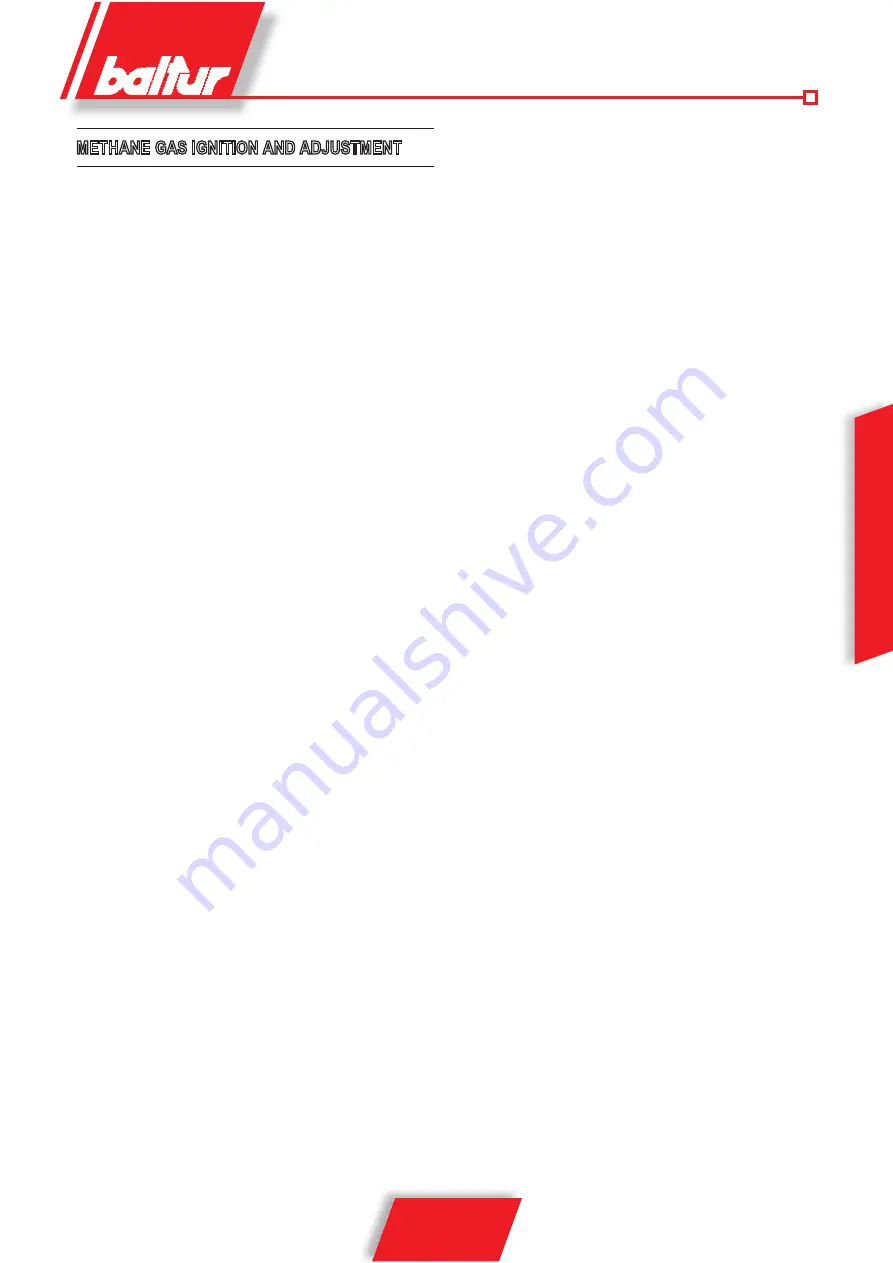
E
N
G
L
I
S
H
12 / 18
000608.1041_201102
METHANE GAS IGNITION AND ADJUSTMENT
NOTE: The burner has a switch to pass manually from the
1st to the 2nd stage.
1) Check that there is water in the boiler and that the gate
valves for the system are open.
2) Check, with complete certainty, that the discharge of
combustion products can take place freely (boiler and flue
gates open).
3) Check that the voltage in the power
supply to be connected corresponds with that required by
the burner and that the electrical connections (motor and
main line) are set up for the available voltages. Check that
all the electrical conection
is carried out on site are correct and in accordance with our
wiring diagram. Avoid working with the second flame: po
-
sition the 1st and 2nd stage switch on the printed circuit in
the 1st stage position for burners TBG 150 P-210P; for the
burner TBG 55 disconnect the wire powering coil Y2 from
terminal 5 of the a terminal board on the printed circuit.
4) Adjust air to the ignition flame: for burners TBG 55 P-
210P, with electric motor electric, following the nstructions
in the technical specifications in the following pages; in the
case of burner TBG 55 with manual adjustment, adjust the
air to the second flame following the instructions on page
41.
