hz
Fault
Figure 3. Status LEDs
1.2
Mounting System (Optional)
The mounting system makes it easier to install and align the Scanner. The mounting system is available as an accessory (see Section 2).
1.3
ConfigPlug (Optional)
The ConfigPlug, included as part of some control cables, is an optional accessory used to store the Scanner configuration and transfer it to
another Scanner. This accessory simplifies the exchanging of a faulting or damaged Scanner. The plug saves the configuration when the PC
transfers the operational parameters to the Scanner. When the original Scanner is replaced and connected to power with the ConfigPlug, the
plug automatically transfers the configuration into the new Scanner.