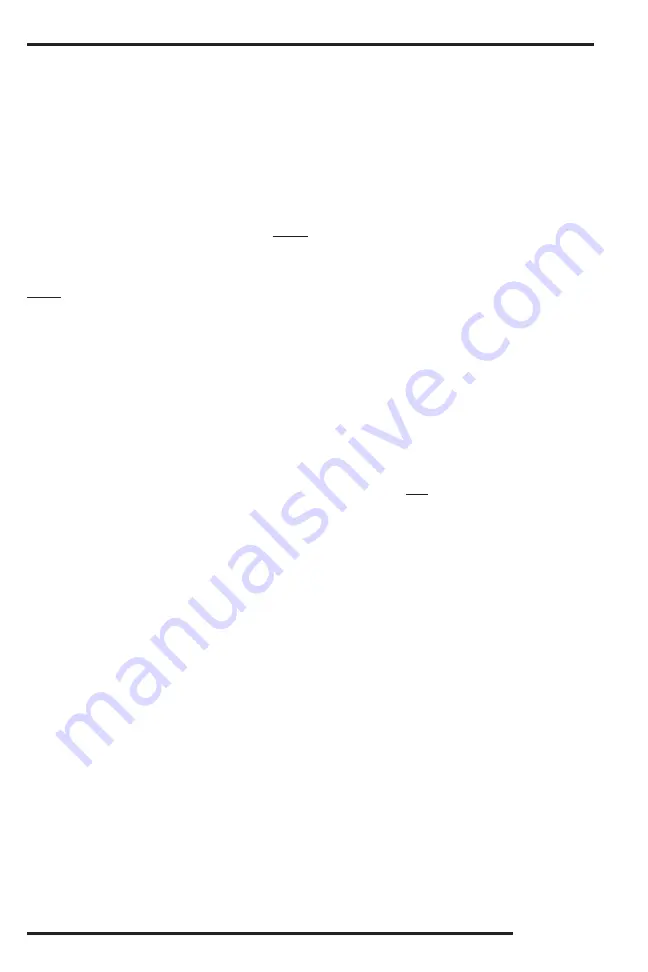
Bandit
54
Copyright 1/18
MODEL 19XPC
1. Engine:
Follow original equipment manufacturer’s requirements for both changing oils and filters, refer to engine
manual specifications.
2. Engine Coolant:
Refer to engine manufacturer’s manual specifications.
3.
Clutch:
Follow original equipment manufacturer’s requirements for both greasing and adjusting. Frequently,
adjust and lubricate per PTO manufacturer’s manual.
4.
Wheel Bearings:
Follow axle manufacturer’s instructions for greasing or oiling wheel bearings.
5.
Tracks (if equipped):
Follow track manufacturer’s instructions for specific track lubricating procedures.
6.
Hydraulic Reservoir Tank:
Completely change hydraulic oil, suction screen(s), and flush the tank
annually. Change hydraulic oil filter(s) AFTER
FIRST 10 HOURS OF OPERATION. Then change hydraulic
oil filter(s) every 3 months or 400 hours thereafter. Maintain hydraulic oil level 3/4 to 7/8 full. See hydraulic
oil requirements below. Check hydraulic oil level in tank daily.
7. High Pressure Filter(s) (if equipped):
If machine is equipped, change high pressure oil filter(s) AFTER
FIRST
10 HOURS OF OPERATION. Then change high pressure oil filter(s) every 3 months or 400 hours
thereafter.
8. Hydraulic Fluid Requirements:
See pages 76 ‑ 77 for hydraulic fluid requirements.
9.
Discharge Swivel:
Grease swivel plates for discharge every 3 months or as needed.
10. Hood Hinge:
Make sure the hood hinge operates correctly, and is lubricated daily. Must replace hinge if
damaged.
11. Steel Friction Areas:
Lubricate all steel friction areas including, but not limited to pivoting, hinged, sliding,
and rotating areas weekly. (i.e. control handle, folding tray, discharge flipper, hyd. valve linkages, height
adjustable discharge, discharge T-handle, hydraulic bump bar, etc.).
12. Pintle Eye Ring:
Keep greased monthly to reduce wear and extend the normal life of your pintle eye ring.
13.
Chain Operated Components:
Use a dry lubricant on any chain driven component weekly. (i.e. hydraulic
swivel discharge, chain driven feedwheels, etc)
14.
Chipper & Feedwheel Bearings:
Use an EP-2 Lithium type grease only for all bearings. Purge chipper
bearings with grease, you can not over grease these bearings. Grease feedwheel bearings daily with one
shot of grease. Both types of bearings are designed with a relief system that will not allow over greasing. In
other words, you can not hurt the bearing seals by pumping in too much grease. Wipe off excess grease.
Excessive grease will attract dirt.
Most of the failures related to bearings are diagnosed as “Contamination”. Contamination is caused by improper
lubrication.
Especially important is proper lubrication when the chipper is setting idle. The bearings must
be fully purged when shut down. Then the bearings must be again fully purged each thirty (30) days
and the machine allowed to run for approximately 10 minutes. Then fully purged again before the
machine is put back into operation. Failure to do this will ruin the bearings. Bearings corrode when
the machine is setting idle.
The second largest cause of bearing failure is operating them at high speeds when the grease is cold.
This causes the bearing race to turn on the shaft. Naturally this ruins the bearing as well as the shaft. Allow
the bearings to turn at slower speeds for at least five minutes. Also check the bearing lock collar set screws
or bearing locknut for tightness each 30 days. Loose set screws or locknut allows the race to turn on the
shaft. Failed bearings diagnosed as contamination or cold starts at high speed are not covered by warranty
of the bearing manufacturer.
15. Feedwheel Slide Box:
Check that feedwheel slide box is working smoothly, oil with 10W/30 type motor
oil daily. Clean and oil the slide guides. After pinning, chaining, and blocking the top yoke in the up position,
clean and oil each side of the bottom yoke. Especially new machines need oiling to ensure correct operation
during brea k - in.
16.
“Bandit Lever Throttle Cable (if equipped):
If the machine is equipped with a “Bandit” lever throttle
system, lubricate inner throttle cable and cable ends with a cable lube or SAE 10W/30 oil every month.
Replace throttle cable if it doesn’t operate smoothly.
MAINTENANCE
LUBRICATION & COOLANT
Summary of Contents for INTIMIDATOR 19XPC
Page 19: ......
Page 37: ...Bandit 23 Copyright 1 18 MODEL 19XPC DECALS ...
Page 38: ...Bandit 24 Copyright 1 18 MODEL 19XPC DECALS ...
Page 142: ...Bandit 128 Copyright 1 18 MODEL 19XPC SERVICE RECORD SERVICERECORD DATE DESCRIPTION AMOUNT ...
Page 167: ...BANDIT CONTROLS 25 245774458290 21Dec2016 Document notes 21Dec2016 First Draft ...