5) Carefully manoeuvre the gas adjustment device valve to
open, for the amount presumed necessary, the first flame
flow adjuster (see the instructions for the two-stage gas
alve for the model installed on the burner). If necessary, of
course, open the safety valve flow adjuster completely if
there is one.
6) With the switch on the burner panel at the position “0”
and the main switch on, check, closing
the contactor manually, that the motor rotates in the right
direction, if necessary swap the two power cables for the
motor around to change the direction of rotation.
7) Now switch on the cotrol panelswitch (see page.15). The
control equipment thus receives voltage and the program
-
mer causes the burner to switch on as described in the
chapter “description of working”. During the preventilation
stage you must check that the air pressure control switch
carried out the exchange (from the closed position without
pressure detection it must go to the closed position detec
-
ting air pressure). If the air pressure switch does not detect
sufficient pressure (does not carry out the exchange) the
ignition transformer is not switched on, nor are the gas val
-
ves, and so the equipment is stopped in its “look-out” mode.
On first switching on repeated “lock outs” may occur due to:
a) the gas piping not being freed of the air sufficiently and
so the gas quantity is not enough to provide a stable flame.
b) “lock out” with flame present maybe caused by insta
-
bility
in the ionisation area, due to an incorrect air/gas ratio. This
can be remedied by varying the quantity of air and/or gas
until the right ratio is found.
The same problem may be caused by incorrect air/gas
distribution in the combustion head. This can be remedied
with the combustion head adjustment device by closing or
opening further the air passage between combustion head
and gas diffusor.
c) It may happen that the ionisation current is interfered
with by the discharge current of the ignition transformer (the
two currents have a common path on the burner’s “mass”)
so the burner gets locked out due to insufficient ionisation
This can be remedied by inverting the supply (230V side)
of the ignition transformer (swapping the two wires carrying
voltage to the transformer). This problem may also be cau
-
sed by an insufficient “ground connection” from the burner’s
casing.
8) With the burner on at minimum you must carry out an
immediate visual check on the extent of and appearance
of the flame, performing the necessary corrections with
the gas and air supply regulators (see points 4 and 5).
Subsequently a check is carried out on the quantity of gas
supplied, by reading the meter. If necessary the gas supply
and the corresponding combustion air can be corrected as
previously described (points 4 and 5). Subsequently the
combustion is checked with the special instruments.
For a correct air/gas ratio you must find a carbon dioxide
(CO
2
) value for the methane that is at least 8 % or O
2
= 6%
at minimum burner supply up to an optimal value of 10 %
or O
2
= 3% for maximum supply.
It is essential to check, with a suitable instrument, that the
percentage of carbon monoxide (CO) present in the fumes
does not exceed the limit set by regulations at the time of
installation.”
9) Carry out repeated checks that the first flame supply
is correct after adjusting the working with the first flame,
switch off the burner, open the master switch and close the
electric circuit that controls the switch on of the second fla
-
me: turn the 1st and 2nd stage switch on the printed circuit
to the 2nd stage position for the burners TBG 150 P-150P;
for the burner TBG 55 reconnect the wire powering the coil
Y2 to terminal 5 of the terminal board on the printed circuit.
10) Open the manual regulator for the gas supply for the
second flame (main flame) to the presumed necessary
quantity.
11) Now switch the burner on again, closing the master
switch and that on the control panel. The burner switches
on and automatically switches on the second flame (main
flame). Carry out an immediate visual check on the extent
of and
appearance of the flame, performing the necessary correc
-
tions with the gas and air supply regulators as indicated in
points 4 and 5.
12) Use the adjuster to set the correct flow for the second
flame as required for the specific case. You must not
keep the burner running if the capacity is greater than the
maximum permitted amount for the boiler, or there is a risk
it could be damaged. It is therefore best to stop the burner
immediately after the twometer readings.
13) Subsequently, with the burner at maximum supply re
-
quired by the boiler, check the combustion with the special
instruments and if necessary change the adjustment pre
-
viously carried out (air and possibly gas) with just the visual
check (CO2 max. = 10 % O2 min =3% - CO max. = 0.1%
14) The air pressure switch is there to prevent the opening
of the gas valves if the air pressure is not that required. The
pressure switch must therefore be adjusted to intervene to
close its contact when the air pressu rein the burner reaches
a sufficient value. The pressure switch connection circuit
provides for auto control so it necessary for the contact to
be actually closed when the fan is stopped (no air pressure
in burner). If it is not the command and control equipment
will not go on (the burner stays stopped). If the air pressure
Summary of Contents for TBG 55
Page 2: ......
Page 75: ...75 80 000608 1041_201102...
Page 76: ...76 80 000608 1041_201102...
Page 79: ...79 80 000608 1041_201102...