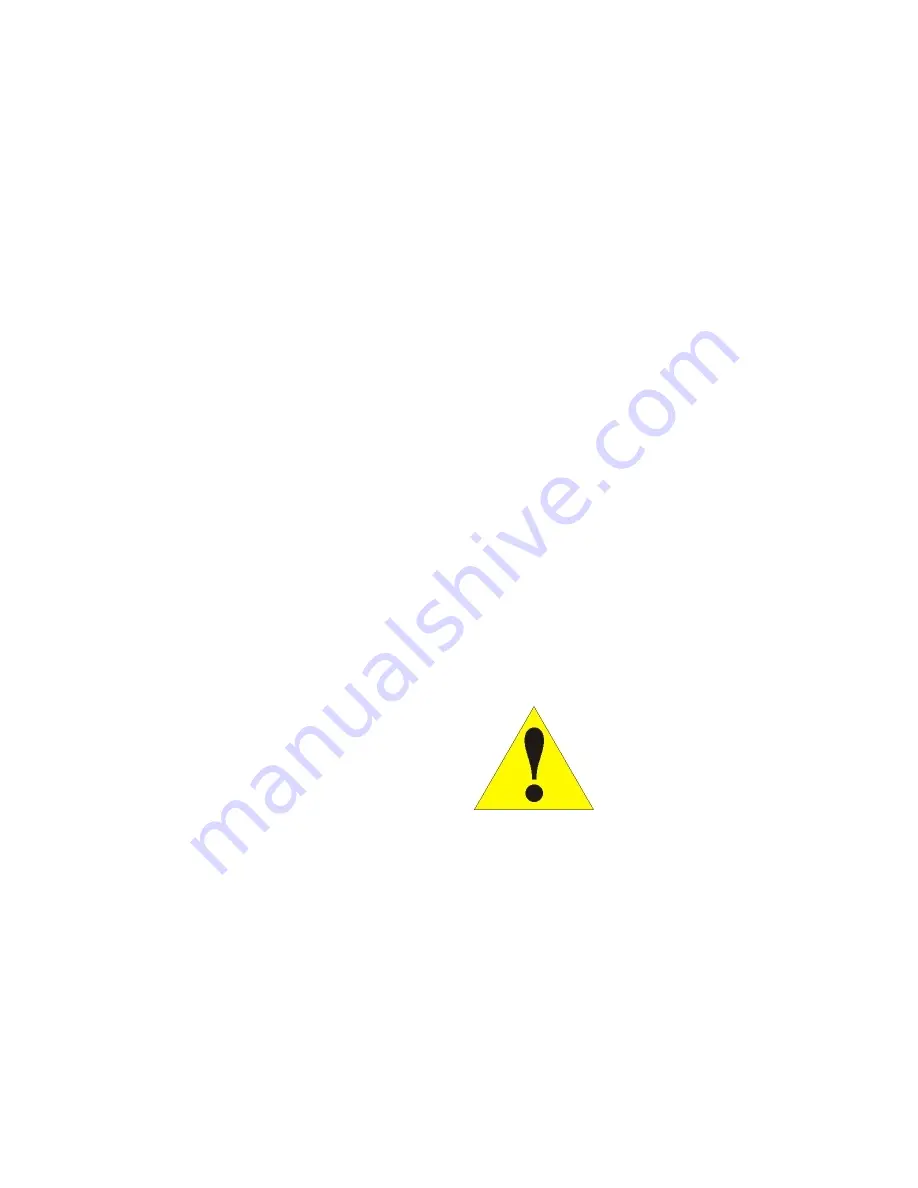
Introduction
Safety Checklist
8
Safe Operation Environment
Safe operation requires an appropriate
operating environment for both the
operator and the machine. If questions
regarding safety arise, contact the factory.
Environmental Conditions
1.
Ambient temperature.
Water in the
machine will freeze at temperatures of 32F
(0C) or below. Temperatures above 120 F
(50C) will result in more frequent motor
overheating and, in some cases,
malfunction or premature damage to solid
state devices that are used in the machines.
Special cooling devices may be
necessary.
2. Humidity.
Relative humidity above 90%
may cause the machine’s electronics or
motors to malfunction or may trip the
ground fault interrupter. Corrosion
problems may occur on some metal
components. If the relative humidity is
below 30% belts and rubber hoses may
eventually develop dry rot. This condition
can result in hose leaks, which may cause
hazards external to the machine in
conjunction with adjacent electrical
equipment.
3. Ventilation.
The need for make-up air
openings for such laundry room
accessories as dryers , ironers, water
heaters, etc. must be evaluated
periodically. Louvers, screens, or other
separating devices may reduce the
available air opening significantly..
4. Radio Frequency Emissions.
A filter is
available for machines in installations
where floor space is shared with equipment
sensitive to radio frequency emissions. All
machines that are shipped to CE countries
are equipped with this filter and comply
with the EMI regulations.
5. Elevation.
If the machine is to be
operated at elevations over 3280 feet
(1000 meter) above sea level, pay special
attention to water levels and electronic
settings ( particularly temperature) or
desired result may not be achieved.
6. Chemicals.
Keep stainless steel surfaces
free of chemical residues to avoid corrosion.
7. Water damage.
Do not spray the
machine with water. Short circuiting and
serious damage may result. Repair
immediately all seepage due to faulty
gaskets, etc.
Do not place volatile or
flammable fluids in any
machine. Do not clean the
machine with volatile or
flammable fluids such as
acetone, lacquer thinners,
enamel reducers, carbon
tetrachloride, gasoline, benzene, naphtha,
etc. Doing so could result in serious
personal injury and/or damage to the
machine
.
Machine Location
1. Foundation.
The concrete floor must be
of sufficient strength and thickness to
handle the floor loads generated by the
machine at high extract speeds.
Summary of Contents for HP series
Page 2: ......
Page 19: ...Front of Machine 18 Installation Foundation Bolt Location Typical Grouting Pattern 5 each side...
Page 38: ......